摘要 1963年12月6日,我国在两面砧装置上合成了第一颗人造金刚石,并在重复试验中多次得到,从而基本上完成了在实验室内得到人造金刚石的第一阶段试验工作。为了继续扩大成果,找出更合理的合...
1963年12月6日,我国在两面砧装置上合成了第一颗人造金刚石,并在重复试验中多次得到,从而基本上完成了在实验室内得到人造金刚石的第一阶段试验工作。为了继续扩大成果,找出更合理的合成工艺方案,过渡到工业生产上去,第一机械工业部一方面组织有关单位,编制了“人造金刚石中间试验计划任务书”,以(64)机密技字2168号文,报请国家科委审批。一方面立即作出明确安排:中间试验基地设在三磨所内,中间试验由三磨所总负责,北京通用机械研究所、济南铸造锻压机械研究所和上海材料研究所等单位参加。1964年春,一机部召开的计划工作会议上已经作了协调安排,然后以(64)二局铸字第906号文件,给济南铸造锻压机械研究所发出“关于下达六面加压专用液压机试验研究品试制计划的通知”,通知说:三磨所为了承担国家人造金刚石的重点科研项目,急需六面加压专用液压机(又称六面顶)一台,现决定将该产品的设计、试制计划正式下达你所,列为试验研究品项目。要求在1965年上半年完成试制,并争取提前。希接通知后即将各项工作安排落实。
时任济南铸造锻压机械研究所副总工程师的范宏才从北京香山回所后,立即向第四研究室布置了任务,由研究室主任闵学熊负责组织液压机组的王留德、于秀勤、杨大春和我成立了“121课题小组”。1964年4月,三磨所就派出于鸿昌、余征民二人来到济南,向课题组介绍人造金刚石的国内外发展情况,提出了人造金刚石工艺试验对设备的要求。余征民同志就留在济南,参加课题小组,自始至终,全程合作。
范总工程师结合工业化生产人造金刚石的目标,对第一台六面顶试验样机提出了下列技术要求:
1、满足人造金刚石工业性生产工艺的试验研究;
2、具有半自动循环工作规范,适合工业性生产人造金刚石;
3、单次循环时间30——45分钟;
4、压力腔内的最高压力达到7万——10万大气压;
5、压力腔内的最高温度达到1600——2000度;
6、保压时间30分钟;
7、顶锤的同步性必须保证压力腔的可靠密封;
8、顶锤寿命达到300次以上。
以上技术指标,意味着人造金刚石的工业性生产设备必须采用特殊的结构、材料和超高压液压传动。然而,我国当时的液压技术才起步不久,液压机行业的技术水平很低,还处于测绘和仿制阶段。行业标准中也只有最高压力为200kg/cm2的部分简单的液压机和液压元件标准。能够独立设计制造的,主要是一些简单的、中小型液压机。即便如此,还普遍存在漏油的问题。济南铸造锻压机械研究所当时还刚刚从“设计处”转型成立,试验与加工条件十分简陋。研究制造六面顶超高压液压机,面临一系列技术难题。而且,六十年代初的国际环境,我国正处于帝、修、反的技术经济封琐之中,没有任何技术资料可以借鉴,只能自力更生,通过设计分析、实验研究去解决。这样一个包含许多探索性难题的任务,要求在一年内完成,时间十分紧迫。
面对这项十分艰巨的任务,范总工程师组织了第四研究室“121”课题组,第五研究室电气、金属材料、理化检验等专业人员和试制车间、供应科等有关部门,通力合作。在保证工作质量的前提下,抢时间、赶进度。要求“121”课题组在六面顶液压机的方案设计、技术设计初步确定以后,提前提出铰链樑、工作缸等大件毛坯的协作图纸,由供应科落实协作。与此同时,提前进行超高压密封试验装置的设计与制造和超高压密封性能与寿命试验。通过单项试验,选取最佳方案,确定主机的结构,进一步完善施工设计。另一方面,提前进行大件加工工艺装置的设计、制造,以便保证大件加工的进度不拖后腿。这样,把多项工作有序结合,交叉进行,争取赢得时间,尽快完成样机试制。其中,必须解决与可能解决的技术难题,尽量在设计、试验、制造过程中,逐个解决;必须在样机制造出来之后,才能进行的顶锤与多缸活塞同步性试验,尽早做好充分准备。耐人寻味的是,为了保重点、抢进度,连铰链床身打腻子、喷漆这种修饰性工序也省略了,所以6×600吨铰链六面顶样机有个爱称“大老黑”。
当时,在试验样机的设计与试验中必须解决的关键技术问题有:
1六面顶主机的独特结构与材料问题;
2 超高压液压密封的问题;
3超高压单向阀和超高压管接头的问题;
4多缸活塞同步的问题;
5压力稳定与长时间保压的问题;
6顶锤的结构强度与寿命问题。择要回顾如下:
一、铰链六面顶主机的结构分析
六面顶超高压液压机,要求在其主机中心的叶蜡石压力腔内,稳定地建立7万~10万大气压的压力。当初设定腔体为φ10mm,叶蜡石方块为32×32×32mm,顶锤顶面22×22mm。在顶面面积上产生10万大气压需要的力是500吨左右,叶蜡石飞边上的压力损耗大约30%,由此,液压缸的吨位定为600吨。参考有关单位的经验,液压缸的材料准备采用炮钢,与炮钢强度对应的工作液体最佳压力应该是1250 kg/cm2。为了在超高压设备方面摸索一些经验,故意提高一级,选择液体工作压力为1500 kg/cm2 。
在缸樑结构的分析上,如果采用整体锻造,虽然结构更为紧凑,但加工未必方便。更主要的是超高压容器的设计缺乏经验,铰链梁的特殊结构,设计得正确与否,有待试验样机出来以后,进行应力测试。如果,缸、梁合为一体,使得零件受力的繁杂程度增大,一旦局部损坏,导致整体报废。再者,超高压工作缸的应力很高,而铰链梁的应力很低,相差十分悬殊,不宜采用同一种材料,因此,采用缸、梁分体结构。
铰链体的设计是主机结构设计中难度较大的部件,铰链床身的结构特殊,六面投影相同,等于只有一个投影。各部位的尺寸位置和操作空间,图面上无法测量。只能在强度计算和平面结构尺寸分配的基础上,做出几种轴测投影来判断空间位置的尺寸。第一稿铰链梁的两个端面是平行的,通过计算分析,组装成铰链床身后,操作空间很小,受力状况也不太好。经过反复多次的设计调整,最后确定,两个铰链孔中心距的尺寸为830 mm,相对内平面上翘70 mm.的结构方案最佳。这个问题,对铰链六面顶液压机的顺利发展有着直接的影响。一旦设计不当,顶锤不能从铰链连接的空间中安装进去,样机就不便使用或无法使用,必将造成大件返工,可能大大延误研制进程。
六组超高压工作缸安装在上、下、左、右、前、后六个铰链梁中。在主缸活塞的端面上,通过绝缘材料、大垫块和小垫块,安装六个顶锤,六个顶锤的顶面在压机中心构成一个立方形空间,用于放置叶蜡石块。主机的这种结构,既能适应顶锤尺寸的变换,又增加了几何对中的调节环节。一双扁螺母坐落在活塞上,作为可调节的定位机构。结构简单,调整方便,定位准确可靠。这些结构的制定,使主机满足了工业生产的要求,十几年的用户访问和四次改进设计,均得到继承和保留。
二、超高压密封的设计与试验
超高压密封是六面顶超高压液压机设计研究中最关键的一个问题,一旦密封漏油,采用等量供液原理的同步方案就没有基础,保压也不可能,更谈不上稳压的问题。严重的情况下,超高压都建立不起来。此外,即使密封性能尚可,而寿命不高,也不能用于生产。因为铰链式六面顶液压机结构封闭,更换密封时必须拆开铰链梁,不仅操作不便,而且影响设备精度。因此,超高压密封是研究制造六面顶超高压液压机的首要问题。
然而,在六十年代初,我国液压机行业只有200 kg/cm2~320 kg/cm2 的密封标准。即使是 200 kg/cm2 的密封产品,漏油是习以为常的。国际合作,四面楚歌。因此,要解决超高压密封问题,只有一条路——自力更生,寻求方案,自行设计,研究试验。而且,时间上必须赶在主机设计审定之前。就这样,在主机设计方案确定之后,首先进行超高压密封的设计研究和超高压密封试验台的设计与制造。要求在两个月之内完成阶段工作,进入超高压密封装置实体的密封性能与寿命试验。
超高压密封装置的设计,是从米赫耶夫的“高压密封装置的新结构”一书中推荐的V型橡胶密封圈入手的。
第一个方案是按书中介绍,对1000 kg/cm2 的超高压具有良好的密封性能的密封圈。作了两点修改,用到 1500kg/cm2,一是,增加V翼的厚度,提高耐磨性,增加高度,加强底部强度。二是,为提高材料的强度和耐磨性,改用聚乙烯塑料制造。
第二个方案是在进一步分析、比较了十多种密封结构的资料,发现Ο型密封圈具有形状简单,没有尖角,不致破坏油膜,可以双向密封的优点,决定自行设计Ο型密封圈加聚乙烯保护环的组合密封。Ο型密封圈的设计是参考前苏联“机械制造通报”杂志上,斯金斯基“关于园断面橡胶密封圈的强度计算”一文,对橡胶Ο型密封圈在第一种工作状况下,即Ο型圈断面变形到还未挤入密封间隙时的工作状况,应用它剪切层面的应力平衡方程式,计算出密封间隙、沟槽结构要素,预压量以及Ο型圈的截面尺寸。同时考虑以下措施,①采用耐磨性较高的聚乙烯塑料保护环来减小活塞与工作缸之间的间隙,保护Ο型密封圈;② 活塞上密封圈沟槽边缘的锐边只倒园R0.5,③ 选用强度极限与弹性模量比值较高的丁晴橡胶材料制造。
第三个方案是把第二方案中的整体聚乙烯保护环,改为膨胀环,利用膨胀环的弹性,进一步减小活塞与工作缸之间的间隙,保护 O型圈。
以上三个方案,经过超高压密封试验台的实体试验,取得下列试验结论:
1、采用两道Ο型密封圈加保护环的结构和Ο型圈加膨胀环的结构,都达到良好的密封性能和较高的试验寿命:
在1450 kg/cm2 的压力下,行程50 mm ,活塞与工作缸的间隙为0.05mm,的条件下,往复运动4 万次,最大泄漏量不超过 0.1 cc/min 。而且,磨损很少,还能继续使用。
2、V型密封圈的寿命在同样寿命4 万次的情况下,泄漏量达到0.25cc/min.
以上实物试验证明,Ο型密封圈加保护环的结构能够达到可靠的密封和8 万次以上的单向升压循环的工作寿命。实际上,铰链六面顶液压机的活塞最大行程为50 mm ,超高压工作行程只有几毫米,实际使用寿命将大大超过8 万次。
三、六面顶顶锤的设计与试验
六面顶顶锤的设计是参照两面顶顶锤的经验,采用Brigman 大支承原理和钢环箍紧的结构,最初设计成直径φ5×046mm ;顶面 22×22 mm ;侧面斜度为46 度;材料为硬质合金G6.等待铰链六面顶液压机试车后,进行试验。六面顶顶锤试验首先要解决的问题是:
(一)检验大支承的比例关系;确定顶面面积与圆锥体部分最大支承面积的比例,使顶锤达到最大承压的要求;
(二)通过试验,确定能够密封住叶蜡石高压密封腔的顶锤侧面斜度,保证叶蜡石腔体内建立7—10万大气压。
第一阶段的试验,
1、主要是试验不同顶面尺寸和改变顶锤压入钢环的过盈量,确定了使顶锤达到最大承压的要求,参照两面顶顶锤的大支承原理,顶面面积与圆锥体部分最大支承面积的比例为1比10 ;六面顶顶锤φ50×46顶面的面积加工成15×15;顶锤压入钢环的过盈量为5‰ ;通过这一轮试验,把顶锤顶面定为22×22mm,顶锤直径定为φ70×46mm.
2、能否保证叶蜡石腔体内建立7万——10万大气压,主要取决于三个因素:a.顶锤同步性比较好;b.叶蜡石组装块中的试料尺寸适当;c.叶蜡石在顶锤斜面之间的飞边具有足够的摩擦力。这三个因素是相互关联的,本阶段的试验就在于摸索、调整三者的关系,达到叶蜡石密封可靠,试料尺寸最大。通过本这一阶段的试验,取得了如下顶锤顶面几何尺寸的设计数据:
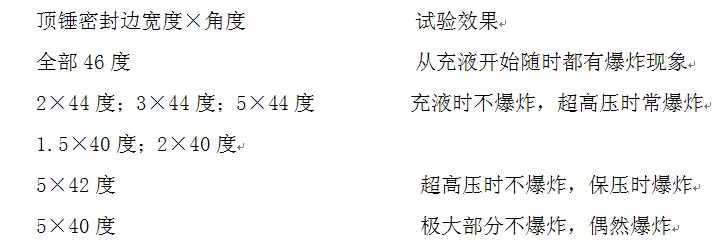
如果进一步减小顶锤斜面的角度,压力损失也将进一步相应增大。所以,从顶锤斜面的因素达到叶蜡石密封基本可靠以后,进一步减少、消除爆炸机率,应该从提高顶锤同步与优化叶蜡石腔体设计来解决。
四、多工作缸液系统同步性试验
(一)同步要求的由来:
1、使叶蜡石各密封边有足够的密封能力,避免试料在高温高压下爆炸;
2、使顶锤受力尽量均衡,提高使用寿命;
3、使叶蜡石腔体内压力尽量均匀,提高石墨向金刚石的转化率。
(二)同步偏差的概念:叶蜡石块压缩到额定压力后,六个顶锤行程的差别定义为同步偏差。
试验方案一、“等量供液加压”:
就是用六个等截面的工作缸,充于等量的高压油,推动六个等截面的柱塞等速前进,保证六个顶锤运动同步。试验表明,这个方案在理论上能够达到同步,实际上效果并不理想。表现在两个方面:
1、六只工作缸的油压不均匀,差别很大。当压力升高到200kg/cm2时,六缸压力分别为:200、160、130、60、180、和150kg/cm2,差别太大;
2、同步精度也不理想,当压力升到380kg/cm2时,上、下、左、右、前、后六顶锤的行程分别为3.14、1.24、3.14、1.27、--?、3.66mm.当压力升到400kg/cm2时,为3.92、1,48、2.76、1.42、--、?3.98mm 。最大同步偏差达到2.42mm和2.56mm 。造成同步偏差这么大的因素有漏油、制造偏差、管道长度、六个封闭容腔中的油量不同等等。
试验方案二、“自由充液与等量供液加压”:
为了消除制造偏差、弹性变形等偏差的影响,在进行超高压之前,先进行200kg/cm2以下的“充液”,然后等量供液加压。这个方案对
1、工作缸油压不均匀的问题解决得比较好;
2、对同步精度仍不理想。
试验方案三、“节流充液与等量供液加压”,通过分析,自由充液与等量供液加压的试验表明,自由充液阶段,因为六只缸是联通的,各缸压力差别不大,但也因为联通,各缸的供液量因阻力不同而不同,所以同步性不好。如果,在充液阶段,各缸的油路中加进各自的节流阀,用于调节各缸油路的阻力,就能平衡各缸的供液量,改善同步性。在这种试验方案中,又分两种情况:
1、在充液过程中随时调节阻力(供液量),这种办法,试验达到的同步精度很高,最大同步偏差在0.05—0.59之间,但手续不胜其烦,而且,调节时顶锤频繁错动,叶蜡石有破碎现象不适合工业生产。
2、把节流阀调节好以后,在充液过程中不调节,这种办法所带来的同步偏差大于上述0.59mm ,在0.22—1.38mm之间,基本满足合成工艺的要求。至此,单项试验暂时告一段落,试验样机转入金刚石合成工艺的移植试验。设备设计研究人员配合操作机器,深入了解设备性能。
1965年8月,三磨所派来了以王光祖为人造金刚石项目负责人的试验小组,其成员是,邵德厚、余志超、李进保、闫聚武等人,与试验样机的顶锤试验和同步试验一起,开展测温、测压的工作。随着顶锤试验的顺利进展,叶蜡石高压腔密封性日趋稳定,爆炸现象基本消除,用铋、铊、铯、钡四种元素,逐级测得了相应的相变点,证明铰链六面 顶液压机,能够在相应的叶蜡石试料腔内,稳定地建立起以上四种元素的相变压力。达到人造金刚石合成压力的要求。1965年10月,开始标定温度,进行金刚石合成工艺试验。1965年11月5日第一次合成出了人造金刚石,正式宣告铰链式六面顶液压机的研制成功。经过半个多月的重复试验,合成几率节节攀升,接近稳定。移交三磨所后,1966年样机在郑州的中间试验的过程中,完成了第六砂轮厂的建厂全套工艺准备的同时, 就生产了五万多克拉金刚石。为人造金刚石行业的形成和发展打下了良好的基础。紧接着,就为建设第一座人造金刚石专业生产厂,修改设计图纸,制造第一批铰链六面顶超高压液压机。
但是,前面提到,铰链六面顶超高压液压机是一个包含许多探索性难题的任务,要求在一年的时间内完成,时间十分紧迫。在这一年中,圆满完成了必须解决与可能解决的技术难题,建立了合成人造金刚石必须的高温、高压的条件,验证了合成工艺,可以稳定地获得了人造金刚石。同时也把第二层次的问题呈现得更清楚了。主要是:顶锤问题,虽然达到10个平均545次、最高700次,超过任务指标300次。但试验表明潜力很大;同步问题,虽然能达到0.22—1.38mm左右,平均0.8mm,也只是基本满足生产要求。同步方案探讨得尚少。当时的试验方案四,“分段充液,等量供液加压”由于当时试验样机忙于搬迁到郑州去做中间工艺试验,也因同步装置的设计和制造都还存在一定的问题,只试验不多,没有得出结果。只是随着生产的快速发展,依靠广大用户操作熟练,不断提高水平,改善效果。一直到1972年,为研究发展大颗粒单晶体和聚晶金刚石的需要,提出进一步提高六面顶压机同步保压性能的研究。(本文作者:济南铸锻机械研究所 陆乃焜;摘自《中国超硬材料工业五十年》)