摘要 超硬材料分会四届六次常务理事(扩大)会议暨海峡两岸超硬材料发展座谈会于2014年4月23日在云南省景洪市召开。会议中,来自南京航空航天大学机电学院的傅玉灿教授作了关于“航空航天中的...
超硬材料分会四届六次常务理事(扩大)会议暨海峡两岸超硬材料发展座谈会于2014年4月23日在云南省景洪市召开。会议中,来自南京航空航天大学机电学院的傅玉灿教授作了关于“航空航天中的磨削加工技术”的专题报告。
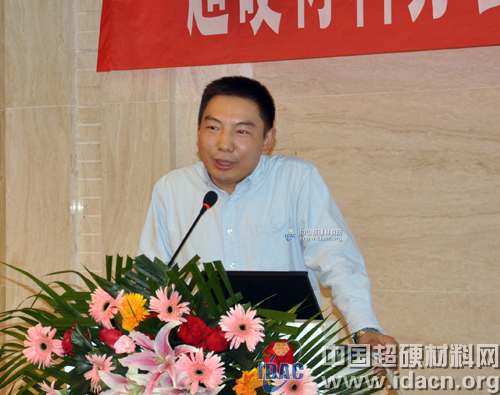
南京航空航天大学机电学院 傅玉灿教授
报告主要从“需求分析”、“存在问题”与“发展现状”等三个方面系统地阐述了超硬材料在航天航空领域的磨削加工应用现状。
报告指出:航空航天产品“轻、高、长、低、快” 的制造要求是难加工材料发展的强大推动力。随着航空航天产品零部件性能要求不断提高,在高强韧材料方面,出现了钛合金、高温合金、金属间化合物等新材料;在高硬脆材料方面,出现了先进陶瓷、光学玻璃等新材料;而在复合性能材料方面,出现了树脂基复合材料、陶瓷基复合材料、金属基复合材料等新材料。
超硬材料在航天航空领域的磨削加工应用主要集中在叶片、盘、轴、齿轮、喷嘴等飞机发动机零部件、机载精密仪器零部件、飞机起落架零部件等几个主要方面。
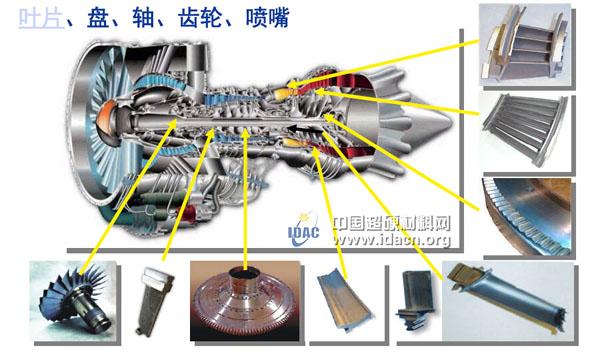
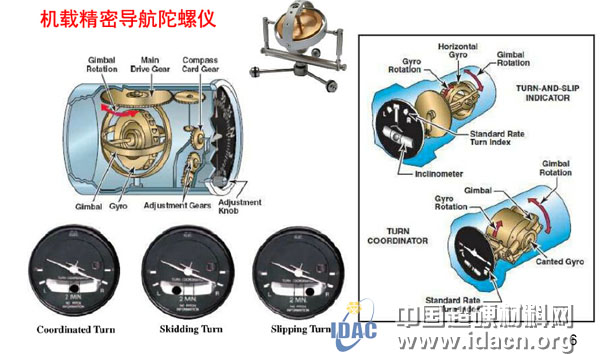
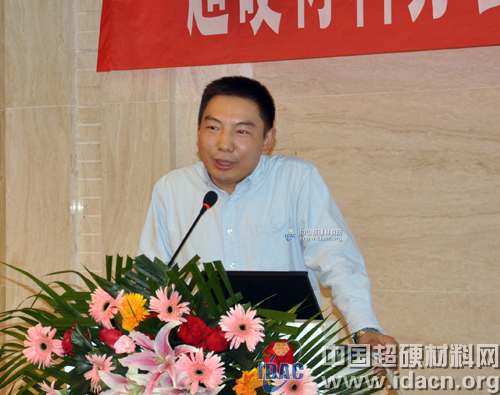
南京航空航天大学机电学院 傅玉灿教授
报告主要从“需求分析”、“存在问题”与“发展现状”等三个方面系统地阐述了超硬材料在航天航空领域的磨削加工应用现状。
报告指出:航空航天产品“轻、高、长、低、快” 的制造要求是难加工材料发展的强大推动力。随着航空航天产品零部件性能要求不断提高,在高强韧材料方面,出现了钛合金、高温合金、金属间化合物等新材料;在高硬脆材料方面,出现了先进陶瓷、光学玻璃等新材料;而在复合性能材料方面,出现了树脂基复合材料、陶瓷基复合材料、金属基复合材料等新材料。
超硬材料在航天航空领域的磨削加工应用主要集中在叶片、盘、轴、齿轮、喷嘴等飞机发动机零部件、机载精密仪器零部件、飞机起落架零部件等几个主要方面。
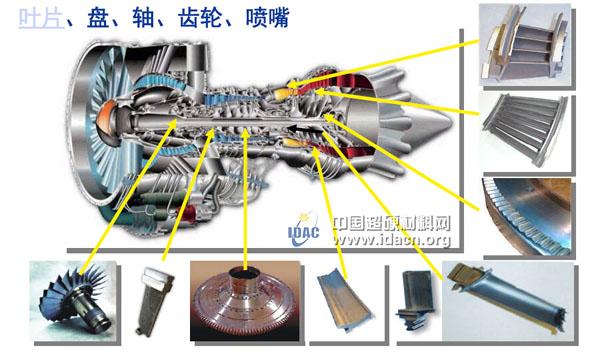
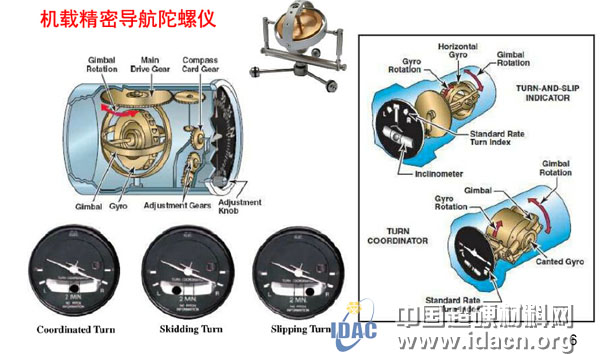
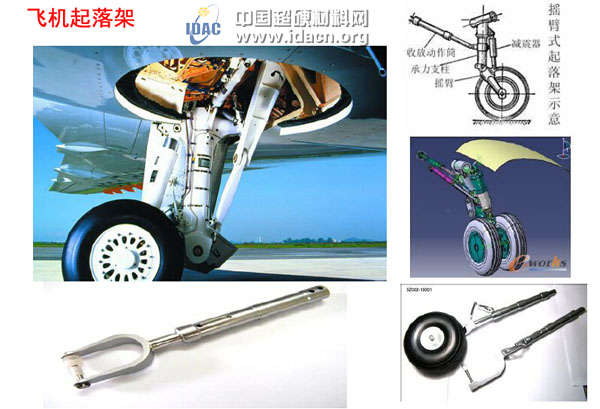
为了更好地解决航空航天领域新材料加工磨削技术要求的不断提高,中国参与了欧盟第五框架项目(航空发动机新型材料先进磨削项目)。该项目要求未来航空发动机新材料先进磨削能达到“磨削成本降低40%、磨削效率提高50%”的要求。并且要求航空发动机高强韧性材料难加工材料零件的加工要以磨削加工为最终加工作业。
但在现阶段,航空航天新材料先进磨削方面还存在着加工效率低、加工成本高、加工质量不稳定等难题。存在的主要问题包括:传统刀具/磨具材料的耐磨性和寿命低、超硬材料工具可胜任加工,但未充分发挥作用、加工区换热问题尚未解决、刚玉、碳化硅砂轮磨削,材料去除率,磨削比低等。
针对以上问题,进一步开发高效磨削潜力的研究构想:
对策1.尽可能提高砂轮的锋利度大幅度降低磨削比能以减少产生的磨削热(具有优化地貌的砂轮设计与制造)
对策2.尽可能强化弧区换热以最大限度地疏导已经产生的积聚在弧区的磨削热(高效加工中的强化换热技术)
但在现阶段,航空航天新材料先进磨削方面还存在着加工效率低、加工成本高、加工质量不稳定等难题。存在的主要问题包括:传统刀具/磨具材料的耐磨性和寿命低、超硬材料工具可胜任加工,但未充分发挥作用、加工区换热问题尚未解决、刚玉、碳化硅砂轮磨削,材料去除率,磨削比低等。
高效磨削技术的应用
“高效磨削”即打破传统切/磨削加工“粗切精磨”的分工模式,达到加工效率、质量双提升,加工成本下降的目的。“高效磨削技术”现在主要划分为:缓进深切磨削(Creep Feed Deep Grinding)、高速快进磨削(High Speed Stroke Grinding)、高效深切磨削(High Efficiency Deep Grinding)、高效砂带磨削(High Efficiency Belt Grinding)。
缓进深切磨削:加大切深,砂轮表面上同时参与切削的磨粒数增加。其优势在于,能保持单颗磨粒切除负荷不变的条件下大幅度提高磨削效率。具有磨削效率高、单颗磨粒的负荷减小、磨削温度低等优点。
高速快进磨削:即提高砂轮线速度和进给速度,单位时间内参与切削的磨粒数增加。其优势在于:即获得高效率又达得高精度。还有磨削力小、磨削效率提高、砂轮使用寿命提高以及被加工工件表面粗糙度低、表面完整性好等优点。
高效砂带磨削:籍磨料相对有向合理排布,大幅度提高磨具的静态风力度。其优势在于:磨削比能低、热效应低、可在不加冷却液的条件下实现高效作业。
“高效磨削”即打破传统切/磨削加工“粗切精磨”的分工模式,达到加工效率、质量双提升,加工成本下降的目的。“高效磨削技术”现在主要划分为:缓进深切磨削(Creep Feed Deep Grinding)、高速快进磨削(High Speed Stroke Grinding)、高效深切磨削(High Efficiency Deep Grinding)、高效砂带磨削(High Efficiency Belt Grinding)。
缓进深切磨削:加大切深,砂轮表面上同时参与切削的磨粒数增加。其优势在于,能保持单颗磨粒切除负荷不变的条件下大幅度提高磨削效率。具有磨削效率高、单颗磨粒的负荷减小、磨削温度低等优点。
高速快进磨削:即提高砂轮线速度和进给速度,单位时间内参与切削的磨粒数增加。其优势在于:即获得高效率又达得高精度。还有磨削力小、磨削效率提高、砂轮使用寿命提高以及被加工工件表面粗糙度低、表面完整性好等优点。
高效砂带磨削:籍磨料相对有向合理排布,大幅度提高磨具的静态风力度。其优势在于:磨削比能低、热效应低、可在不加冷却液的条件下实现高效作业。
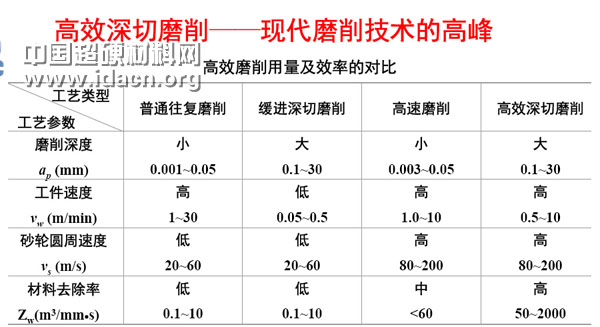
航空航天类难加工材料高效加工存在的主要问题:
1.磨削热的产生问题
2.磨削弧区的换热问题
1.磨削热的产生问题
2.磨削弧区的换热问题
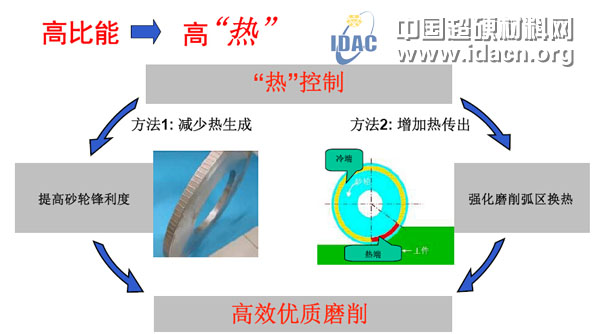
针对以上问题,进一步开发高效磨削潜力的研究构想:
对策1.尽可能提高砂轮的锋利度大幅度降低磨削比能以减少产生的磨削热(具有优化地貌的砂轮设计与制造)
对策2.尽可能强化弧区换热以最大限度地疏导已经产生的积聚在弧区的磨削热(高效加工中的强化换热技术)