摘要 多晶硅产业背景光伏发电的地位稳步提高2012年全球新增光伏装机容量32吉瓦,全球累计安装量达到100吉瓦,德国安装总量32吉瓦,居首位。2011年上半年,德国的可再生能源发电总量实...
多晶硅产业背景光伏发电的地位稳步提高 2012年全球新增光伏装机容量32吉瓦,全球累计安装量达到100吉瓦,德国安装总量32吉瓦,居首位。2011年上半年,德国的可再生能源发电总量实现历史突破,达到其电力需求的28%,光伏发电首次超越水电,占总电力需求的3.5%。伴随日本福岛核电事故的发生和我国今春大范围雾霾加剧,人们寻找清洁高效的新能源的步伐日益加快。此间,太阳能光伏发电成为最受关注的重点之一。2013年,全球安装有望达到35吉瓦。光伏装机容量在全球范围的持续增长,标志着光伏发电的地位将稳步提高。
多晶硅产业集中度提高 多晶硅是信息产业和太阳能光伏发电产业的基础原材料,多国都已将其列为战略性材料,实施政策鼓励与财政支持,而我国由于多晶硅产业化生产技术的缺乏,国内需求长期依赖进口。直到2005年,洛阳中硅高科技有限公司依托中国恩菲工程技术有限公司,建成我国第一条产业化示范线,彻底打破了国外多年技术封锁和市场垄断。
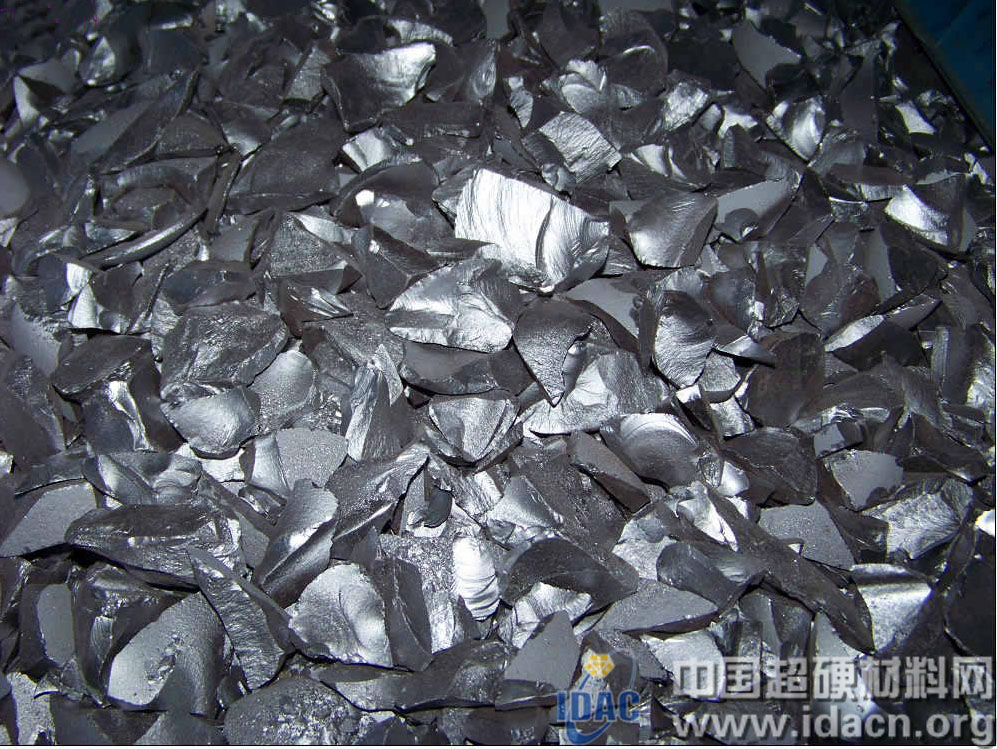
光伏发电商业化应用对多晶硅生产成本的持续降低将形成持久性压力,在当前阶段、在多晶硅技术还没有取得革命性突破时,多晶硅企业能否生存下来的简单而明确的判断标准之一,便是生产成本与国际一流企业的差距。
在国外,多晶硅属于产业集中度非常高的行业。30年来,国际上具一定规模的多晶硅生产企业仅7家,旗下共10家工厂,集中在美日德。而在国内,多晶硅行业曾经出现的“天价行情”,使在资本逐利性驱动下的许多企业,纷纷铤而走险涉足多晶硅行业。但是由于缺乏核心技术和管理提升能力,难以形成持续降本能力。2010年,部分企业曾经间歇式生产;2011年以来,大部分企业已处停产状态。
严酷的市场洗礼已经淘汰、也必将淘汰大部分无规模效应的企业和有规模效应企业的部分落后产能,必将使产业集中度大幅度提高。有效的多晶硅产能,是能够真正形成持续的市场供应能力、并且生产成本具国际竞争力的产量,目前我国该部分产能不足10万吨/年,能够提供有效产能的企业数量约3—8家。
多晶硅产业安全度降低 多年来,我国光伏用多晶硅50%以上依赖进口,电子级多晶硅100%依赖进口。目前,我国多晶硅行业深陷经济危机、贸易战、货币战的三重重压,再加上国外媒体的误导,中国多晶硅一直在“高能耗、高排放”的困扰下艰难前行:各项优惠政策取消、电价优惠难以获得、融资渠道阻塞。而美欧多晶硅企业,在政府政策扶持、财政补贴和高价长单捆绑中国下游客户的背景下,大幅低价倾销中国市场,给刚刚兴起的中国多晶硅产业形成致命打击。
目前,我国80%多晶硅企业停产超过一年,2012年中国产能利用率仅三分之一;2013年一季度全国产量不足1万吨,产能利用率不足25%。随光伏行业钢性需求的增加,我国多晶硅产品的供应能力并未显著增强,内忧外患导致我国多晶硅行业的产业安全度降低。
2009年以来,我国多晶硅产品的对外依存度一直维持在50%左右且居高不下。依靠大量多晶硅进口支撑了中国光伏和信息产业的发展。
2012年,中国多晶硅产量占全世界四分之一。国内多晶硅企业全线停产,将导致全球多晶硅供需失衡,中国光伏企业也必然面对原料供应价格上涨,生产成本大幅提高的局面。可以说,正是有了多晶硅这块“挡箭牌”,既平抑了国外多晶硅产品的进口价格,又为中国光伏行业提供了喘息和发展的“保护伞”。所以,中国多晶硅与中国光伏行业荣辱与共,产业链任何不同环节之间发生的兄弟阋墙行为,都不利于中国光伏产业的发展。
多晶硅能耗解析
光伏发电能量回收期 和火电厂用煤发电不同,光伏发电利用半导体界面的光生伏特效应,将太阳能直接转变为电能。虽然多晶硅在生产过程中需要耗能,但作为太阳能光伏发电的核心材料,却能产生更多能源,所以以能量回报率或能源再生比来看,多晶硅和一般工业品有很大差异。
据计算,光伏发电从硅石冶炼开始,经过工业硅、多晶硅、铸锭(拉晶)切片、电池片制造、光伏组件生产到光伏系统安装完毕,全产业链的总能耗为1.60千瓦时/瓦。
各环节具体用电量为:(1)“硅砂——冶金硅”的能耗:13千瓦时/千克;(2)“冶金硅——多晶硅”的能耗:120千瓦时/千克,蒸汽消耗50千克/千克—硅;每生产1千克高纯多晶硅消耗1.35千克冶金硅;(3)“多晶硅——多晶硅片”的能耗30千瓦时/千克;1千克硅锭/硅棒需要1.1千克高纯多晶硅,1千克硅棒或硅锭可以切46片156×156毫米硅片,每片平均制造4.2瓦太阳电池;(4)“多晶硅片——多晶硅光伏电池”的能耗 0.2千瓦时/瓦,制造每瓦太阳电池需要的高纯多晶硅5.7克/瓦;(5)“光伏电池——光伏组件”的能耗0.15千瓦时/瓦,(6)“光伏组件——光伏系统”的能耗 0.25千瓦时/瓦。
以上系数计算,全部能量消耗结果为:1.55千瓦时/瓦,太阳电池组件产率=97%(即封装成品率),全部能量消耗:1.55 /0.97 = 1.60千瓦时/瓦。
依据国家发改委2013年2月《关于完善光伏发电价格政策通知》征求意见稿的地区分类,计算有代表意义地区的发电量和能量回收期:
二类地区:1瓦电池安装在西北部地区,年均有效发电小时数1400-2100小时,按年当量小时数1500小时计算,年均发电量1.5千瓦时;按照寿命25年计算,总发电量37.5千瓦时,能源再生比37.5/1.6=23.4,即耗1度电可再生23.4度电;能量回收期为1.07年(=耗电/年产电)。
经计算,各类不同地区光伏发电的能量回收期,晶硅太阳能电池的能量回收期介于1.07—1.6年之间,平均能量回收期为1.3年。可以预见,随行业技术进步,各个环节能耗仍将下降,光伏发电能量回收期将缩短至1年以内。
目前,国内生产的晶硅太阳能组件的使用寿命为25年,在生产太阳能组件能耗回收后,几乎不用再消耗能源即可发电,整个寿命期内没有任何污染物排放。事实上,即使25年之后,太阳能组件的发电效率大约相当于25年之前的80%,仍可使用很长一段时间,已有晶硅太阳能使用超过30年的案例。
标煤消耗比较 据《中国电力减排研究》发布数据:2012年全国6000千万以上火电机组平均供电标准煤耗平均为324克标准煤/千瓦时。光伏发电从硅石到系统的总能耗为1.60千瓦时/瓦,全部能耗折标煤为518.4克标准煤/Wp。晶硅太阳能电池寿命25年,基本免维护,寿命期内(按年有效发电时间1500小时计算)平均发电量=37.5千瓦时,折标煤为13.82克标准煤/千瓦时,仅为煤电消耗的4%,尽管发电密度低,但确属优质能源。
全行业能量平衡分析 据统计,按2012年国内产多晶硅6.4万吨、每千克多晶硅耗电120千瓦时计算,多晶硅生产总电耗为76.8亿千瓦时,仅占全国2012年总用电量49591亿千瓦时的0.1548%,微不足道,“高能耗”名不副实。
6.4万吨多晶硅可制造10.83吉瓦太阳能电池,二类地区每年发电量162.5亿千瓦小时,一年发电量的48%足以偿还多晶硅电能消耗。随着多晶硅技术提升导致能耗下降(由120千瓦时/千克降低到100千瓦时/千克以下)、光伏电池效率继续提高(17.5—22%)、基片继续减薄等技术发展,晶体硅光伏发电系统的能量再生比有可能更高。按测算结果,完全可以利用光伏发电来生产多晶硅等光伏产品,实现良性的、可永续发展的太阳能产业。
多晶硅清洁生产路线图
多晶硅工艺提高后,完全能够实现清洁生产。产业发展初期,生产规模小,副产物处理技术不完善,部分副产四氯化硅通过水解及贮存等简单的处理方式,给行业带来负面影响。
伴随产业规模扩大,简单的副产物处理方式已不能适应大规模生产需要,为降低生产成本,实现安全环保生产,以中硅高科为代表的企业深入研究四氯化硅氢化技术,将其转化为原料三氯氢硅,实现了多晶硅生产系统的闭路循环,以此降低多晶硅生产成本。
舆论误导 2007年,中国首次成为世界第一光伏产品生产大国,当年多晶硅产量1130吨,突破千吨大关,中硅高科当年产量506吨,约占全国50%,列首位,成为业内外关注焦点。
2007年8月,国内某期刊发表《太阳能产业真相》,2008年3月9日,美国某知名媒体援引该文的主要观点,发表题为《中国太阳能生产厂家将工业垃圾倾倒在厂后》的报道,大肆渲染中硅高科300吨生产线调试过程中的一次偶发阀门泄漏事件,引发不了解多晶硅行业内情的相关人士的误解,“声讨多晶硅”之声不绝于耳。此报道到目前仍成为证明多晶硅污染的“依据”之一。
针对此报道,国家环保部曾多次、随机地到现场调查,当地环保部门也进行了长达2周的现场突击检测,最终得出“中硅高科‘三废’全部达标排放”的重要结论。2009年,中硅高科获得国家“环境保护突出贡献奖”,2010年获“全国环保优秀品牌企业”。
严格的核查及客观的结论,已经为中国多晶硅企业正名,正是在此基础上,2012年“多晶硅节能环保新技术、装备及产业化”荣获国家科技进步二等奖,这一目前行业最高奖项,成为行业发展的标志性事件。
多晶硅副产物的处理措施 有关多晶硅污染的报道,主要集中在四氯化硅的处理上。美国媒体发出“四氯化硅倒在地里会寸草不生”的言论。可实际上,四氯化硅既是多晶硅生产的主要副产物,也是多晶硅生产原料的主要来源之一。近几年,随着四氯化硅冷氢化等技术研发与推广,实现了将多晶硅生产过程中产生的95%的副产物四氯化硅氢化转化为三氯氢硅原料,剩余约5%含杂质四氯化硅经提纯后用于生产气相白炭黑或其他有机硅产品,真正做到物料闭式循环利用,既有效解决了副产物处理难题,也降低了生产成本,消除了四氯化硅的污染隐患。
多晶硅“三废”处理措施 事实上,多晶硅生产的“三废”成分简单,处理容易。多晶硅还原尾气主要含有氢气、氯化氢、三氯氢硅、四氯化硅等成分;废水为废气淋洗水、纯水制备排水等, 含盐酸,呈酸性;废渣为硅粉、二氧化硅、石灰石渣等,无害、不溶,属一般固体废物。
通过用水或碱性水对废气进行淋洗,利用氯硅烷极易水解和酸碱中和的原理,将废气中的主要成分水解成二氧化硅和盐酸,盐酸与碱反应形成中性水,进一步处理后达标排放;二氧化硅通过压滤固化后运至政府指定垃圾场或填坑铺路。
氢化技术取得突破是形成多晶硅生产过程物料封闭循环的基础,现在国内大部分千吨级规模的工厂都有“尾气干法回收”系统,环境影响评价和监测系统完善,不存在“高排放”。
多晶硅生产工艺比较分析
目前,国际流行且可量产的多晶硅生产工艺主要分为两类,即改良西门子法和硅烷法,改良西门子法因其应用基础广泛,在本轮多晶硅产能扩张中占据了主要地位。近年来,全行业遇到困境之时,国内部分企业纷纷将目光转向更加陌生的硅烷法多晶硅生产工艺,西门子法或硅烷法究竟孰优孰劣?
历史起源 1955年,德国西门子开发出以氢气还原高纯度三氯氢硅,在加热到1100℃左右的硅芯上沉积多晶硅的生产工艺;1957年,这种多晶硅生产工艺开始应用于工业化生产,被称为“西门子法”。此后,各企业根据自己的特点,对西门子法进行改良,形成了各自的改良西门子工艺。
硅烷法制造多晶硅也是一种化学方法,核心工艺是利用高纯度硅烷在反应器中热分解为高纯度硅,可生产棒状和粒状两种形态产品。目前,美国MEMC公司和挪威REC公司采用硅烷法生产多晶硅。
历史表现 近年来多晶硅不同方法生产的产量与份额见表4:由表4可看出,硅烷法多晶硅产量份额在11%左右。自2007年开始,中国共4家企业开展硅烷法多晶硅技术引进、研发和产业化,投资最多的是23亿元,年产3000吨多晶硅,至今没有产品上市。
国外多晶硅产业政策
美国多晶硅政策 多年来,美国美国的多晶硅产量一直位居世界前列,政府将多晶硅产业纳入清洁能源和制造业回归范畴,通过投资补贴、财税支持、基础措施建设补贴、电价补贴、土地优惠等多项政策,支持并补贴多晶硅企业,仅2010年美国政府提供给多晶硅企业的“投资补贴”一项政策支持就高达4.62亿美元;Hemlock公司2008—2011年获得美国政府补贴总金额高达7.46亿美元,约占Hemlock公司2008—2011年总收入的5%。
德国多晶硅政策 德国政府为多晶硅企业提供各种形式的资金支持,截至2011年底,德国政府机构提供的各项投资补贴为瓦克公司节省了4.47亿欧元的成本。
在新能源产业兴起,从而导致多晶硅需求剧增的情况下,国外多晶硅企业在2005—2007年罕见扩产的举动。2008年以后,国外多晶硅企业的产能扩张与取得政府巨额补贴几乎同步进行,可以说正是由于政府的扶持,才导致了国外多晶硅企业的竞争优势,在一定程度上,该种优势形成了对我国多晶硅企业的现实压力。
多晶硅行业的政策建言
根据国家能源局规划,到2050年,中国总用电量113000亿千瓦时,可再生能源比例达到62%,太阳能光伏所占比例为12.4%,光伏安装总量将达到1000GW。面对如此广阔的内需市场,从政策层面保护多晶硅行业的稳定和发展,有利于推进中国光伏行业的健康发展。
扶优扶强,支持先进多晶硅企业研发新产品 多晶硅政策要适应客观变化,鼓励优势企业节能技改,进一步提升竞争力。国家科技部在“十五”期间支持了24对棒节能还原炉研究,“十一五、十二五”支持了冷氢化、热氢化、节能高效提纯技术和副产物综合利用技术,这些技术对多晶硅行业起到巨大的推动作用,但与德国瓦克所拥有的5000多种多晶硅产业链技术和产品相比,中国多晶硅企业产品单一、抗风险能力差,需要国家进一步支持、加大科技投入,提升技术水平,提高质量、稳定质量,降低消耗,提高综合利用能力,实施产品多元发展(如有机硅、光纤四氯化硅、硅烷等),以确保产业安全。
开放光伏发电市场,实现光伏发电的直接交易试点 光伏发电属黄金电力,其发电季节和发电时段与用电高峰基本吻合。目前,我国光伏发电的成本已经具备一定的商业化应用基础,成本在1元/千瓦时左右,全国不同地区,高峰电价不同。
光伏发电在与高峰用电基本匹配的条件下,将有利于电网调峰,如果在这些地区开放光伏发电市场,允许一般工商企业与光伏发电的直接交易,将有效促进光伏发电应用。
营造公平的竞争环境 在当前全球经济低迷、贸易保护盛行时期,多晶硅及光伏已经成为全球关注的焦点,各国政府均伸出“有形之手”,采取多种措施对本土企业进行保护:美国多晶硅企业用电价格2—3美分/千瓦时,日本德山曹达、德国瓦克拥有自备电站,韩国多晶硅企业电价折合人民币0.41元/千瓦时。
而中国多晶硅企业基本使用全球同行最高电价,为避免中国多晶硅企业“饿死在开饭前”,并鉴于全行业总用量占全社会总用电量微小,应给予多晶硅企业直购电、自备电站等政策,为多晶硅企业参与国际竞争创造平等条件。
目前,中国光伏行业因“双反”而引人注目,多晶硅是光伏行业的基础。通过近十年的努力,多晶硅产学研用等各个方面均取得历史性突破,同时也带动了光伏行业的迅猛发展。在产业低谷时期,我们应以坚韧不拨的实干精神,克服暂时的困难,用更好的业绩迎接光伏的美好明天。