本论文利用CBN工具对AISI 52100轴承钢进行精车加工,采用田口L9正交阵列和变量分析法(ANOVA)来研究切削参数(切削速度、进给和切割深度)对性能特征(切削力,表面粗糙度)的影响。结果表明进给速率和切削速度对表面粗糙度影响最为显著;而影响切削力的主要因素是切割深度,其次是进给。利用多次线性回归分析法对实验数据进行深入分析并预测切削力和表面粗糙度的最佳范围;并将切削参数和性能特征相关联。最后,在最佳切削条件(v=200m/min,f=0.08mm/rev,d=0.2mm)下分别用光学显微镜和扫描电子显微镜(SEM)对工具磨损面和工件加工面进行观察。
1.引言
对大于46HRC的钢件进行硬车削加工在齿轮、凸轮、轴承、模具等制造工艺中应用十分广泛。为应对工件较高的机械负荷和热负荷,以及切削材料优越的性能,CBN、PCBN和聚晶金刚石工具应运而生。与传统磨削工艺相比,硬车削工艺能够极大降低制造成本、缩短加工时间、工件表面整体质量更优良、减少不利于环境保护的冷却液的使用等。
加工表面特征对零部件的疲劳强度、抗腐蚀性、摩擦性能等使用性能有着重要影响。加工后的表面光洁度和整体性决定着工件的表面质量。表面粗糙度越大,表面光洁度就越差,零部件寿命就越短。因此,对加工表面进行控制是十分重要的,也是可行的;通过对切削力的调整即可实现。对切削力进行研究分析在硬车削工艺是也是十分重要的,切削力和切削性能密切相关,如表面精准度、工具磨损、切削温度和强制振动等。在车削工艺中有众多因素影响着切削性能,如工件变量、工具变量和切削参数等。工具变量包括工具材料、切削刃几何形状(后角、切削刃倾角、刀尖半径、前角)和工具振动等。工件变量包括材料、机械性能、物理化学性能等。切削参数包括切削速度、进给速率和切割深度。
本论文利用CBN工具对AISI 52100轴承钢进行精车加工,研究切削参数(切削速度、进给和切割深度)对性能特征(切削力,表面粗糙度)的影响。利用多次线性回归分析法对实验数据进行深入分析并预测切削力和表面粗糙度的最佳范围;并将切削参数和性能特征相关联。
本实验中,切削速度(v)、进给(f)和切割深度(d)为切削参数。表一为确认参数及其准级;表二为田口正交阵列。
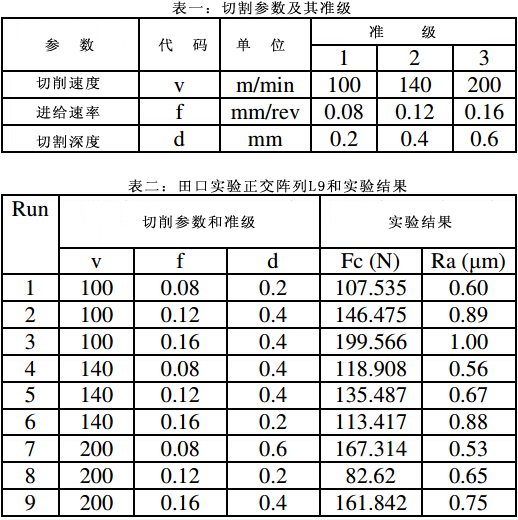
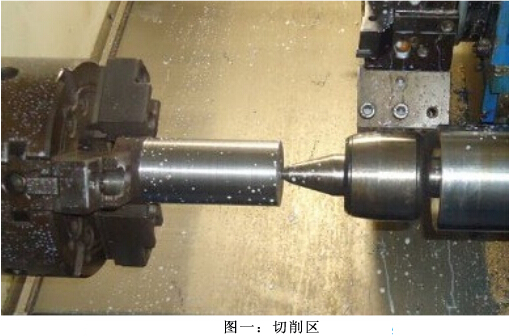
3.结果和讨论
3.1 切削力和表面粗糙度分析
利用变量分析法(ANOVA)对表二获得的实验结果进行分析。确认对性能特征(表面粗糙度、切削力)影响显著的因素,如表3所示。显著性水准α=0.1,可信度为90 %的分析进行操作。表格最后一栏为影响占比。
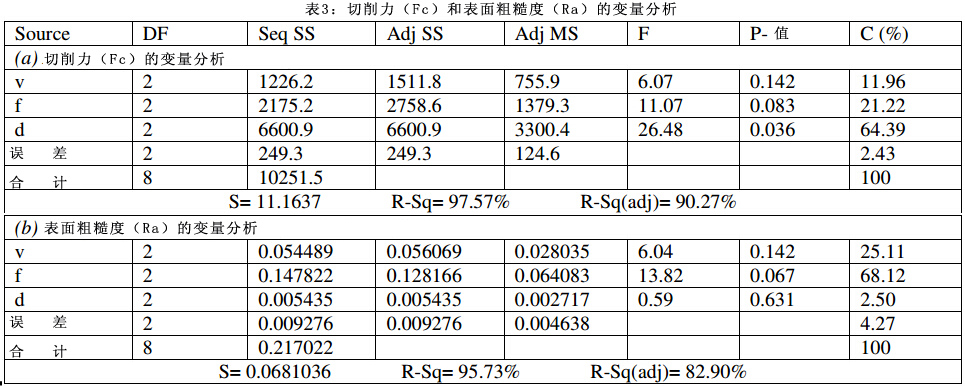
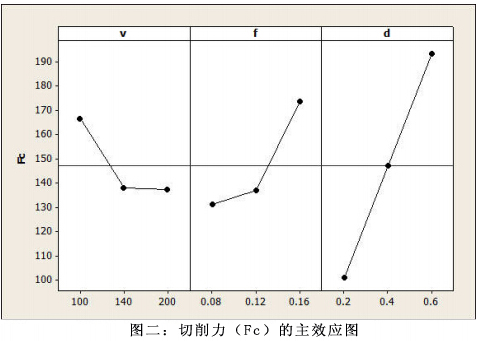
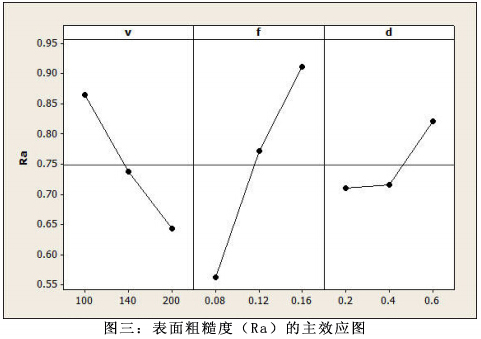
3.2 最佳设计预测

如表4所示,当切削力Fc的两个最显著的因素分别为:


其中,
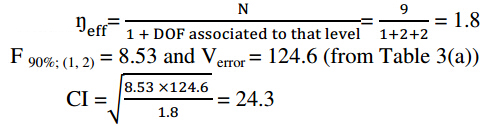
最后,Fc的90 %置信区间为:

如表4所示,当表面粗糙度Ra的最显著因素在f1准级时,表面粗糙度(Ra)的预测平均值计算如下:
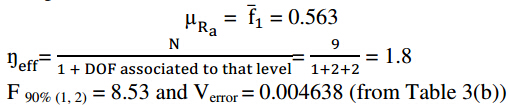
Ra 的90 %置信区间计算公式为:
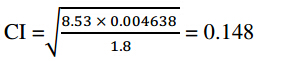
最后,Ra 的90 %置信区间为:

3.3 关联
用多元线性回归法对因子和性能特征进行关联;获得模型如下:

利用决定系数(R2值)对模型进行诊断检测。当R2接近统一时,响应模型和实际数据一致。
3.4验证试验
从图二、三可以看出,准级v3、f1和d1的结合出现了表面粗糙度最小值和切削力最小值。因此,为确认表面粗糙度和切削力,本研究将v3f1d1当作验证试验;实验结果和预测值接近,如表5所示。
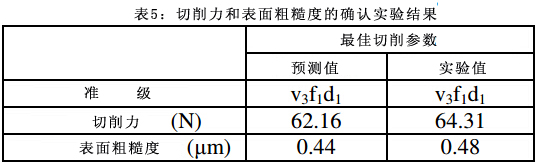
图四为CBN工具侧面磨损图。侧面上的磨损类型说明工具切削刃和侧面跟工件材料间的摩擦引起了磨损。侧表面出现许多沟槽;这些沟槽是由AISI 52100钢中的超硬碳颗粒引起的。图5为加工过程中表面质量的SEM图,切削速度为200m/min,进给速率0.08mm/rev,切割深度为0.2mm。图六为最佳切削参数下加工AISI 52100淬火钢的切削力。
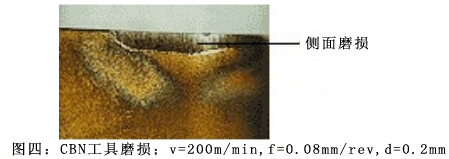
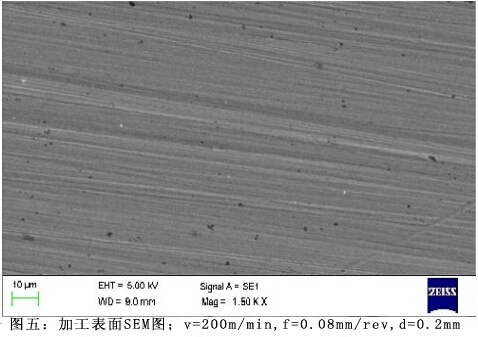
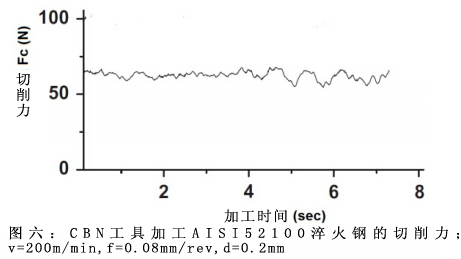
表面粗糙度受进给速率影响最大,占据68.12 %。表面粗糙度随进给速率增大而增大。切削速度为负效应(25.11 %),切割深度影响可以忽略不计(2.50 %)。
最佳切削力预测值和最佳表面粗糙度预测值的90 %置信区间分别为61.38 ≤µFC≤109.98 N,0.415≤µRa≤0.711 µm。
切削参数和性能间的关系可以用多元回归方程来表示,用来预测任意一个参数准级的性能预期值。(编译:中国超硬材料网)