磨削是利用磨粒进行材料去除的一种加工工艺,通过砂轮旋转,磨粒与工件接触并充当切割工具的作用,从而起到磨削作用。外圆磨削加工中,工件围绕固定轴旋转,加工表面与旋转轴同轴。
外圆磨床制造工艺自工业革命时期就有所发展。1830年Jonathan bridges 和James Wheaton制造出第一台现代外圆磨床。1876年Joseph brown研制出带有砂轮的车床并获得专利。1925年Norton改善了外圆机床实现了更高转速和更精确的磨削公差。将CNC和PC集成同一个动力系统进一步深化了机械制造控制工艺,大大节省了人工操作。两个平面从相对方向移动接触,加工操作更加流畅。Krabacher研究了材料去除率和表面粗糙度等加工参数,发现材料去除率降低时工件表面质量就会得到改善。Heaker and Liang预测表面粗糙度主要跟磨削过程的切屑厚度有关。Vickers taff研究了工件表面粗糙度与砂轮进给速度和砂轮磨损的关系。Rama Chandran 利用回归分析法和数学模型研究了进给和切割深度对砂轮磨损及表面光洁度的影响。但外圆磨削附件对工件表面粗糙度的影响却鲜有研究,尚未见报道。
本研究对外圆磨削基本概念和外圆磨削附件制造进行了介绍,还有回归分析法;并研究了磨削参数对湿加工、干加工条件下的表面粗糙度的影响。
外圆磨削的基本概念
外圆磨床的基本组件包括砂轮架、横滑板、轮轴头架、和尾座。砂轮架将驱动电机和主轴连接;横滑板能够使砂轮架从工件移动到尽头;轮轴头架对工件确定位置、夹持。尾座用来夹持工件的另一端,如图一所示。
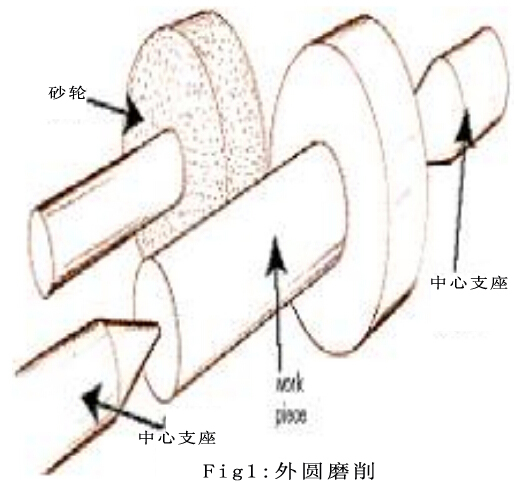
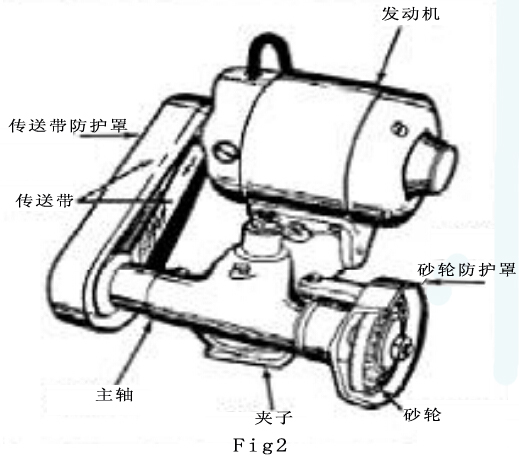
附件制造中用到的组件有:发动机、砂轮、固定台、柄轴、轴承、皮带轮和传送带。
发动机:
发动机是一种能够把其它形式的能转化为机械能的机器,包括内燃机和电动机等;电动机是将电能转化为机械能,AC电机则能实现机械能和交流电能相互转换。本实验使用的是AC电机,用于砂轮旋转,如图三所示。0.5 H.P,2800 RPM,3相,0.37 KW, 0.75 AMPS. 440伏。
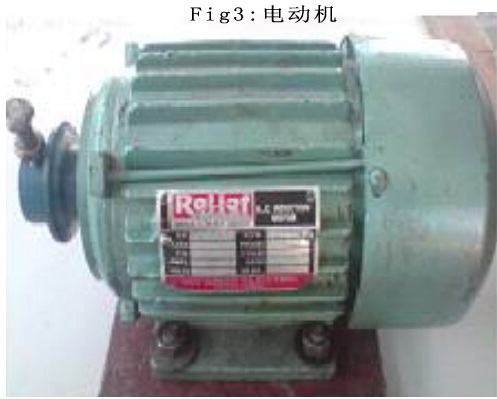
本实验采用刚玉砂轮,如图四所示;Carborundum Universal公司生产、刚玉磨料、直径200 mm、厚度20 mm、孔径31.75mm、最大速度3150 Rpm。
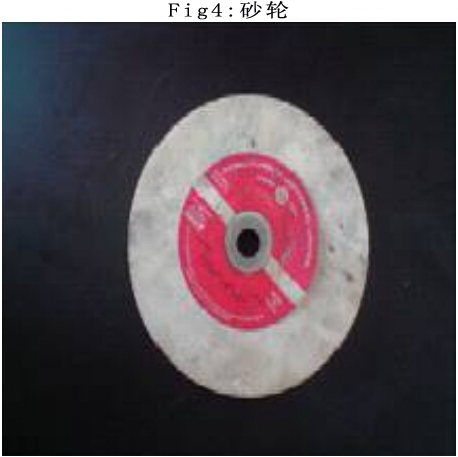
本实验采用12”×6”的MS台,将刀架从车床上移走之后装置上固定台,固定台对整个附件承重,用于移动砂轮和发动机。
杆柄:
本实验的附件采用两种柄轴:固定柄轴,直径76 mm,内孔径40 mm;旋转柄轴,直径17 mm。如图五所示。
发动机通过传送带和皮带轮带动柄轴旋转从而带动砂轮旋转;利用球轴承将旋转柄轴装配在固定柄轴内。利用钎焊将固定柄轴焊接在固定台上;球轴承装配在固定柄轴内部用于旋转柄轴的移动,然后再将砂轮固定在旋转柄轴上。
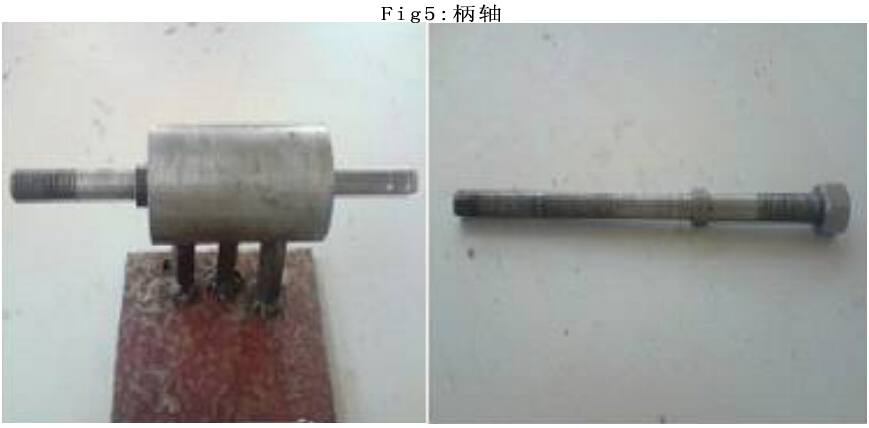
本实验的附件采用两种类型的轴承:球轴承和止推轴承。
球轴承是将球滚珠装配在内钢圈和外钢圈的中间以承受较大载荷的一种滚动轴承;通过两个轨道将负载传递到钢珠上,其中一个轨道为固定轨道,另一个轨道可以转动从而带动钢珠滚动;主要用于减小转动摩擦,提供径向负载和轴向负载。由于钢珠间接触面较小,所以球轴承的负载容量就小;但可以允许内外轨道间存在一定未对准误差。由于钢珠制造成本低廉,球轴承在滚动轴承系列中是比较便宜的一种。
止推轴承一般是由两个止推垫片或更多止推垫片和若干滚动体组成,能够承受较大的轴向负荷。外直径40 mm,内直径17 mm。如图六、七所示。
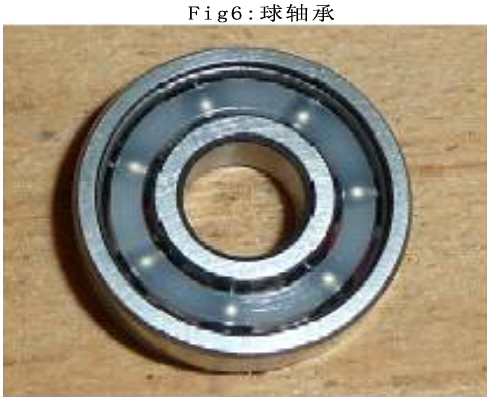
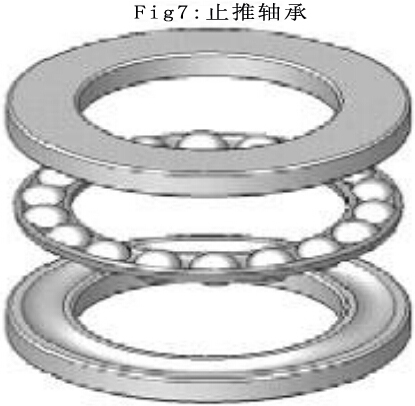
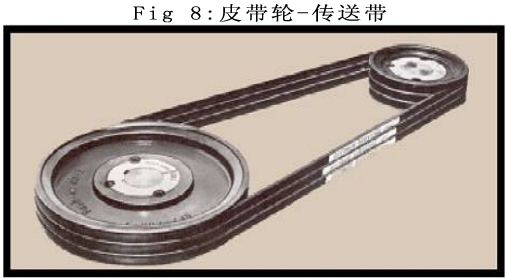
1. 在固定台上钻孔,并将发动机固定。
2. 利用准线将固定柄轴置放在车床的中心高度位置,该高度位置由方棒保持。
3. 将固定柄轴和固定台跟方棒焊接在一起。
4. 利用球轴承将转动柄轴嵌入固定柄轴(如图九所示)。
5. 利用塑料镶套将砂轮紧夹在旋转柄轴上。
6. 将法兰盘放置在砂轮两边防止砂轮从柄轴上滑脱。
7. 将用于砂轮自由运动的止推轴承装配在旋转轴上。
8. 旋转柄轴上装配的组件顺序依次为:止推轴承、法兰盘、砂轮、法兰盘、螺母。
9. 安装皮带轮。
10. 安装传送带(如图10所示)。
11. 将车床上的刀架拆卸,然后将装配好的以上组件固定在车床的横滑板上(如图11、12、13所示)。
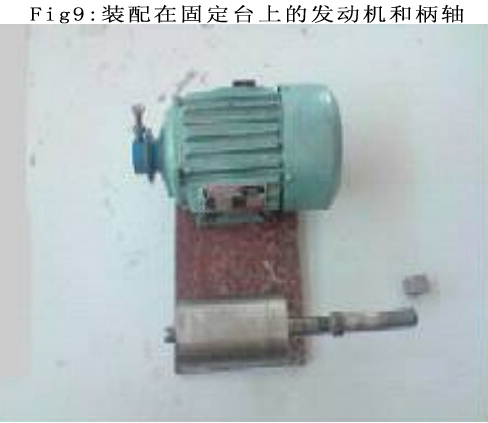
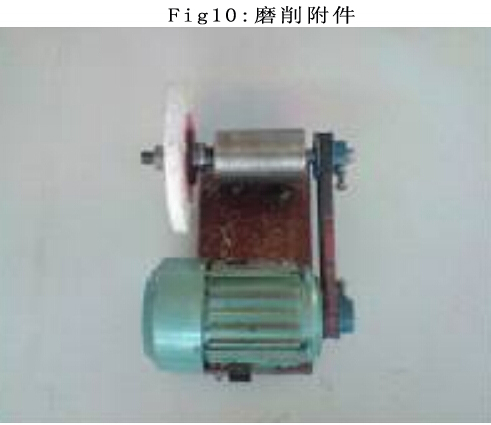
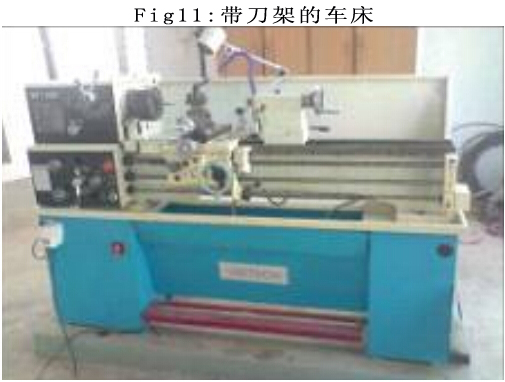
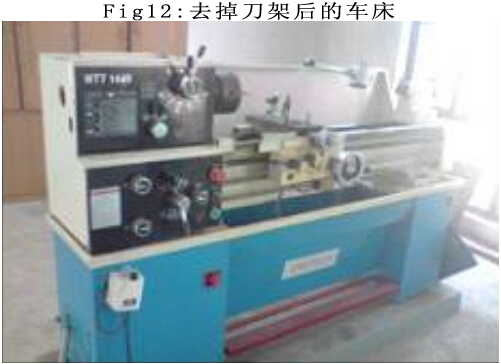
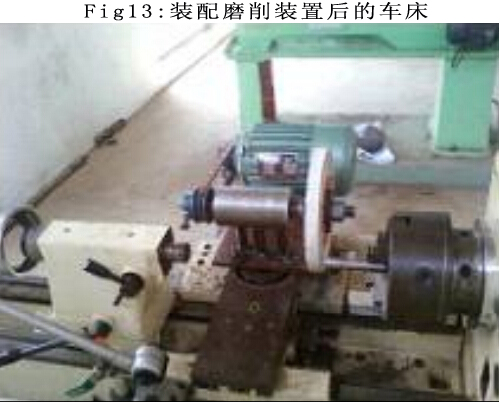
磨削工艺和参数
本实验中用到的外圆磨削工艺采用横向研磨,干磨和湿磨。湿磨所用切削液为水基乳液,组份为90%水、5%切削油、2%硝酸钠、2%乳液和1%纯碱。
设计矩阵
工件旋转速度和砂轮的轴向运动也叫做横向进给速度,连同切削深度一起都是本研究所用到的参数。表一为这些参数的不同值。
实验采用两级全因子设计矩阵,表二为干磨、湿磨输入参数所求得的表面粗糙度(Ra)。
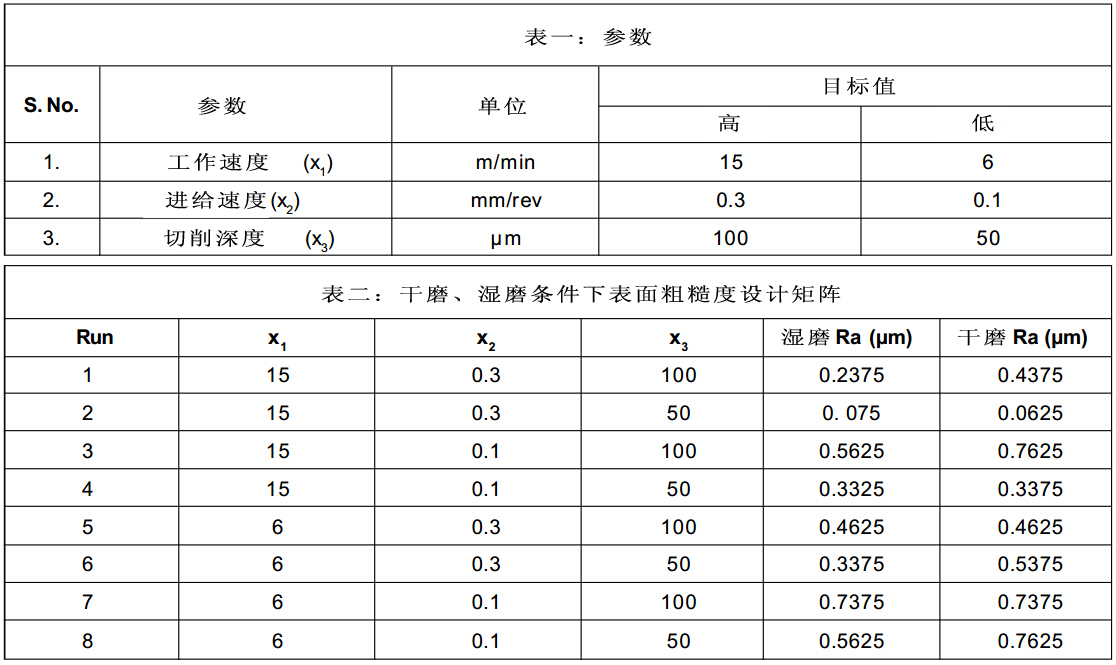

对以上数值进行回归分析,用耶特算法进行变量分析(ANOVA)。最终回归公式如表三所示。
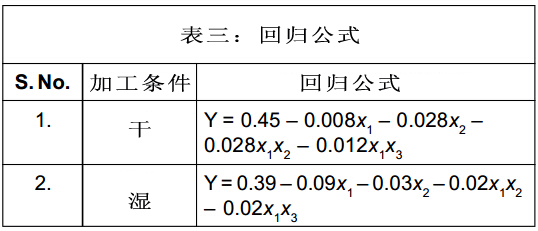
利用回归分析法,在干磨、湿磨条件下求得了理想表面精磨的最佳输入参数。车床外圆磨削工艺实现了低成本制造。干磨条件下最佳参数值为:工作速度15m/min,进给速度0.3mm/rev,切削深度50μm。湿磨条件下最佳参数值为:工作速度15m/min,进给速度0.1mm/rev,切削深度50μm。(编译:中国超硬材料网)