采用传统的机械研磨方法制造金刚石刀具时,因研磨线速度高,局部压力大,对刀具表面及刃口冲击剧烈,不可避免地会导致刀具表面产生微小沟纹和较厚的加工变质层,且刀刃锯齿度较大,从而限制了刀具质量的进一步进步。试验表明,采用机械方法研磨金刚石的表面粗糙度极限值约为3nm,刀刃锯齿度最小只能达到几十纳米的数目级,表面加工变质层厚度约为200nm。
随着超精密加工技术的不断发展以及加工精度的不断进步,对金刚石刀具的精度及质量要求也更为苛刻。研究还发现,刀具表面变质层厚度将直接影响刀具的寿命与零件的加工质量。因此,开发新型的金刚石刀具加工方法无疑是突破机械研磨方法对刀具质量限制的有效途径。
此外,如高精度轮廓仪、隧道扫描显微镜、原子力显微镜等仪器中使用的金刚石探针的前端球顶圆弧半径要求达到或小于1~2μm,精度要求高于0.1μm;加工光通讯用光栅表面的微细沟纹时,需要使用刀尖圆弧半径为0.1~3μm,并具有相当高的尺寸与外形精度的金刚石雕刻刀具。对于此类特殊要求,采用传统的机械研磨方法或者无法达到,或者加工本钱极高,因此也迫切需要开发新型的金刚石工具加工方法。
下面介绍近年来出现的四种较为典型的金刚石工具加工方法。
2 离子束溅蚀法
离子束溅蚀法是利用高能离子的轰击作用直接对被加工工件进行物理溅蚀,以实现原子级的微细加工。离子束溅蚀法的加工原理如图1所示。
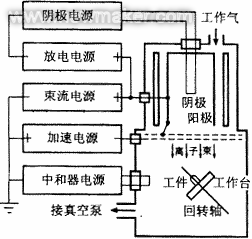
3 真空等离子化学抛光法
真空等离子化学抛光法的加工原理如图2所示。转动的磨盘被中间的高真空区分为左右两部分。左边为沉积区,采用真空等离子物理气相沉积法在磨盘表面镀上一层细晶粒氧化硅;右边为研磨区,金刚石表面处于活化状态的碳原子通过与磨盘上的氧化硅发生分子级化学反应而形成磨削作用。反应天生的一氧化碳或二氧化碳气体被真空泵抽出反应室。该方法的研磨速度为1~3000μm3/s,约每秒0.25~750个原子层,可研磨出极高质量的刃口。该方法最先被美国刀刃技术公司用于研磨超精密金刚石镜面切削刀具,该刀具可广泛用于加工各种纳米级精度的超精表面。
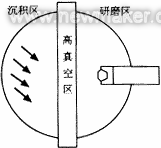
图2真空等离子化学抛光法的加工原理
4 无损伤机械化学抛光法
该方法是在NaOH溶液中加进适量的细金刚石粉和更细微(达纳米级)的硅粉,带强负静电的细微硅粉会吸附在粒度大得多的单个金刚石微粒上形成具有硅吸附层的金刚石磨料,然后将其涂敷在多孔的铸铁磨盘上对被加工金刚石进行研磨。研磨时,吸附在金刚石微粒上的硅粉一方面可阻止金刚石微粒对被加工金刚石表面的直接冲击,保护金刚石表面不会产生深度损伤,另一方面可与被加工金刚石表面发生反应并通过其微弱的磨削作用将反应层往除。该方法的磨削速度非常低,仅为每分钟一个原子层。
5 热化学抛光法
在温度为800℃时,若使金刚石表面与铁接触,金刚石晶体中的碳原子能够摆脱自身晶格的约束,扩散到铁晶体晶格中往。热化学抛光法即是运用此机理对金刚石表面进行研磨加工。
研磨时,在氢气气氛中将铁质研磨盘加热到800℃,使被加工金刚石表面与铁质研磨盘接触并相对滑动,金刚石晶格中的碳原子就会扩散到铁晶体晶格中,达到磨削金刚石的目的。进进铁晶格中的碳又与氢气反应天生甲烷并随气流散发到空气中。该方法的磨削速度为每秒40~2000个原子层。
利用该方法刻蚀金刚石,还可在其表面加工出图案和花纹,制成各种精美的金刚石工艺品。
6 结语
上述加工方法具有以下共同特点:
对被加工金刚石表面无冲击,避免了机械加工方法造成的表面冲击沟痕,使被加工表面异常光洁,其表面粗糙度可达1nm。
被加工金刚石表面与研磨盘之间的接触力非常小,易于研磨出高质量的刀刃。
被加工金刚石表面的损伤与变质层较磨削速度很低,只适用于精磨加工后的超精密抛光。
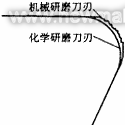
图3机械研磨与化学研磨的刀刃圆弧比较浅,可进步金刚石刀具的寿命。
此外,采用机械方法加工制成的金刚石刀具用于镜面切削时,通常存在一个“磨合期”,即需要经过一段时间的切削过程,刀具才能达到最佳加工效果。究其原因,是由于刀刃圆弧实际是由一些不规则的折线组成。研究文献表明,化学研磨方法可得到比机械加工方法光滑得多的刀具刃口圆弧(如图3所示),制成的刀具在使用过程中可消除“磨合期”,且工件表面加工质量得以大幅度进步。