晶片制备工艺中金刚石线是耗费较高的一个因素,研究并分析影响线锯寿命的机能就至关重要。本论文讨论了线锯表征方法并研究了金刚石线的磨损情况。研究结果表明:金刚石线和加工材料间的相互作用引起的切割线磨损(CWW)以及金刚石线本身的作用而引起的非切割线磨损(NCWW)是金刚石线磨损的两种主要形式。在新型实验装置上,NCWW被降低至最小,显著改善了金刚石线的切割性能。
关键词:金刚石线,磨损,切割,机械优化
引言:
光伏设备用碳化硅晶片的制备工艺近年来正经历着一场技术革新,以金刚石线加工为代表,也即固结磨粒锯切(FAS)技术正替代浆加工和自由磨粒锯切(LAS)技术。这种技术革新不仅影响着碳化硅晶片的多线锯加工工艺,还改变着光伏产业链中其他碳化硅切割工艺,如晶锭修整等。FAS技术中耗费较高的就是金刚石线锯损耗。金刚石线的最大使用时间也即线寿命主要受线磨损影响。本论文主要研究金刚石线的磨损对制造设备的影响。
论文分为以下部分:首先介绍金刚石线在整个耗费中的占比;然后分析金刚石线磨损的实验方法,主要是制造设备方面线损的特征和原因,最后介绍了经设备优化的高性能金刚石线。
金刚石线在整个耗费中的占比
图一为金刚石线设备耗费计算。(a)为晶片制造总费用(从结晶到质检);(b)为生产线加工耗费(非碳化硅);(c)晶片耗费分布比例。
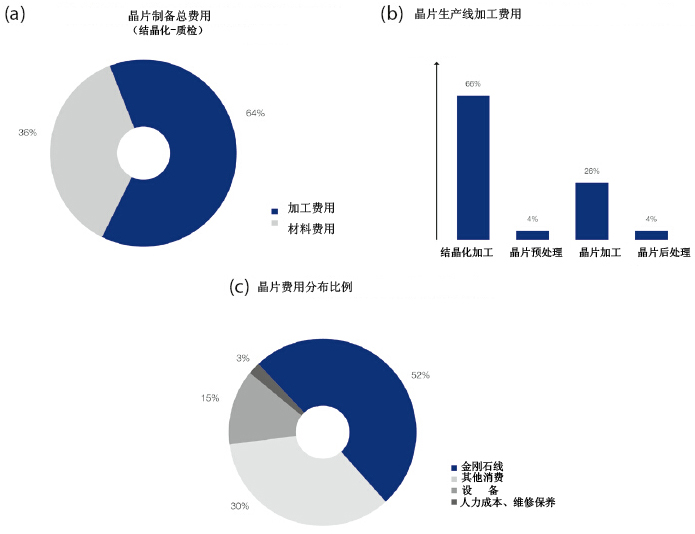
图一:成本计算
然后,根据一条完整的晶片生产线加工步骤将加工费用细分为几个部分(图一b)。为避免繁琐,修整、磨削和上胶等程序都归为预晶片处理;清理、测量和打包归为后晶片处理;图表中可以看出除了结晶化工艺处理是高能耗外,晶块切割成片是最大的耗费之一,占整个加工耗费的四分之一。
晶片处理费用中,金刚石线占据将近一半的费用比例(图一c)。本实验中金刚石线占整个费用的比例为9%。根据pvinsights.com的数据统计,2013年8英尺单晶碳化硅晶片的平均价格为1.2美元。根据晶片制造商的利润,金刚石线耗费占每片晶片的8%-9%。由此可以看出降低金刚石线耗费对于晶片费用的影响。如果一条线锯的线耗费缩减10%,那么一台年产量350000片的机器就可以节省开支35000美元。
金刚石线性能
晶片加工中,金刚石线消耗可以通过切割一块晶片所用的线长(m/片)或单位长度的线长切割出的晶片面积(cm2/m)来量化。第二个定义有两点好处:不依赖晶片面积且易转化为其他切割工艺参数,如晶锭修整等。因此,本论文中主要讨论金刚石线性能,而不讨论线消耗。
为最大化金刚石线性能,延长线的操作时间(线寿命)就十分必要;在实际生产过程中,就是要重复多次使用同一根线来完成切割。向前进级几百米后,调换线的进给方向;在向后进给几百米后,再次调换进给方向。
线性能设置的过高,会出现切割精度下降和线断裂现象。最适宜的线性能基本保持在切割表面的规格和线成本之间。
线性能增大引起的切割精度下降的机能尚未研究清楚,但作者认为金刚石线的磨损是最主要的限制因素。因此,为了定义最适宜线性能的工艺,有必要建立对线磨损进行表征的分析方法。
金刚石线分析方法
一种最直接的金刚石线分析方法是利用测微规测量线直径,这是一种无损测量方法,测量结束后线还可以继续用来切割。图四和图六为该方法测得的数据结果。
对于晶片加工,线直径可以由晶片厚度获得;为此,需要知道线的外径和晶片表面的距离。假设该距离保持常量,那么根据晶片厚度的变化就可以求得线的外径,如图三和五所示。
利用光学显微镜对金刚石线进行观察。在实际操作中,为获取线状态的高分辨率图,通常采用SEM进行观察法。研究线磨损的测量技术如图二、四、六所示。
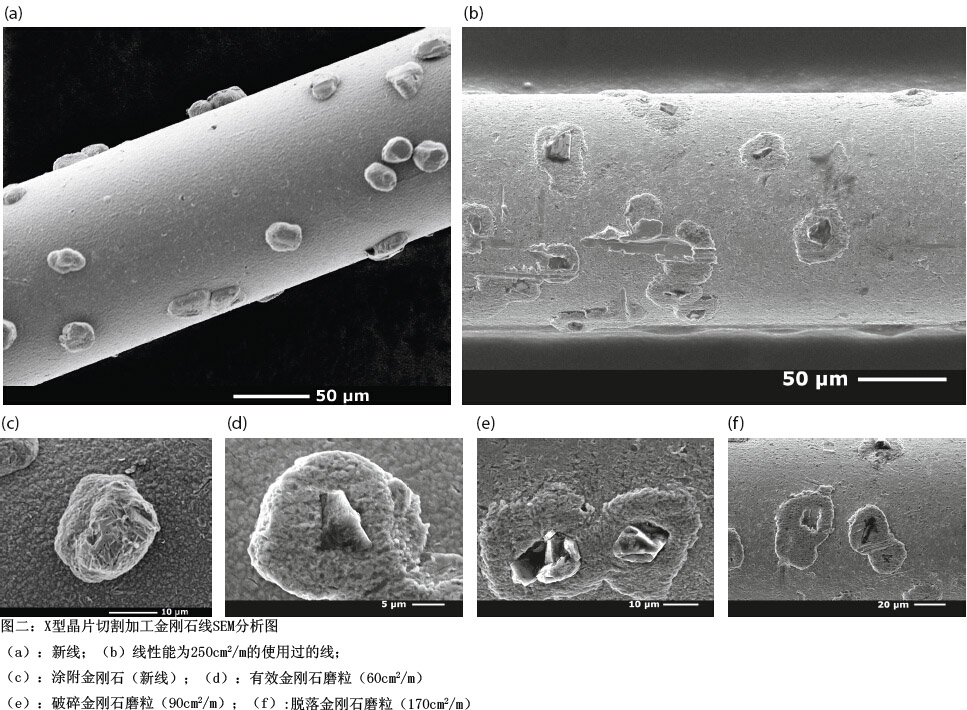
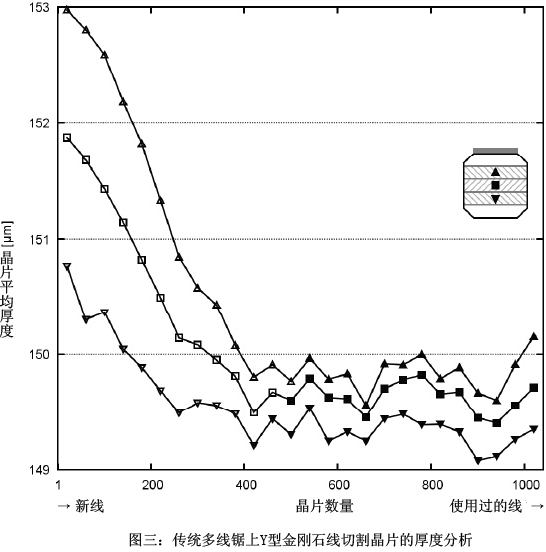
为研究金刚石线的磨损特征,实验对X型商用金刚石线进行SEM分析,结果如图二所示。图二(a)中,利用一个崭新的金刚石线采用上述进给方向对四个碳化硅晶片进行切割加工,线性能为250cm2/m。图中最后一排为持续切割阶段的金刚石线特写。
随着线性能的增加,线外径变小。这种变小和使用过的金刚石线特征相关联(图二b,d,e,f),如变形、金刚石突起的脱落和金刚石破碎;同时切削力也增大。这些现象都和金刚石线的磨损有关。
金刚石线磨损的原因
以上金刚石线磨损描述留下了一个最基本也是最重要的问题:什么机能引起了线磨。文献中除了提及线磨对晶片制造成本的重要性外,并无涉及引起线磨的机能。此外,还有一个问题就是跟金刚石线的机械接触在何处发生。切割过程本身会使金刚石线和被切割材料发生接触;其他接触还有:线和导丝辊上面的涂附材料接触;线和滑轮、缠线轴发生的接触;以及缠线时线本身相互间的接触。切割过程中线和被切割材料发生的磨损称之为切割线磨损(CWW),其他情况引起的磨损称之为非切割线磨损(NCWW)。很显然,为降低线的耗费,在切割性能确定的参数条件下,CWW应该保持最小,NCWW尽可能要避免。
下一步就是研究造成NCWW的机械接触类型都有哪些,以及如何量化这些类型。由于同一根金刚石线上可能会同时出现CWW和NCWW,所以这一问题解决起来比较困难。
论文的其他部分主要讨论在缠线和卸线的过程中引线卷轴上发生的金刚石线本身的机械接触。为研究这种接触是否影响切削过程,实验对晶片厚度做了分析,如图三所示。
利用传统的多线锯和Hennecke晶片监测系统用Y型金刚石线对125mm(6’’)的单晶碳化硅晶片进行切割;沿着25mm宽的条带平均分布测厚点。在1022块测试晶片中,有3块晶片厚度超过180μm,将其剔除在实验分析之外。
第2、3、4个25mm条带的平均值分别用向下的三角形、方形和向上的三角形表示,如图3所示。
对比图三中曲线间的不同可以看出:切割过程中(从向下的三角标识到向上的三角标识)晶片平均厚度增大。这说明金刚石线的外径由于线磨损而变小。金刚石线的横截面SEM图可以看出,与金刚石线相互垂直的方向上有典型的刮痕,如图2b所示。
通过气割还可以测量到线外径的减少,气割是线锯上材料负载为零的晶片切割加工。实验证明:通过对金刚石线操作管理系统的精微调整,可以降低线外径的磨损。总之,在每100周期的缠线和卸线循环中有最小为0.4μm的 外径减小量可以观测到。
镜片加工过程中线磨损的降低
从以上线磨损机制可以看出,对晶片加工设备的优化可以实现成本节省。事实上,传统晶片加工设备的金刚石线操作系统都是为自由磨粒锯切(LAS)技术而研发的;该技术中金刚石线自身的接触是无害无损的,因为线本身并不包含任何切割磨粒(如金刚石),也就不会磨损相互接触的其他金刚石线,进而不会影响切割性能。而固结磨粒锯(FAS)切技术中金刚石线自身的接触可以引起额外的磨损。因此,从LAS到FAS技术的转变就需要对金刚石线操作系统进行设备上的优化处理。
Meyer Burger研发了一种金刚石线操作管理系统的多线锯设备原型,能够在金刚石线缠线和卸线中最大化的减小线接触并多次重复使用,如图4、5所示。
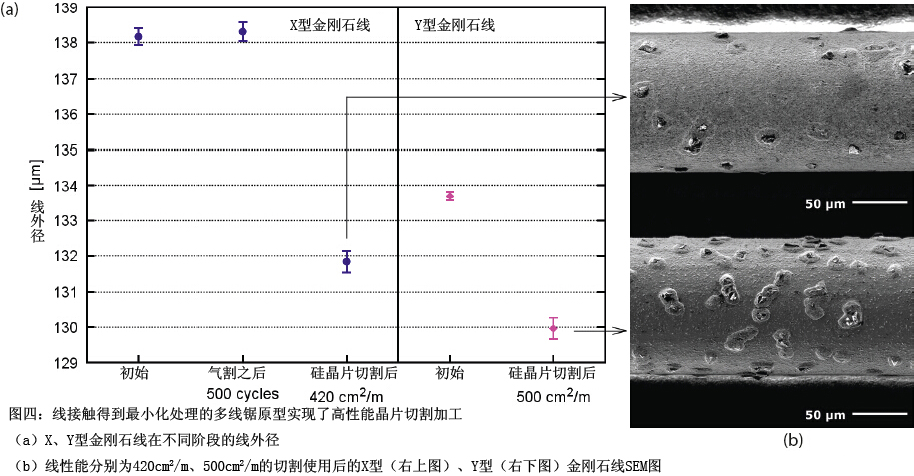
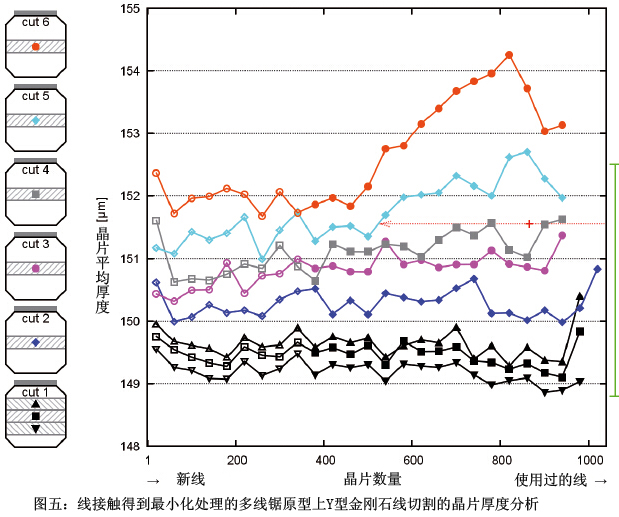
采用X型金刚石线对硅晶片进行切割加工,线性能为420cm2/m;另选线性能为500cm2/m的Y型金刚石线进行切割加工。观察发现,两种类型的金刚石线在缠线和卸线过程中都没有机械磨损带来的垂直刮痕。还可以观察到有效金刚石磨粒,如图4b所示。对比两种类型的金刚石线外直径发现,线磨损是线性能的一个函数,如图4a所示。
以上实验结果说明线接触经过最小化处理的晶片加工设备可以实现高性能的金刚石线切割加工。如图四所说明,成本节省取决于金刚石线的类型。
结论:
晶片制备工艺正经历有自由磨粒锯切技术向固结磨粒锯切技术的转变,其中金刚石线是最主要的消耗因素。本论文对缠线和卸线过程中线接触对金刚石线的磨损情况进行了研究分析;通过对现有线操作管理系统的精微调整,NCWW可以得到一定程度的减小。而要想进一步减少线磨损,就需要对金刚石线管理系统进行创新改造。(编译:中国超硬材料网)