申请人:深圳市力博刀具技术有限公司
发明人:张明菊 吴建军 林世民
摘要:本发明公开了一种单晶金刚石刀具加工方法以及单晶金刚石刀具。本发明包括以下步骤:1)、准备单晶金刚石材料,2)、加工硬质合金基体端部,便于单晶金刚石材料的定位和焊接,3)、将单晶金刚石材料焊接在硬质合金基体端部形成单晶金刚石刀具,4)、根据刀具外观轮廓设计要求采用激光切削法加工单晶金刚石刀具,5)、采用热化学抛光法研磨单晶金刚石刀具的刀具刃口。本发明采用激光加工单晶金刚石刀具,避免了机械加工方法造成的表面冲击沟痕;用热化学抛光法研磨单晶金刚石刀具的刀具刃口,易于研磨出高质量的刀具刀刃;激光加工时,单晶金刚石刀具表面涂覆涂层,有效防止激光的透射和反射,提高刀具加工的效率和质量。
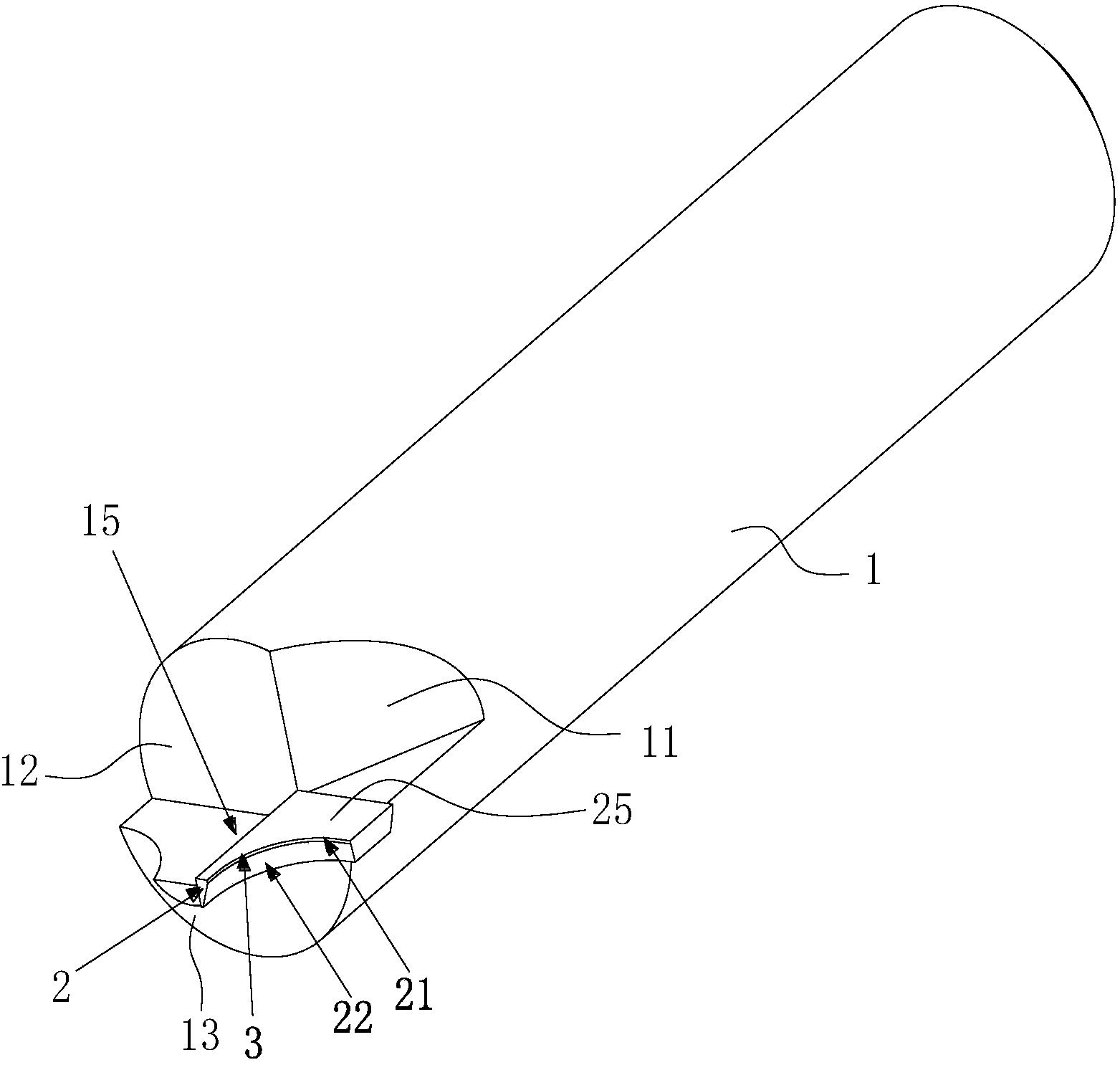
2.根据权利要求1所述的单晶金刚石刀具加工方法,其特征在于:所述步骤2)为:首先在硬质合金基体端部切削出两个相互垂直的切削面,与硬质合金基体底部平行的切削面和硬质合金基体构成焊接平台,另一个切削面为焊接面,然后在焊接平台上开设出排屑槽,并在排屑槽靠近焊接面的一侧预留出定位面,最后在硬质合金基体端部突出部分远离焊接面的一侧开设出形状为内凹弧面的避空面;所述步骤3)为:单晶金刚石刀具的底面放置在定位面上,其侧面紧贴焊接面并采用真空焊接法焊接于焊接面,与焊接面相互平行的单晶金刚石刀具的表面为前刀面。
3.根据权利要求2所述的单晶金刚石刀具加工方法,其特征在于:所述单晶金刚石材料透明、无裂痕且选定作为前刀面的单晶金刚石表面光滑、平整、无划痕。
4.根据权利要求1所述的单晶金刚石刀具加工方法,其特征在于:在进行步骤3)加工前,采用蒸汽清洗单晶金刚石刀具表面,并在单晶金刚石表面涂覆涂层,涂层覆盖整个单晶金刚石表面,涂层厚度0.1~0.2mm。
5.根据权利要求4所述的单晶金刚石刀具加工方法,其特征在于:在所述步骤4)中,激光切削加工完成后采用工业酒精擦拭去除单晶金刚石刀具表面涂层,然后用蒸汽清洗单晶金刚石刀具。
6.根据权利要求4所述的单晶金刚石刀具加工方法,其特征在于:所述涂层为白色的漆层。
7.根据权利要求1所述的单晶金刚石刀具加工方法,其特征在于:在所述步骤5)中,刀具刃口的研磨抛光方法具体为:在氢气或者惰性气体的气氛中,使用经过加热的铁质研磨棒与刀具刃口表面接触并相对滑动,单晶金刚石晶格中的碳原子扩散到铁晶体晶格中,实现对刀具刃口进行抛光。
8.一种采用权利要求1-7任一项所述单晶金刚石刀具的加工方法加工而成的单晶金刚石刀具,其特征在于:包括基体和单晶金刚石刀具,所述基体一端开设有焊接平台,该焊接平台两侧的基体上分别设避空面和排屑槽,所述避空面为内凹的弧面,其中垂直于所述焊接平台的切削面为焊接面,所述排屑槽与焊接面之间预留有定位面,所述定位面位于焊接平台所在的平面,所述单晶金刚石刀具底面放置在定位面上,其侧面紧贴焊接面并焊接于焊接面,所述单晶金刚石刀具包括第二后刀面、第一后刀面、前刀面和刀具刃口,所述前刀面与焊接面平行,所述第二后刀面、第一后刀面和刀具刃口位于远离焊接平台的一侧,所述第一后刀面与前刀面之间的交线为刀具刃口。
9.根据权利要求8所述的单晶金刚石刀具,其特征在于:第一后刀面为内凹的弧面,其弧面的母线与单晶金刚石刀具轴中心面的垂直面的夹角为第一后角,所述第一后角的范围为3~5°。
10.根据权利要求8所述的单晶金刚石刀具,其特征在于:第二后刀面为内凹的弧面,其弧面的母线与单晶金刚石刀具轴中心面的垂直面的夹角为第二后角,所述第二后角的范围为20~25°。