摘要 日本DISCO公司的科学家们使用一种称为关键无定形黑色重复吸收(keyamorphous-blackrepetitiveabsorption,KABRA)的专利和正在申请专利的激光...
日本DISCO公司的科学家们使用一种称为关键无定形黑色重复吸收(key amorphous-black repetitive absorption,KABRA)的专利和正在申请专利的激光材料加工技术,可以将碳化硅(SiC)晶圆的生产率提升到原来的四倍,并且在提高产量的同时减少材料损耗。该技术适用于单晶和多晶锭,不管晶体层的取向如何。目前,SiC 功率器件在市场中的渗透较慢,主要是因为其产量小、且生产成本高。然而,KABRA 方法能够显著提高 SiC 器件的产量,并且应该能够使 SiC 器件作为功率器件、空间反射镜、超稳定光学模具和辐射热测量计等产品而获得更多的市场驱动力量。为了使用厚度为 20mm、直径为4英寸的晶锭生产厚度为 350μm 的SiC 晶圆,传统的使用金刚石线锯的加工工艺,切割每片晶圆需要 1.6~2.4小时,随后还要进行双面研磨工艺和最终抛光工艺,从一个晶锭生产 30片晶圆,总共需要 2.5~3.5 天的时间。虽然许多抛光工艺正在开发中,但 SiC 仍然是一种非常坚硬的易碎材料,由于在机械切割过程中形成深的起伏凹槽,所以 SiC 必须非常仔细地进行研磨。
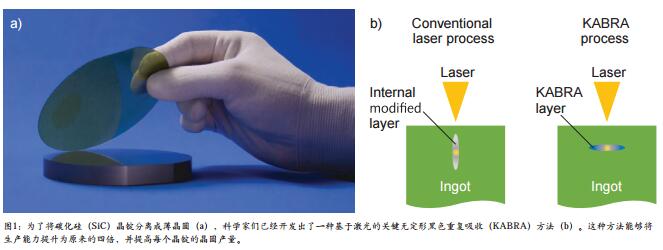
KABRA晶圆分离
从其名字上可以看出,KABRA 工艺本质上将激光聚焦在 SiC 晶片的内部,通过重复通过或“无定形黑色重复吸收”,将 SiC 分解成无定形硅和无定形碳,并形成作为晶圆分离基点的一层,即黑色无定形层吸收更多的光,从而能够很容易地分离晶圆(见图 1)。与传统工艺中的 1.6~2.4 小时相比,KABRA 工艺仅用 25 分钟来分离每片晶圆,与使用常规切片工艺、每片晶圆将带来 200μm 的材料损耗相比,KABRA 工艺在分离期间并不产生材料损耗。此外,金刚石锯片分离的晶圆需要 16 小时的最终研磨时间,这在 KABRA 工艺中也是不需要的。
总之,利用传统工艺,从一个晶锭中生产出 30 片晶圆,需要 2.5~3.5天的时间 ;而使用 KABRA 工艺,从一个晶锭中生产出 44 片晶圆,仅需要 18 小时的时间,这相当于 3~5 倍的生产率提升(或者说产能大约为原来的四倍)。