摘要 1、缸体缸体是承装所有机件的总承,缸体结构共同点是一个近似六面体箱式结构,薄壁,加工面、孔系较多,属典型的箱体内零件,主要加工有缸孔、主轴承孔、凸轮轴孔等,有润滑油道、冷却水道、安...
1、缸体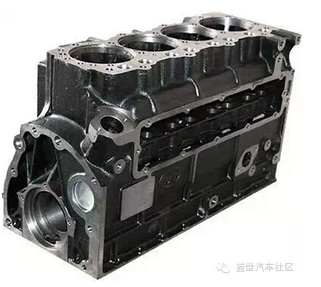
缸体是承装所有机件的总承,缸体结构共同点是一个近似六面体箱式结构,薄壁,加工面、孔系较多,属典型的箱体内零件,主要加工有缸孔、主轴承孔、凸轮轴孔等,有润滑油道、冷却水道、安装螺孔等多种孔系,有多种联结、密封用凸台和小平面,它们的加工精度直接影响发动机的装配精度和工作性能,同时,为提高机体刚度和强度,还分布有许多加强筋。
缸体孔加工:采用粗镗、半精镗及精镗、珩磨方式加工。主轴承孔的加工:一般采用粗加工半圆孔,再与凸轮轴孔等组合精加工。凸轮轴孔的加工:一般采用粗镗,再与主轴承孔等组合精加工。挺杆孔的加工:一般采用钻、扩(镗)及铰孔的加工方式。主油道孔的加工:传统的加工方法是采用麻花钻进行分级进给方式加工,其加工质量差、生产效率低,目前工艺常采用枪钻进行加工。
2、缸盖
缸盖形状一般为六面体,系多孔薄壁件,其上有气门座孔、气门导管孔、各种光孔及螺纹孔、凸轮轴孔等。
缸盖的平面加工一般采用机夹密齿铣刀进行铣削加工,孔系一般采用摇臂钻床、组合机、加工中心等设备进行钻、扩、铰方式加工;导管及阀座采用冷冻或常温压装方式进行压装,常温压装过程中一般采用位移-压力控制法对装配过程进行控制。
孔加工是缸体、缸盖的难点所在,孔系加工一般采用钻、扩、铰、镗削、攻丝等加工方式。孔加工对刀具的要求极高,任何刀具折损,崩刃,孔精度不良等问题都会影响孔加工的加工精度,在这里小编介绍一款读者提供的采用OSG刀具进行加工的解决方案:
孔加工案例
某发动机厂采用OSG的VP-DC-MT(DIN标)/VP-DC-HT(JIS标)/VO-DC-HT(JIS标 内冷)系列刀具,该刀具具有V (TICN) 涂层、VP-DC-HT 采用CPM粉末高速钢材质、0°前角式样加大刃部强度、对应高速加工,切削速度达 30 m/min。用来加工铸铁缸盖的孔系,取得较好的效果。
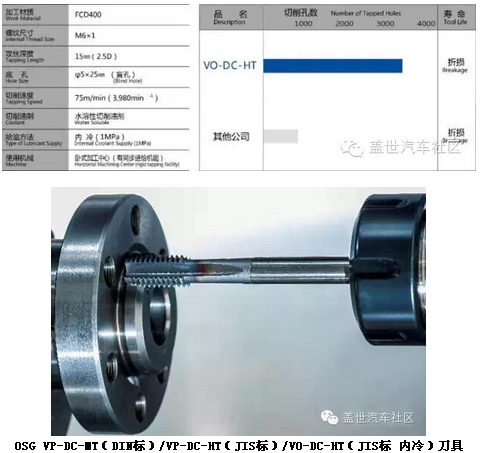
在铝合金发动机零部件加工过程中,切削液边界润滑性能是改善刀具磨损和控制表面质量的重要指标。切削液优异的边界润滑性,以及其强效的化学附着力可在工件和刀具间产生承压油膜,减少磨料磨损,吸收切削热,并使得切屑迅速脱离刀具前刀面,避免切削刃产生积屑瘤和粘结磨损。结合我们前文所提到的“极压润滑性能”,使刀具始终处于相对理想的切削条件下,从而达到控制尺寸公差稳定和提高表面质量的效果。在用于铝合金工件的高精度加工时,其优异的边界润滑特征表现的尤为出色。
切削液案例
下面是国内一家知名汽车厂商在加工缸盖挺柱孔时使用奎克切削液的一个实际案例。加工工艺及加工参数:
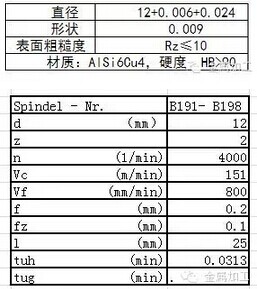
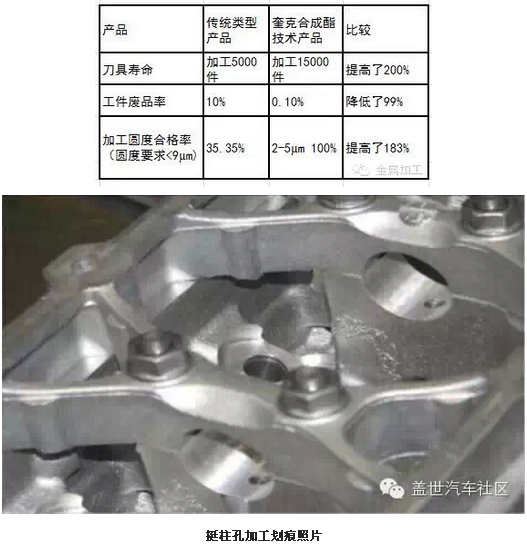
3、曲轴
曲轴是汽车发动机的中心零件,在发动机中承受着交变反复的弯曲和扭转载荷,故绝大多数毁于疲劳断裂或产生偏磨而较快磨损,是影响发动机寿命的重要零件。但其形状相对细而长,易变形,连杆颈和主轴颈不在同一根轴线上,在加工中易产生不平衡的现象,因而曲轴的数控加工不论对机床设备还是对数控软件都提出了比较严格的要求。
曲轴加工软件案例
现在曲轴的生产中多采用具有双主轴的车铣复合机床上对其数控加工。而hyperMILL®对于曲轴任何部位的数控编程,无轮曲轴颈、连杆轴位置的车削、曲柄处的铣削还是油孔处的多轴钻削,在hyperMILL®中都可以轻易实现。并且曲轴在试制阶段多采用的棒料开粗,hyperMILL®的任意毛坯粗加工功能可以按任意角度进行加工,并能继承上次结果毛坯,以达到均匀的余量。投影精加工则是曲柄位置加工的优先选择,它可以实现多轴定位精加工,刀路均匀而整齐。曲柄颈和连杆颈处一般需要车削后留有余量以进行后续的磨削,无论粗车还是精车,在hyperMILL®中只要选择对应曲线后更改参数即可实现。
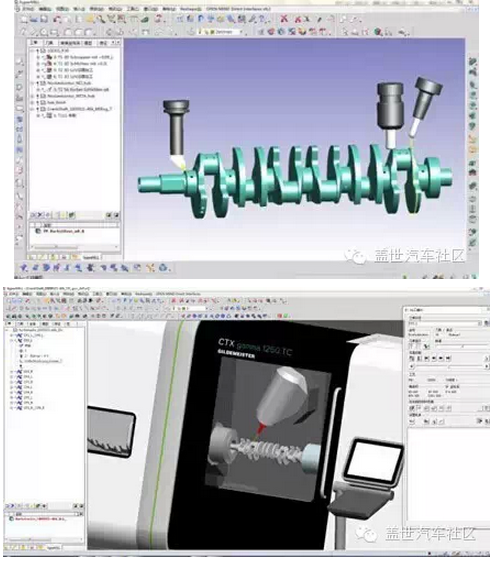
曲轴的中心孔是曲轴加工过程的重要定位基准,曲轴常见的中心孔加工方式为几何中心孔和质量中心孔。
曲轴技术要求较高,其轴颈直径公差一般为IT6级公差,轴颈表面粗糙度为Ra0.4~Ra0.2μm,因此为保证产品质量要求,曲轴在经过粗加工后,必须对所有轴颈进行磨削的精加工,以提高轴颈精度和降低表面粗糙度。曲轴轴颈传统的磨削方法分半精磨和精磨两个阶段,但随着毛坯制造技术的发展和粗加工设备加工精度的提高,目前大多数曲轴加工厂已取消了半精磨工艺,这样可以缩短曲轴的加工流程,同时也降低了曲轴的生产成本。
对于曲轴外铣,金属加工小编推荐一款山高的非标铣刀,切削轻快,刀具简单易用。
曲轴外铣案例
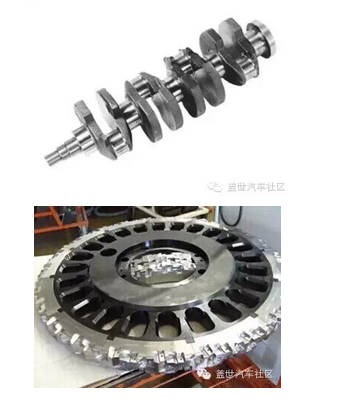
机床: 数控曲轴外铣专机
材料:42CrMo4 HB280
刀体直径: D700mm (非标)
12个刀夹
168个刀片(3种类型)
刀片:SNHW1204XXEN8-MD07
LNHW150343TN4-MD15
LNHW1204S30EN8-MD07
切削参数:
Vc=154 m/min
Vf=230mm
Ap=2-5mm
Ae=39.8mm
刀片寿命:150分钟/刃
曲轴油孔一般孔径较小、深度较深,属深孔加工,因此加工难度较大,曲轴油孔加工目前已逐渐采用枪钻加工,枪钻用来加工深孔的深度一般可以做到枪钻直径的100 倍以上,另外枪钻加工可以达到的精度很高,视不同的被加工材料和选用不同的切削用量可以一次加工出精度很高的孔。为提高曲轴的强度、增加表面耐磨性,曲轴一般需要对轴颈表面、圆角等处进行强化处理,常用的强化工艺有淬火、滚压、氮化等,由于淬火适应范围广、效率高、强化效果好,因此淬火成为目前主要的强化工艺。
4、凸轮轴
凸轮轴是发动机中配气机构中的重要部件,在发动机工作循环中,它合理地控制进排气门的开启、关闭时间和开合量,使经过压缩的燃油混合气充分燃烧,推动活塞运动做功,然后将废气排出燃烧室,因此它影响着发动机的动力性、经济性和排放。
凸轮轴属于细长轴类零件,刚性差、易变形,要准确控制发动机的进排气门定时开启和关闭,凸轮应具有很高的轮廓精度、相位角度要求和良好的耐磨性能及整体刚性。因此,其轴颈和凸轮的加工成为整个凸轮轴加工工艺的重点,其加工多以车削、铣削和磨削工艺及表面强化(淬火、喷丸、氮化)等辅助工艺相结合。
凸轮轴颈传统加工流程:仿形多刀车→粗磨→淬火→半精磨、精磨→靠模砂带抛光,目前的加工流程:CNC无靠模外铣机床铣削凸轮→淬火→CNC无靠模磨床CBN砂轮磨削凸轮→柔性抛光凸轮。
谈到凸轮轴必须提到的一个具有革命性的新技术就是装配式凸轮轴。它与传统整体式凸轮轴相比,具有质量轻、加工成本低、材料利用合理等优点。
装配式凸轮轴是将凸轮、空心轴体和支撑轴颈等分别进行材料优化匹配,分体精密加工,再以某种连接方式装配而成,凸轮一般采用碳钢或粉末烧结材料,轴体则采用中空无缝钢管,碳钢凸轮经冷、温精密锻造成形,并进行高频淬火或渗碳处理,凸轮也可由粉末烧结材料通过精密烧结成形技术烧结成形,也有采用铝合金做轴体的。
装配式凸轮轴主要工艺流程包括:压装凸轮→校直→加工两端面中心孔→车轴颈→磨轴颈→磨凸轮→凸轮淬火→去毛刺→校直轴颈→凸轮轴颈及凸轮抛光→清洗→综合检测。
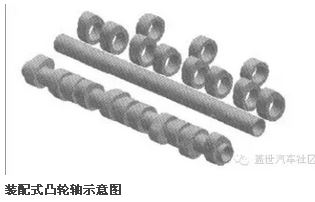
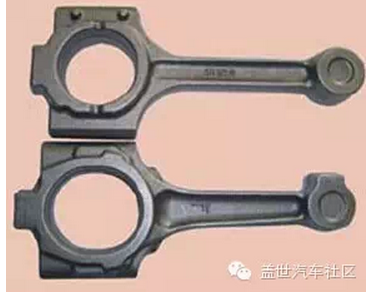
连杆外形不规则而且较复杂,不易实现定位,大小头是细长的杆身连接,容易变形;尺寸公差、形位公差,表面粗糙度等要求较高。连杆的加工工序遵循先面后孔,先基准后其它的原则。连杆是一个刚性比较差的零件,因此定位夹紧应减少变形对加工精度的影响。
连杆涨断加工技术(也称连杆裂解)作为一项制造新工艺,并逐渐应用于大规模生产领域。连杆裂解是对连杆杆身和连杆盖结合面进行无屑断裂剖分加工的新技术,具有构思新颖、操作经济、效益显著的特点。
其工艺过程的主要特点是:
(1)大头孔加工。传统工艺一般是切断后对大头孔进行拉削,或者在切断前将它加工成椭圆形,因为是断续加工,振动大、刀具磨损快、刀具消耗大。而涨断工艺将大头孔加工成圆形 。
(2)连杆体、盖分离。传统工艺采用拉断(或铣断、锯断)法,而涨断工艺是在螺栓孔加工之后涨断。采用涨断工艺后,连杆与连杆盖的分离面完全啮合,改善了连杆盖与连杆分离面的结合质量,所以分离面不需要进行拉削加工和磨削加工。由于分离面完全啮合,将连杆与连杆盖装配时,也不需要增加额外的精确定位,如螺栓孔定位(或定位环孔),只要两枚螺栓拧紧即可,这样可省去螺栓孔的精加工。
(3)结合面的加工。传统工艺是在拉断后还要磨削结合面,且连杆体/盖的装配定位靠两个螺栓孔中的定位孔和螺栓的定位部分配合来定位,所以对螺栓孔与其分离面的垂直度和两螺栓孔的中心距尺寸都有严格的要求。尺寸误差导致连杆与连杆盖装配后有残余应力留在连杆总成。
(4)螺栓孔加工。涨断工艺加工的连杆体/盖的装配定位是以涨断断面作定位,而传统工艺加土的连杆体/盖的装配定位靠两个螺栓孔中的定位孔和螺栓的定位部分配合来定位,所以对螺栓孔和螺栓的精度要求都很高。采用涨断工艺加工连杆时,精度要求大大降低,两个螺栓孔可不同时加工,这样为多品种加工创造了便利条件。连杆大头孔采用涨断工艺后,它们的分离面是最完全的啮合,所以没有分离面及螺栓孔加工误差等影响。
(5)螺栓装配。通过带振动式储料器的螺栓进料装置、分离装置以及带导管和气嘴的进料器,将螺栓进料、安装,并用安装在齿条式安装支架及液压驱动垂直滑台上.的快速BOSCH拧紧机进行预拧紧,当拧紧至某一设定扭矩处时,通过设有等待功能的装置松开螺栓,清理结合面,最后拧紧螺栓至要求。
连杆涨断技术在连杆加工发展史上,涨断工艺的发明具有划时代的意义。目前,连杆涨断加工工艺在国内已被广泛使用。上海大众、一汽大众、华晨和奇瑞等厂家均采用此种连杆工艺,一些专业的连杆制造厂家也开始采用此工艺。国内的装备制造厂家已制造出相关的专用设备。