抛光、珩磨和磨削等传统精整工艺不足以在航空航天、光学电子、医疗器械和核反应堆等技术领域的设备制备工艺中实现较高要求的表面精整水平。MAF工艺则可以在管状工件的内外表面以及平面工件上实现较高的表面质量;利用磁场中形成的磁性磨粒,MAF可以实现较高的工件表面和边缘精加工。少量的磁性磨粒充当切削工具,当对工件施以相对运动时这些磨粒在工件表面受到压缩并将待加工材料以切屑形式磨除掉。
Shinmura 等人在高温高压条件下将平均直径5μm的氧化铝和铁粉混合,在真空烧结炉中1.5小时,将其制备成150μm粒度大小的磁性磨粒,对SS41材质的工件进行破碎和修整加工,并研究MAF工艺的基本原理。实验结果表明工件表面精整质量得到了约40%的改善。 Aizawa等人利用磁性辅助磨料研磨工艺对非铁磁管状工件进行内表面精整加工。实验所用工件为不锈钢卫浴管,磁性磨料为氧化铝和铁粉混合制备而成;表面精整改善约48%。实验还对MAF工艺中润滑剂的使用量进行了研究,发现润滑剂最佳用量可以改善磨料在工件表面的接触进而实现较好的表面精整且精度较高。Khairy等人研究了MAF工艺在精整加工银器钢棒的粗糙表面和锋利边缘时的有效性和稳定性。实验将氧化铝和铁粉混合,在1400℃下置于盛放有惰性介质的炉中进行压制,时间1小时;然后将其破碎成小颗粒并进行粒度筛选。实验结果表明MAF工艺能够改善表明精整约52%。表面光滑度、纹理结构和表面层等都要比珩磨、抛光等利用固结在铁水泥粗颗粒上的精细磨料产生的表面精整质量要好。
Kaur A.等人利用氧化铝做磨料成分、铁粉做铁磁成分制备出普通磁性粘结磨料,然后进行MAF工艺试验。表面精整改善程度最大为36%。
以上文献可知,MAF工艺参数如磁性磨粒量、工件旋转速度、磨粒粒度、加工时间、工件间隙和磁通量密度会影响表面精整质量和材料去除率。
2、磁性磨料的制备
试验将300目铁粉(体积比80%)和300目氧化铝磨料(体积比20%)进行手动混合,置于1100℃烧结炉中,烧结完毕将其破碎成小颗粒并进行粒度筛分,如图1所示。所用磨料粒度为120、180和220(106μm、75μm和53μm)。

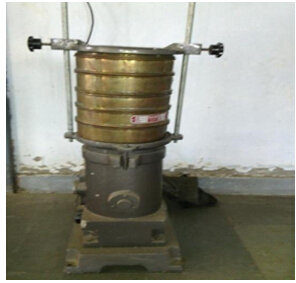
图2为内表面MAF工艺用实验装置。磁性磨料堆放入管状工件内,两个永久磁铁产生磁场。根据工件外直径调整改变工件-磁铁的工作间隙。
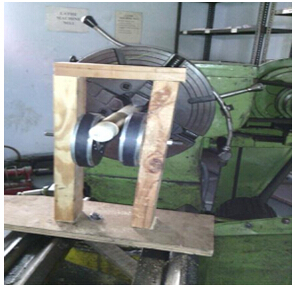

实验对工艺中的有效参数如磁性磨料量、工件旋转速度、磨粒粒度、加工时间和工作间隙进行改变并研究它们对表面粗糙度的影响。
图3为磁性磨料量对平均表面粗糙度的平均值的影响。据图可知,表面粗糙度随磨料量增加而降低,说明磨料量增加可以改善表面精整质量。表面粗糙度随磨料粒度增大而降低。还可以看出表面粗糙度的降低随着中间线的出现划分出两个基准,基准1和基准2;随着工件-磁极的间隙增大,表面粗糙度数据从基准1降低为基准2进而增大转向基准3。表面粗糙度随工件旋转速度的增大呈定量下降。随着加工时间的延长,表面粗糙度由基准1向基准2定量下降,基准2到基准3的下降变化影响基本可以忽略。