1、线痕分类
线痕按照形状分为单一线痕、硬质点线痕和均匀线痕。单一线痕,有深有浅,若线痕较小还是可以接受为合格片。由于多晶硅铸锭的原料和工艺原因,多晶锭内部多少都会有SIC和SI3N4杂质,切割完成后,就会形成形状类似单一线痕。均匀线痕体现为整个或者部分硅片表面出现多条由深至浅状似划伤的线痕。对于多晶硅来说,三种情况都存在;对于单晶来说,线痕只有均匀线痕和单一线痕[1]。
2、单一线痕
造成单一线痕的原因有很多种因素,主要有:
(1)停机。切割机有时在某些警报下会自动停机,比如:砂浆流量过低,冷却液异常,电气柜温度过高;有时也需要人为停机,比如:雷电天气致供电电压不稳,排线机构异常,突发紧急状况。机器停止再重新启动后,由于导论心震,钢线不能完全按照原位置切割,就产生了线痕。
(2)断线。断线后的晶棒即使能够挽救回来,但是由于停机,硅片上也会产生线痕。产生断线的原因主要有:①张力问题。a/.收放线端排线不均匀,造成“一侧坑一侧包”的状况,钢线运动到两侧时张力急剧跳动,造成断线;张力臂由于长时间未清理,粘附砂浆过多,造成张力臂过重,调节灵敏度降低;b/.张力臂转轴部分被砂浆堵塞,造成摆动不畅,都可以导致断线;c/.钢线生产时产生线头穿错,也称为压线,极易造成断线;d/.张力检测设备故障或由于长时间使用,张力检测值形成偏差,从而形成断线;e/.钢线走线导轮磨损严重,造成钢线剧烈波动,张力不稳,导致断线。②钢线本身质量问题。a/.钢丝强度偏低;b/.钢丝存在表面缺陷,当受力时这些表面缺陷处成为应力薄弱部位,易于断裂。③切割工艺问题。a/.张力设定过大,钢线运行速度过高,砂浆粘度过低,砂浆流量过低,新线供给过少,造成带砂浆能力下降,钢线磨损量过大,形成断线;b/.工作台进给速度过快,造成钢线弯曲度过大,形成断线。
由此可见,控制断线问题首先要控制好张力,张力臂系统要定时清洗,保证其运行灵敏,导线轮要定期更换,张力检测装置要定期校正,校正完成后用手动张力计进行校对,保证其张力检测无偏差;其次要购买品质好的钢线,否则会大大增加断线率;最后要使用成熟的切割工艺,其中砂浆配置是一个关键环节。碳化硅微粉在包装、运输、存放过程中挤压结团,这就要求工人在配制沙浆倒料过程中要特别注意:倒料时应慢倒,控制在2.5~3min一袋,避免猛倒造成微粉沉底结块搅拌不均,造成与实际配比不一致,影响切割。碳化硅微粉具有较强吸水性,在空气中极容易受潮结团,应避免微粉裸露在空气中时间过长。砂浆在配制过程出现了许多的人为因素,很多参数因人为而改变。如果改为自动投料,减少人为因素效果会更好。最好把碳化硅微粉在80~90℃烘箱里,烘8h以上,来优化碳化硅微粉的各项指标。一般来说,手动调配的砂浆需要搅拌6h以上,全自动雾状投入磨粉的,只需搅拌1~2h即可使用。
(3)跳线。跳线的线痕一般集中在硅棒某一段,但也有全线网跳线的,造成硅棒各段都有线痕。导致线网跳线的原因主要有:a/.上次切割完的线网没有清理干净,或者硅片碎片、砂浆的杂质没有过滤完全,进入线槽引起跳线;b/.张力设定过小,造成钢线绷紧不够引起跳线;c/.导轮使用时间过长,造成钢线振动过大,引起跳线;d/.主辊线槽磨损严重,钢线在相邻线槽间移动,造成跳线。
由此可见,为了避免跳线,每次切割前要严格检查线网和主辊状况,保证其杂质都被清理干净;钢线张力要根据钢线直径和工作台进给速度合理设定;定期检查更换导轮,保证其导线槽磨损量在合适范围内。
(4)粘胶问题。硅棒与玻璃板粘接时,由于抹胶过多或者刮胶不彻底,导致钢线带胶切割,造成钢线携带砂浆能力下降,形成线痕。此类线痕一般在靠近粘胶面的倒角处。因此抹胶量要严格控制,可以用纸胶带粘于倒角处,待硅棒与料板压紧稳定后,再将胶带撕下,这样就可以防止胶水粘附在硅棒上。
(5)收线弓时产生线痕。在切入玻璃的时候,正在拉线弓,这个时候钢线在两种介质中切割,由于硬度和结构的不同(以金刚石硬度10为准,玻璃硬度为6,单晶硅硬度略逊于金刚石),导轮跳动过大,哪怕一瞬间,产生侧移,就会产生线痕。因为玻璃是非晶体,在600℃左右就会变软。钢线切割到玻璃的时候在玻璃表面会产生大量的热,软化,黏附钢线,砂浆就不易被带入,降低了切割能力,这时也容易产生线痕。
(6)进刀口钢线波动。由于刚开始切割,钢线处在不稳定状态,钢线的波动产生进刀口线痕,进线点质硬,比如多晶的切割一般会有此问题,加垫层(导向条,如石墨,玻璃等)可以使钢线容易切入,消除线摆,消除进刀口线痕。
3、硬质点线痕
单晶没有硬质点,多晶在铸锭过程中会形成硬质点,切割时会产生硬质点线痕,如图1所示。
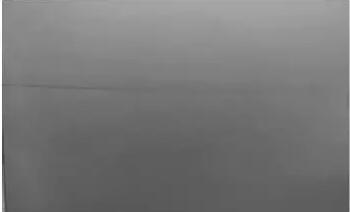
图1:硬质点线痕
减少多晶硬质点的解决方法:
(1)在装料后执行严格的开炉程序以排除氧和水分,因为他们可以和石墨反应生成CO溶于硅熔体,使得碳含量增加。
(2)将石英坩埚和石墨托隔开或选取适当的气流方式使CO不能到达熔硅表面,减少晶体生长过程中的碳污染。
(3)尽量缩短硅锭生长周期,以抑制SiC的长大和聚集,他们在较细小、未聚集的情况下不会对硅片切割造成危害。
(4)热场采用二氧化钼涂料进行覆盖。
4、均匀线痕
此类线痕的表现形式为硅片整片或部分区域的密集线痕(如图2)。
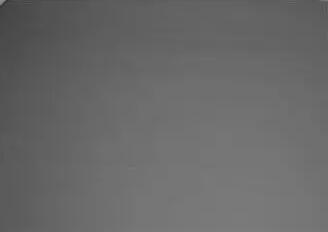
图2:均匀线痕
(1)沙浆黏度不够、钢线圆度不够、线速过高、钢线张力太大,导致钢线带砂浆能力降低。
(2)碳化硅微粉切割强度不够或者圆度系数过高,导致砂浆切割能力下降。
(3)工艺参数不合理,砂浆流量过低。
由此可见,为了避免此类线痕产生,切割前要仔细检查钢线质量、碳化硅微粉硬度和圆度,切割时使用成熟的切割工艺,确保钢线张力、线速、砂浆流量合理配置。此外,目前很多厂家为了节约成本使用回收砂浆,由于回收砂浆的碳化硅微粉硬度、圆度不稳定,导致重新配比后的砂浆中碳化硅微粉之间、微粉与悬浮液之间存在配合性问题[3]。这种使用回收砂造成的均匀线痕可以通过加大砂浆密度,降低工作台速度,减少使用回收砂的比例和加大砂浆更换量在一定程度上得到控制。
5、结论
综上所述,多线切割工艺非常复杂,硅片线痕产生的原因也是多种多样,为了减少线痕片的产生,必须严格保证切割线和碳化硅微粉的质量,砂浆的配置和搅拌要严格按照配置工艺进行,保证其黏度、密度、切割力符合要求;粘胶时注意胶水使用量,避免胶水在硅棒倒角处残留;切割前仔细检查线网和主辊,保证没有杂质附着;砂浆要充分过滤,滤净其杂质;检查张力系统和每个导线轮状态,不过度使用导轮;使用成熟的切割工艺,使钢线走线速度、工作台速度、砂浆流量、钢线张力合理配合。只有这样才能避免或减少线痕片的产生,切出质量合格的硅片。
参考文献:
[1]陈雪,汪钉崇.单多晶太阳能硅片线痕的起因和降低方法[C].第十届中国太阳能光伏会议论文集.杭州:浙江大学出版社,2008:218-222.
[2]徐旭光,周国安.多线切割晶体表面质量研究[J].电子工业专用设备.2008(166):20-22.
[3]李轩.太阳能电池板线切割常见线痕及浆料配置[EB/OL].Http://home.51.com/1464468707/diary/item/10039508.html,2008-11-25/2012-7-15.