引言:太阳能是最重要的清洁可再生能源,预计到2040年太阳能总装机容量将占全球发电量的15%~20%[1]。根据2013年国务院出台的“光伏国八条”,2015年光伏发电装机容量将达35GW,占总装机容量的2.4%[2]。大规模利用太阳能发电的关键是制备低成本、高效率的太阳能电池。单晶硅的拉棒工艺复杂,且硅料成本较高;而多晶硅的铸锭工艺简单,且方形铸锭硅料利用率高,显著降低了成本,目前国际市场上98%以上的光伏电池均为多晶硅太阳能电池[3]。
普通平面硅片对太阳光具有一定的反射(400~1000nm波长范围内反射率为30%~40%),因此在太阳电池的生产工艺中,需要在硅片表面加工出具有减反效果的微结构(即绒面)以提高转换效率,具体有益效果包括:(1)对光进行多次反射,提高太阳光在硅片表面的吸收效率,增加短路电流Isc;(2)延长光在硅中的光程,增加光生载流子的数量;(3)曲折的绒面可增加P-N结面积,增加对光生载流子的收集率;(4)少子寿命的延长可改善太阳能电池的长波光谱响应(红光响应)。
根据美国国家可再生能源实验室(NREL,NationalRenewableEnergyLaboratory)的统计,目前单晶硅电池最高效率为27.6%(2004年美国Amonix公司创造),相较而言多晶硅电池效率最高仅为20.4%(2004年德国Fraunhofer-ISE创造)。其中一个重要因素是目前单晶硅绒面减反效果明显优于多晶硅。晶相分布均匀的单晶硅通过各向异性碱腐蚀获得均布密集的金字塔微结构,可实现10%以下的平均反射率;而多晶硅内部存在晶界,采用酸腐蚀方法制得绒面平均反射率在20%以上,从而影响电池整体效率的提升。根据“光伏国八条”,新上产能的多晶硅电池效率需不低于18%。因此对多晶硅表面制绒方法的技术特点、发展现状以及发展趋势进行分析、综述和预测是很有意义的。
本文首先分析多晶硅表面制绒的技术要求,随后根据技术原理的不同,依次对干法制绒技术、湿法制绒技术以及掩膜制绒技术进行综述,分析不同制绒技术的技术特点,随后从绒面质量、制绒效率、成本以及环保性等方面对多晶硅制绒技术进行评述,最后对多晶硅制绒技术的发展趋势进行预测。
1多晶硅制绒的技术要求
多晶硅制绒的技术要求主要包括两方面:
(1)绒面形貌。要求多晶硅表面能够均匀、全面的覆盖一层表面微结构,具体包括:①绒面微结构大小及结构参数。绒面单个微结构尺寸小有利于增加入射太阳光在微结构内部的光程,从而增强光陷阱作用,提高减反效果;②绒面分布均匀性。绒面需完全覆盖多晶硅表面,其有益性表现为:绒面均匀性越好,扩散形成的P-N结越平整,电池开压越高;绒面均匀性直接影响PEVCD镀膜时间;绒面均匀性影响丝网印刷工艺的浆料填充性以及工件的碎片率。
(2)绒面表面质量。线切割以及制绒过程会给硅片表面带来裂纹、晶格畸变等表面/亚表面损伤。裂纹面上有大量硅原子的悬挂键,易使少子复合;某些晶格位错面也含有大量悬挂键,且晶格畸变对载流子有严重的散射作用从而影响迁移率。此外,在裂纹与位错中易残存大量金属杂质原子等深能级杂质,也会严重影响Isc,进而影响转换效率。因此,制备完成的绒面需要保证其表面质量的完整性。
目前多晶硅表面制绒方法分为干式制绒技术(主要包括机械刻槽、激光加工、反应离子蚀刻加工技术)以及湿式制绒技术(主要包括酸性蚀刻及碱性蚀刻技术)。此外,基于掩膜的蚀刻技术可实现较为理想的蜂房结构(Honeycomb)绒面。
2干式制绒技术
2.1机械刻槽
通过使用V形刀具刻划实现多晶硅片表面的刻槽,从而制成微结构绒面并达到减反效果。该方法工艺难度一般,容易实现,且对环境较为友好;其缺点为:(1)要求被加工硅片具有超过200μm的硅片层,硅料成本高;(2)会在多晶硅表面带来机械损伤,需要后续腐蚀工艺去除;(3)由于硅材料的硬脆特性,长期使用需要考虑刀具的磨损;(4)较深的沟槽会影响后续电极的制作。德国Konstanz大学Zechner等[4]使用该方法在德国Eurosil多晶硅片上刻槽,基片厚度200μm,槽深40~60μm,其所制备的绒面结构以及显微观察结果如图1所示,其在350~1000nm波长范围内的平均反射率为18.4%。
2.2激光制绒
激光制绒是各向同性制绒方法,其原理是利用高能激光脉冲辐照硅片表面使局部材料急剧升温、熔化、气化,在光辐照区形成凹凸的表面微结构。激光制绒加工如图2所示,一般选用纳秒级激光,经过光学系统汇聚后在多晶硅表面进行路径扫描。
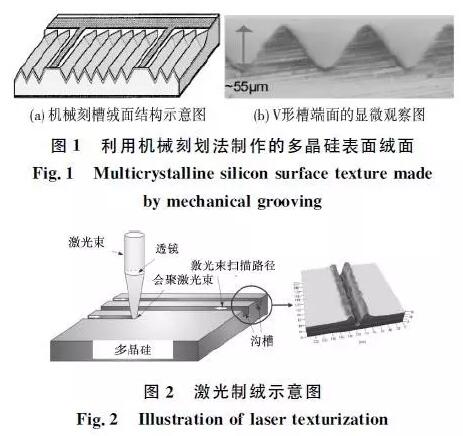
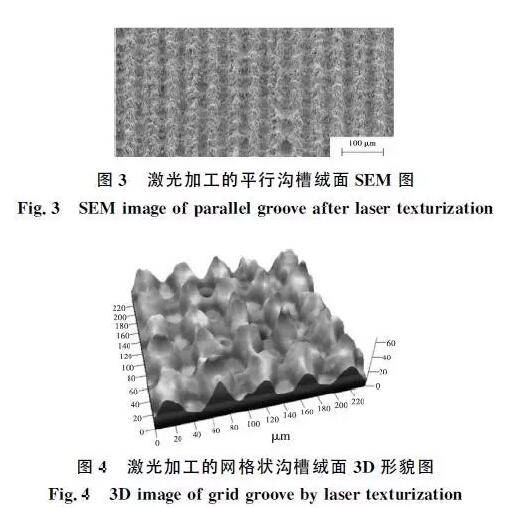
2.3反应离子蚀刻
反应离子刻蚀(Reactiveionetching,RIE)制绒工艺是将清洗后的硅片置于含有SF6、O2的氧化性混合气体中,在高频射频(Radiofrequency,RF)电场下气体辉光放电将气体电离分解为包含自由基、离子和自由电子的等离子体,综合等离子体受电场作用加速撞击硅片的物理效应和游离活性化学基的化学刻蚀作用,在多晶硅表面形成纳米级的微金字塔阵列(如图5所示),其加工装置如图6所示。
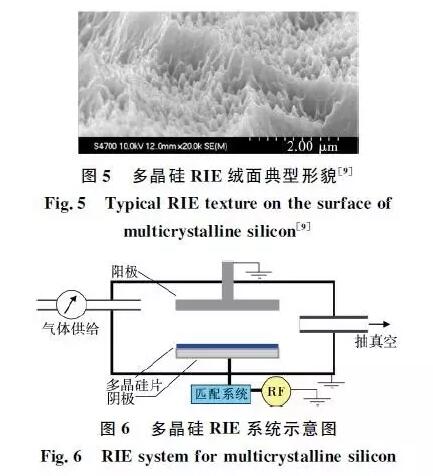


和SOF4,避免SFx+与F复合反应,从而增大F原子浓度并提升刻蚀速率。另一种生成物为硅表面的钝化层SiOxFy,此钝化层对侧壁则起到刻蚀保护作用,从而实现高深宽比的各向异性刻蚀[8]。
RIE制绒工艺的优点为:(1)绒面小且分布均匀,减反效果好;(2)通过调节电场参数、混合气体比例、蚀刻时间等工艺参数,可实现反射率在1%~20%的范围内可控;(3)可用于较薄硅片的制绒,且蚀刻厚度一般为3~5μm,节约硅料成本。
Yoo等[9]使用频率13.56MHz、功率100W的RF电源,控制SF6与O2比例为2∶5,气压24.6Pa,蚀刻15min时所制得绒面平均反射率(波长范围300~1200nm)为13.3%(绒面形貌见图5)。韩国Park等[10]在混合气体中加入Cl2,利用Cl2减慢蚀刻速率,有利于控制绒面形貌。在系统功率为120W时绒面平均反射率为14%左右(波长范围330~1100nm),但Cl2对环境有不利影响。
RIE制绒工艺的缺点为:(1)离子轰击带来的晶格损伤等表面/亚表面损伤,以及残留在表面的不可挥发反应生成物,会增加表面复合。需要通过酸洗(去除反应生成物)、碱洗(去除表面/亚表面损伤)等工艺去除损伤层。清洗会增加反射率(文献[10]中反射率平均上升2.89%)。(2)需要等离子炬及相应的控制系统,且需要低温泵和溅射离子泵相结合以满足极高的真空度要求,设备成本高。
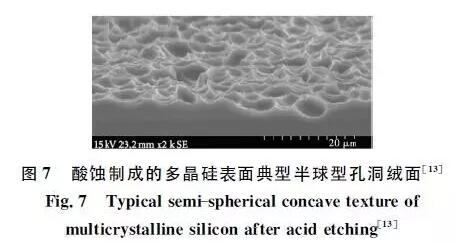

酸蚀制绒工艺优点为:(1)工艺较为简单;(2)成本相对较低;(3)腐蚀孔坑结构最先开始于线切割带来的裂纹等表面损伤处,从而在制绒同时实现表面机械损伤的去除,提高了制绒效率。2010年荷兰能源研究中心Tjengdrawira等[14]研制出效率为17.8%的多晶硅太阳能电池,其中使用了改进的基于HF/HNO3配方腐蚀液的酸蚀制绒工艺。在经过8道工序实现的1.8%的效率提升量中,酸蚀制绒工艺提供了0.3%的效率提升量。国内上海交通大学、北京交通大学、苏州大学、郑州大学、新余学院等高校以及英利能源、潞安环能、黄河光伏等太阳能企业均对多晶硅酸蚀制绒工艺进行了研究。其中郎芳等[15]以英利太阳能公司生产的硼掺杂P型多晶硅(厚度180μm,尺寸156mm×156mm)为样片进行酸蚀制绒(腐蚀液由40%的HF溶液、65%的HNO3溶液和去离子水按比例混合而成)。大量样品的测试结果表明,多晶硅绒面的反射率一般为22%~28%,反射最小的可以达到20%左右,并确定使电池效率达到最优的腐蚀深度约为4.0~4.25μm。
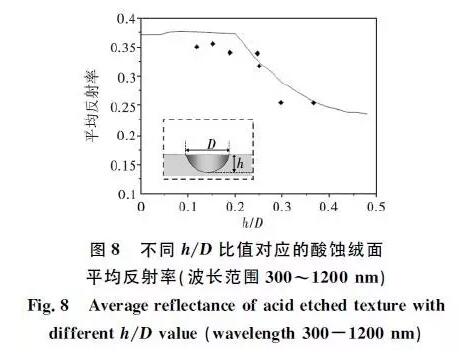
腐蚀厚度也是酸蚀制绒工艺的重要参数。考虑到节约硅料成本,目前线切割硅片厚度趋势为100μm。线切割的两个切割面会有5~7μm的损伤层。减反效果与腐蚀厚度存在相互矛盾:腐蚀厚度过小,线切割损伤层(晶体缺陷)去除不充分,表面易产生复合,少数载流子寿命减短,影响Isc以及效率;腐蚀厚度过大,则腐蚀时间长导致表面孔坑微结构尺寸增大、减反效果变差且硅片强度变弱。
酸蚀工艺的缺点为:(1)绒面稳定性不好及质量难控制,且减反效果一般;(2)所使用的HF、HNO3以及反应生成的H2SiF6与NOx废气对环境影响很大;(3)多晶硅表面生成的孔洞末端易产生晶体位错,从而导致多晶硅电池P-N结在承受一定的反向偏压时极易发生雪崩击穿(如图9所示,其中针对传统酸蚀制绒工艺的缺陷,目前对传统酸蚀制绒工艺的改进主要包括以下几方面:
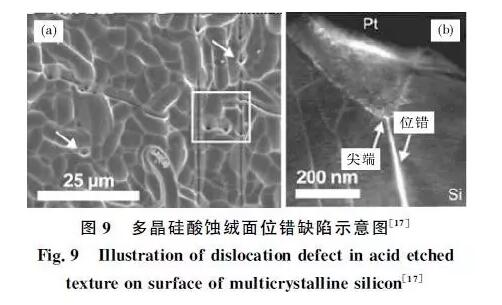
钱勇等[12]将HNO3用NaNO2替代,发现使用NaNO2时腐蚀坑的深度大于传统的酸刻蚀,且密度分布比较均匀,平均反射率下降了8%左右。③醇类等有机溶剂。其作用包括:降低反应液的表面张力,使生成气体快速逸出;增加腐蚀液在多晶硅表面的湿润性,使腐蚀液在多晶硅表面浸润的更加均匀从而提高制绒质量;溶解硅片在切割后的有机物残留;起缓冲剂的作用,控制反应速度。
(2)将电化学腐蚀工艺与酸蚀工艺相结合。采用铂丝或石墨作为阴极,多晶硅片作为阳极,含HF和有机溶剂的混合溶液作为电解液。表面硅在电解过程中失去电子,形成的空穴会减弱表面硅的硅氢键,从而使氟离子更易与硅结合,但是多孔硅结构的形成机理目前尚处于研究之中。电化学酸蚀所制备的多孔硅绒面可实现超低的反射率[18],但是其在实际应用中面临以下问题:①若先制备多孔硅层再做扩散工艺,则后续工艺中的酸洗碱洗会使多孔硅几近消失。②若先做扩散工艺再制备多孔硅层,则多孔硅层的形貌及性能的长期稳定性较差,易导致表面复合,影响少数载流子寿命[19]。因此电化学制备多孔硅绒面目前难以应用于多晶硅太阳能电池的量产化工艺中。
3.2碱性蚀刻技术
多晶硅碱蚀制绒工艺多采用一定浓度的NaOH溶液(或KOH溶液,但由于KOH成本高于NaOH,在工业生产中应用不多)在一定的温度下进行腐蚀,腐蚀化学过程为:

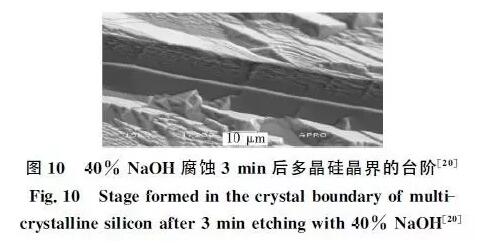

Gangopadhyay等[20]研究了不同的NaOH/NaClO配比对制绒效果的影响,发现当NaOH浓度为5%、NaOH与Na-ClO比例1∶3时,所制得绒面的平均反射率(波长范围300~1100nm)最低可达20.5%左右。王坤霞等[21]研究了在NaOH溶液中加入添加剂对绒面效果的影响,通过加入一种添加剂首次观察到了碱液刻蚀出的密集均匀分布的陷阱坑,绒面平均反射率为20.5%(波长范围400~900nm)。由于成本低、工艺简单且环境友好,碱蚀制绒工艺在多晶硅太阳能行业中有重要的潜在应用价值。
近年来多晶硅的电化学碱腐蚀得到关注,其是在腐蚀槽内将硅片接电源正极,贵金属铂片接电源负极,利用外加电场提供空穴排斥硅表面悬键的氢原子,随后失去氢钝化的硅被碱液腐蚀。电化学碱腐蚀方法的优点在于:(1)电化学腐蚀不受多晶硅的晶粒取向无规则的局限,在恒定电压下可实现各向同性腐蚀;(2)可以通过控制腐蚀电压等条件更加方便地控制反应速度[22]。Abburi等[23]在经过10min预腐蚀的多晶硅片上通过电化学碱蚀(电压40V,腐蚀温度50℃,KOH质量分数22.4%,腐蚀时间10min)得到了平均反射率最低为17%的绒面。
4掩膜辅助蚀刻技术
3.1节中阐述了绒面的减反效果随绒面微结构深宽比的增大而增强。传统的整体蚀刻难以实现高深宽比且分布均匀的绒面,由此出现了掩膜辅助蚀刻技术,其基本加工流程如图11所示:先在工件表面镀一层掩膜(图11(a)),在掩膜表面生成规则的微孔阵列(图11(b)),随后进行整体蚀刻(图11(c)),最后将掩膜腐蚀去除从而得到微结构形态及分布可控的蜂房状绒面(图11(d))。1998年新南威尔士大学赵建华等[24]首先提出了掩膜蚀刻工艺,在厚度大于200nm的SiO2掩膜上使用光刻工艺加工出规则排列的直径4μm的微孔(图12),接着基于HNO3与HF比例50∶1的腐蚀液对掩膜下面的多晶硅进行腐蚀,最后使用缓冲HF腐蚀液除去掩膜,从而加工出截面轮廓为半圆的蜂房状绒面(图13),最终完成的电池效率达19.8%。德国弗莱堡大学Volk等[25]结合SiNx掩膜、皮秒激光打孔及喷洒腐蚀法(Sprayetchingmethod)加工出深度15μm、宽度为31.5μm的蜂房状结构绒面,最低反射率可达17.5%。
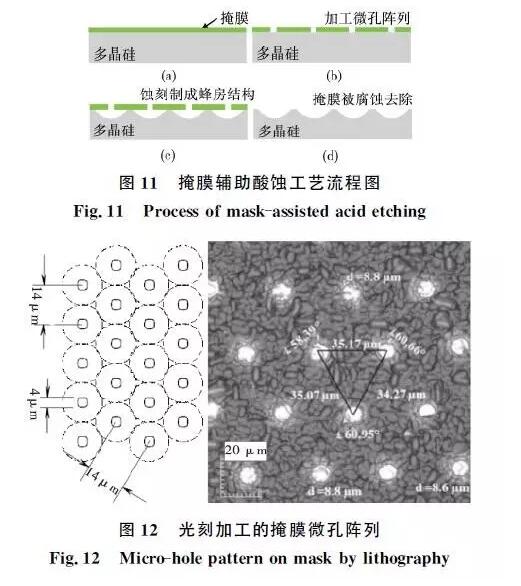
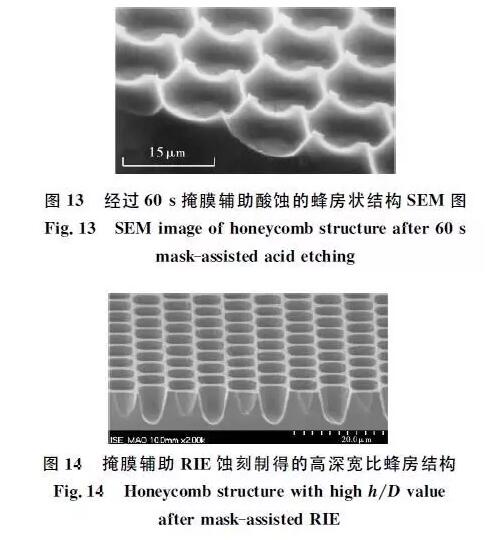
5多晶硅制绒技术综述
上述制绒方法的性能指标对比如表1所示。
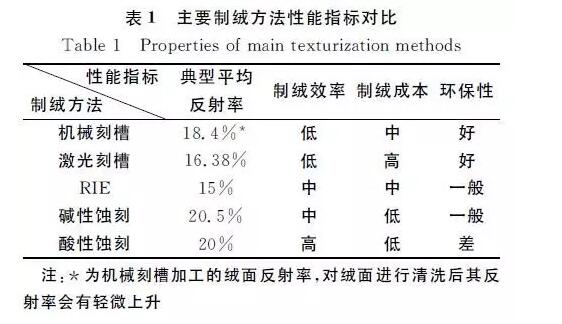
制绒成本主要包括两部分:设备成本与硅料成本。激光加工需要激光器,且由于激光烧蚀引入亚表面损伤,对硅片的厚度有一定要求。RIE需要专用设备,且反应环境要求很高的真空度,因此其设备成本很高,但是对硅片厚度不敏感,因此硅料成本较低。机械刻槽需要开发专用刻槽刀具,需要考虑刀具磨损,且对硅片厚度敏感,硅料成本高。酸蚀、碱蚀使用槽式制绒设备,结构简单,设备成本低,且在蚀刻速率可控的前提下对硅片厚度不敏感,硅料成本低。
目前的多晶硅制绒技术对环境都存在一定影响,其中机械刻槽与激光刻槽环保性最好(仅需碱性和酸性清洗液清洗破坏层及表面生成物);RIE过程中虽然SF6呈惰性且无毒,但会产生SF4等有毒气体,也需要碱性和酸性清洗液清洗破坏层及表面生成物,环保性次之;碱蚀需要大量碱性蚀刻液,也需要酸洗去除表面杂质;酸蚀大量使用剧毒的HF蚀刻液,过程中产生氮氧化物,环保性最差。综合考虑减反效果、制绒效率、加工成本等因素,尽管对环境影响很大,目前酸蚀仍然在多晶硅太阳能电池量产流程的制绒工艺中占主导地位。随着人类传统能源的日益紧缺,太阳能电池的需求不断增大,必须考虑量产过程中的环保问题,因此在保证制绒效果及量产成本的前提下,亟需一种高效、高质量、低成本、环保的多晶硅制绒方法。
6多晶硅制绒技术展望
依据对现有多晶硅制绒方法的分析,并结合多晶硅制绒研究领域最新的研究进展,本文对多晶硅制绒技术的发展趋势做如下展望:
(1)对现有量产方法的工艺进行研究,进一步提高制绒效率、绒面质量并降低成本。如Kulesza等[30]对传统酸蚀制绒工艺的HF、HNO3、CH3COOH/H2O配比进行了优化,将酸蚀时间缩减至60s。Chen等[31]发现酸蚀、碱蚀均无法完全去除线切割工序带来的多晶硅表面损伤,通过在腐蚀工艺后增加蒸汽喷射蚀刻(Vaporblastetching)工序,可完全去除表面损伤且绒面反射率仅为19%。
(2)将现有未能应用于量产的方法进行实用化研究,以提高加工效率、降低成本。其中,批量生产中多晶硅片厚度的减薄化是大的趋势,相应的干式RIE制绒方法由于具有对硅片厚度不敏感、反应速率可控、制绒效率中等、环境影响较小等优势,成为现阶段多晶硅制绒技术实用化研究的热点。
(3)探索基于其他原理的制绒方法。如吴立群等[32]提出基于超声驻波的多晶硅湿法制绒技术,利用所构造的二维超声驻波场控制腐蚀溶液中的反应粒子,可实现平均反射率为8%的低反射率绒面。
(4)复合制绒工艺。综合多种制绒原理的优势,实现绒面微结构的优化。如Liu等[33]与Basu等[34]均提出RIE与传统酸蚀结合的多晶硅复合制绒法,在酸蚀绒面上通过RIE叠加密集分布的山脊状微结构,可实现极佳的减反效果。