车削工艺:
车削是对旋转柱形工件的外径进行金属磨除的工艺处理技术,按照规定尺寸对工件直径进行缩径并获得良好的表面光洁度。作为一种外表面加工处理,车削包括以下基本构造:旋转的工件;单刃切削刀具;切削刀具与工件轴向平行并间隔一定距离。锥面车削与之基本类似,不同点在于切削路径与工件轴有一定角度;而轮廓车削则通过改变切削刀具和工件轴间的距离来获取所需的工件形状。单刃切削刀具即便规格固定,也可以使用多工具装置来进行车削,每个工具都能够独立充当单刃刀具。
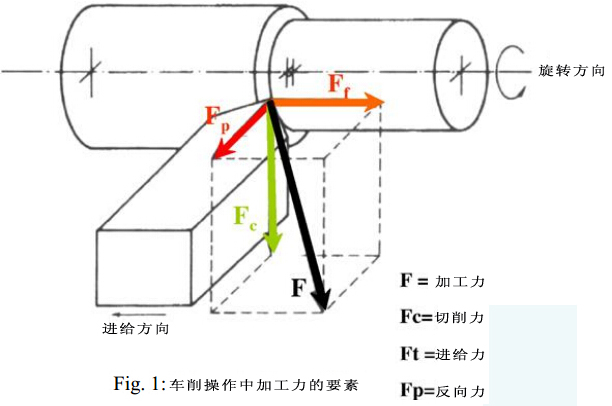
速度、进给和切削深度是车削工艺的三个基本参数。
切削速度:切削速度是主运动上切削行进的速率,工件圆周的切削刃经过时留下的长度,单位为米每分钟(m/min);当工件旋转时;每一个工件上的不同直径都需要不同的切削速度来完成。
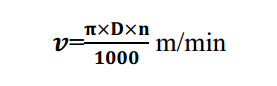
其中v为切削速度,D为工件原始直径,N为转数RPM。
切削速度不能随机选择。如果速度过低,加工时间就过长;如果速度过高,切削刃就会快速磨损从而失去原有的硬度。为求得准确的切削速度,需要考虑一下因素:
工件材料、车削工具材料、冷却、机床设计、切削口横截面
进给:工具沿着切削路径移动的速率。工具进给影响着加工速度和表面粗糙度。进给速度高时,加工速度就快;进给速度低时,表面光洁度就好。进给有手动进给和自动进给两种。
在动力进给车床中,进给速度直接与转数有关,单位为毫米每转(mm/rev)。
Fm=f.N mm/min
其中,Fm为每分钟进给毫米数,f为每转进给毫米数,N为转数RPM。
进给速度增大则会缩短切削时间,但也加快工具寿命的耗损。进给主要受尺寸、形状、强度、夹持零件所用方法、机床刚度和切削深度的影响。
切削深度:切削深度可以理解为工件表面被磨除掉的层厚度:

其中D为工件原始直径,d为切削后的直径
其他参数为常量,切削深度和切削速度的变化成反比;切削深度与进给速度比为10:1。
综述:喷射成形机压磨板
(1)《AISI D2 冷锻模具钢硬车削工艺机械加工性能研究》
Paulo davim, V.N. Gaitonde and S.R. Karnik, Int. Journal of Refractory Metals & Hard Materials 27 (2009) 754–763
本文利用不同的CC650、CC650WG和GC6050WH陶瓷刀具,设定切削深度直线性增长的加工条件,对高含量铬AISI D2冷锻模具钢进行硬车削加工,研究了切削力(Fm)、功率(P)、固定切削力(Ks)、表面粗糙度(Ra)和工具磨损(VC)等机械加工参数。实验采用基于数学模型的反应曲面分类研究法(RSM)分析了切削深度(0.2, 0.4 and 0.6 mm) 和加工时间(5, 10 and 15 min)对机械加工性能的影响,其中常量为80m/min,0.10mm/rev。
根据实验结果和参数分析对模型可适性进行方差分析(ANOVA),实验采用析因设计。研究结果发现:CC650WG刀具在表面粗糙度和工具磨损方面性能较好;而CC650刀具则降低了切削力、功率和固定切削力。
(2)《高强度铝合金加工用纳米晶金刚石镀附工具》
J.Hu, Y.K. Chou and R.G.Thompson, International Journal of Refractory Metals & Hard Materials 26 (2008) 135 –144
本文利用微波等离子体辅助化学气相沉积法在普通硬质合金工具表面沉积出纳米晶金刚石(NCD)涂层,研究了NCD工具加工高含量Si的铝合金工艺处理技术;通过改变速度(3 and 10 m/s)和进给(0.2 and 0.8 mm/rev)以及常量切削深度(1mm),利用MCD、PCD和NCD工具进行实验。
此外,实验还将CVD金刚石涂层和PCD工具跟NCD工具性能进行了对比;并建立了FE模型以此研究不同切削加工条件下和沉积金刚石涂层后的应力改性。
(3)《AISI 4340硬化钢车削工艺处理中CBN-TiN涂附硬质合金刀具和PCBN刀具的工具磨损、加工性能研究》
Abhijit S. More, Wenping jiang, W.D. Brown and P.Malshe, Journal of Materials Processing Technology 180 (2006) 253–262
本文采用析因设计,通过改变切削速度(100, 125 and 150 m/min)和进给速度(0.10, 0.15 and 0.20 mm/rev)以及固定切削深度0.25 mm,利用CBN-TiN涂附硬质合金刀具和PCBN刀具对AISI 4340硬化钢进行车削工艺处理。实验采用ANOVA法对以上加工参数对工具寿命、表面粗糙度和切削力的影响进行分析。加工参数设置为V = 125 m/min,F = 0.15 mm/rev,DoC = 0.25 mm,将CBN-TiN涂附硬质合金刀具和PCBN刀具进行了工具寿命、表面粗糙度和切削力的对比。结果发现:CBN-TiN涂附硬质合金刀具的使用寿命大致为每个切削刃18-20分钟,PCBN刀具寿命为32分钟。CBN-TiN涂附硬质合金刀具加工后的表面粗糙度在1.3微米以下;PCBN刀具加工后的表面粗糙度为常量值。两种刀具的切削力稍微不同。在降低加工成本方面,CBN-TiN涂附硬质合金刀具更有优势,因此更适合硬车削加工。
(4)《氮化硅刀具对灰口铁进行车削工艺处理中的切削力研究》
J.V.C. Souza, M.C.A. Nano, M.V. Ribeiro, J.P.B. Machado and O.M.M. Silva, Materials and Design 30 (2009) 2715 –2720
本文利用氮化硅(Si3N4)陶瓷刀具对灰口铁进行车削处理并研究其切削力。实验设置了不同的切削速度(180, 240, 300, 360 and 420 m/min)和进给速度(0.12, 0.23, 0.33, 0.40 and 0.50 mm/rev),切削深度为常量,1.0mm。切削力、工具寿命、温度和表面粗糙度等参数进行了研究分析。
研究结果表明当切削速度达到300m/min时切削力降低;工具磨损较少,这说明Si3N4适合加工灰口铁;同样速度下平均加工温度降低,进给速度增大。
(5)《AISI 52100钢的硬车削处理工艺中刀刃几何形状对工件亚表面变形和全厚度残余应力的影响》
Jeffrey Thiele and Shreyas Melkote, Journal of Manufacturing Processes Vol. 2/No. 4 2000
本文利用CBN对AISI52100钢进行硬车削,对切削刃制造和工件硬度对表面抛光和切削力的影响进行了研究。结果显示刃磨对表面粗糙度的影响随工件硬度增大而降低。同时,切削刃形状对轴向和径向切削力有着显著影响。
(6)《英高镍718高速加工工艺中切削参数对工件硬化和使用寿命的影响》
Dinesh G. Thakur and B. Ramamoorthy, Int J Adv Manuf Technol DOI 10.1007/s00170-011-3529-6
本文利用低温处理硬质合金工具对英高镍718进行加工处理,并求得了切削力,工具使用寿命、刀具外侧磨损和残余应力等。实验采用不同切削速度(40 and 65 m/min)、进给速度(0.08 and 0.2 mm/rev)和切削深度(0.5 and 1 mm)。结果显示低温处理过的硬质合金刀具的切削力要比未处理过的刀具切削力低10%-15%左右。
对工具使用寿命的分析研究表明:切削速度、进给速度和工具类型是影响工具寿命的三个主要因素;低温后处理技术也能改善硬质合金刀具的使用寿命。
通过选择适当的切削参数可以将工件硬化最小化;经低温处理的硬质合金刀具侧面磨损要比未经处理过的刀具磨损更加规则。低温处理的刀具残余应力比未经处理的刀具残余应力低7%。
结论:
根据上述研究文献可以看出,研究者利用不同切削刀具对不同材料如英高镍718、AISI 1040钢、AISI 52100钢、C45钢、灰口铁、富含硅的铝合金和AISI4340钢进行加工处理;通过速度、进给和切削深度等加工参数求得了切削力、表面粗糙度、断面形态和工具磨损等。本文旨在优化英高镍625硬切削工艺中的切削力和温度参数。(编译自中国超硬材料网)