申请人:东南大学
发明人:陈锋 陈培架 余新泉 张友法 曾从远
摘要:本发明涉及一种挤压浸渗制备金刚石-Al复合材料的方法,具体步骤:首先,将金刚石颗粒填入模具,保持模具竖直并振实,使金刚石颗粒自由堆积;其次,将模具加热到一定温度并保温,旋紧上盖,使金刚石颗粒在受压状态下保持紧密堆积状态;然后,通过加压将铝液渗入金刚石颗粒间隙,同时向模具上盖处喷雾冷却,使铝基体顺序凝固制得金刚石-Al复合材料;最后,通过热处理改善金刚石-Al界面结合。所用金刚石粒径为125-250μm,表面不镀膜,基体为铝硅合金。本发明无需真空或气氛保护系统;特制模具在整个制备流程中提供压应力,保证金刚石颗粒紧密接触;顺序凝固使铝基体致密;后期热处理能改善金刚石-Al界面结合。复合材料热导率优异,适合工业化生产。
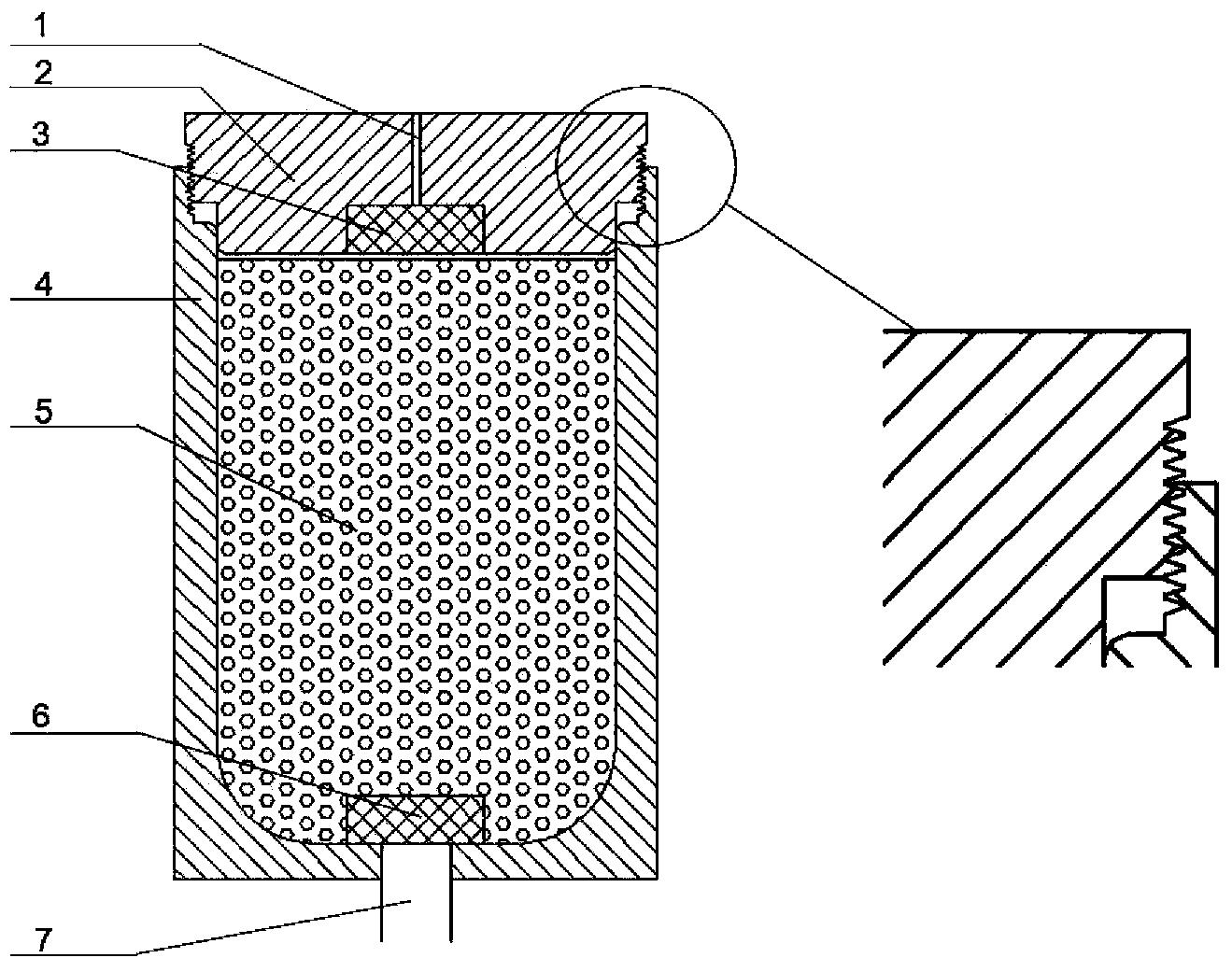
2.根据权利要求1所述的挤压浸渗制备金刚石-Al复合材料的方法,其特征 在于:所述浸渗模具包括排气口(1)、上盖(2)、上盖多孔陶瓷(3)、圆筒形模 腔(4)、进液口多孔陶瓷(6)、进液口(7);该模具以圆筒形模腔(4)为主体, 上部采用螺纹连接的上盖(2)封口,模腔中填充自由堆积金刚石颗粒(5);在 圆筒形模腔(4)下底面设置进液口(7),并在进液口(7)上安放进液口多孔陶 瓷(6),进液口多孔陶瓷(6)主要起到过滤铝熔体和阻止金刚石颗粒从进液口 (7)漏出的作用;在上盖(2)设置排气口(1),并在排气口(1)下部安放上 盖多孔陶瓷(3),上盖多孔陶瓷(3)主要起到排气和阻止金刚石颗粒从排气口 (1)漏出的作用。
3.根据权利要求1所述的挤压浸渗制备金刚石-Al复合材料的方法,其特征 在于:所述BN脱模剂,成分为85wt%BN粉末,5wt%速溶Na2SiO3粉末,10wt% 无水乙醇。
4.根据权利要求1所述的挤压浸渗制备金刚石-Al复合材料的方法,其特征 在于:所述的金刚石颗粒为MBD4型,表面不镀覆,粒径为125-250μm。
5.根据权利要求1所述的挤压浸渗制备金刚石-Al复合材料的方法,其特征 在于:所述铝熔体为铝硅合金,Si含量在7wt%~12.5wt%之间。
6.根据权利要求1所述的挤压浸渗制备金刚石-Al复合材料的方法,其特征 在于:所述模具预热,预热温度为610-650℃,保温时间为1-2h。
7.根据权利要求1所述的挤压浸渗制备金刚石-Al复合材料的方法,其特征 在于:所述压力浸渗,压力为1-2MPa。
8.根据权利要求1所述的挤压浸渗制备金刚石-Al复合材料的方法,其特征 在于:所述热处理,热处理温度为510-550℃,保温时间为2-4h。