中国海洋大学
摘要:采用悬浮法进行电镀金刚石线锯的实验研究。通过单因素实验方法,借助扫描电子显微镜,研究了复合镀层表面的形貌。结果表明,当工艺参数为金刚石磨粒质量浓度80g/L、分散剂质量浓度2g/L、电镀时间20min、平均电流密度2A/dm2时,能够获得金刚石磨粒分布均匀、符合实际切割需要的电镀金刚石线锯。
关键词:悬浮法;电镀金刚石线锯;工艺参数
中图分类号:TG717文献标志码:A
1·引言
近年来,在大尺寸半导体基片和功能晶体的切割中,固结磨料线锯以无可比拟的优势被认为是最好的切割材料之一。与现有的几种固结超硬磨粒的方法相比,电镀方式具有制造周期短和生产成本低等优势,且电镀线锯具有耐热性和耐磨性良好等特点[1]。金刚石线锯是将高硬度、高耐磨性的金刚石磨粒通过电镀的方式牢固地把持在钢丝基体上而制成的一种切割工具[3]。其制作工艺一般可分为埋砂法和悬浮法。目前,国内对电镀金刚石线锯的研究尚处于初步阶段,而且大都采用埋砂法进行电镀,此种方法虽然制作线锯的性能较悬浮法有所增强,但是其生产成本相对较高,制作周期较长,较不易于大规模工业化生产。本文采用悬浮法进行实验研究,得出了此种方法制作的最佳工艺条件。
2实验
2.1实验设备和仪器
实验设备和仪器包括:国华电器有限公司的HH-6型数显恒温水浴锅,金坛市医疗仪器厂JJ-6型数显直流恒速搅拌器,香港龙威仪器仪表有限公司PS-302DM型直流电源(输出电压:0-30V连续可调,输出电流:0-2A连续可调),上海精纯仪器设备有限公司NDJ-1型旋转粘度计,日立TM-1000扫描电子显微镜。
本实验采用瓦特型镀液(硫酸镍250g/L,氯化镍30g/L,硼酸30g/L,十二烷基硫酸钠0.03g/L,1,4-丁炔二醇0.8g/L,PH=5.0,T=45℃)。电镀槽材料为PVC,尺寸为400mm×150mm×200mm。线锯基体采用抗拉强度高、柔韧性好的韩国Kiswire进口钢丝(直径120μm)。镍片(纯度99.9%)作为该实验的阳极,金刚石磨粒采用河南黄河旋风股份有限公司的B级金刚石颗粒(粒径15μm),每次所镀线锯长度为200mm。
2.2实验方法
电镀金刚石线锯制作工艺流程为:前处理→镀液中进行施镀→后处理。
(1)前处理
在施镀前,对钢丝以及金刚石磨粒的前处理必不可少,处理的完全与否直接影响着线锯的质量。对于钢丝的前处理,主要针对其表面油污的处理。油污的存在会影响镀层与基体的结合力,同时还会污染镀液,严重影响线锯的质量。本文采用化学法除油,利用碱液对油脂的皂化作用,去除造化性油脂。钢丝在碱液煮沸30min,用去离子水清洗后,再在丙酮溶液中浸泡30min,以去除仍然残留在基体上的有机物,最后用去离子水冲洗干净即可。对于处理后的钢丝,可以采用简单的方法测试其清洁度,根据油污不能被水润湿的原理,将几滴水珠滴在钢丝上,除油不彻底时,表面水滴成球形,表面倾斜时会沿钢丝滑落;除油彻底时,水滴散布于表面呈水膜[4]。
金刚石颗粒一般是经过高温高压制备而成,生长过程中一些金属催化剂(如Mn、Fe、Ni、Co)及其碳化物作为包裹体被留在金刚石颗粒内部,包裹体对金刚石的强度和热稳定性都有负面影响[5]。因此,在使用之前要进行磁选处理。本实验采用先酸洗后碱洗的工艺。用10%的稀硝酸溶液煮沸30min,待溶液冷却后,用去离子水水洗至中性,再用10%的NaOH溶液煮沸30min,冷却后水洗至中性,最后用镀液浸泡以备使用。实验表明,该处理工艺能较好地使金刚石颗粒磁性减弱,可以减轻或降低金刚石颗粒导致的镀层微观结构的恶化。
(2)施镀过程
阳极镍片及基体钢丝需进行镀前活化,镍片需在10%稀硫酸溶液中放置5min,同时将钢丝浸泡于10%盐酸溶液中5min,取出后,进行施镀。施镀过程中,采用搅拌器进行搅拌(200r/min),并且保持镀液的清洁。
(3)后处理
电镀结束后,将线锯从镀液中取出,并用去离子水冲洗,使粘附在线锯上的金刚石颗粒回到镀液中。随后在马弗炉中进行除氢处理,温度为200℃,时间为2h。原因为在电镀过程中,阴极上除了金属离子放电结晶外,镀液中还会发生电离生成一定量的氢离子,一部分氢离子在阴极上还原成氢气,并与金属同时在阴极上析出或吸附在阴极表面形成气泡、针孔等缺陷;另一部分则以原子状态向镀层和基体内部扩散,使晶格畸变,产生较大的内应力,导致镀层变脆,故要进行除氢处理[4]。
3结果与讨论
从锯丝的上下表面砂量均匀性、磨料分布密度等方面,分别考察分散剂质量浓度、金刚石颗粒质量浓度、平均电流密度和电镀时间对锯丝砂量的影响。
3.1分散剂质量浓度对锯丝上下表面上砂量的影响
本实验采用增加镀液粘度的方式,提高颗粒的分散性能,以解决悬浮法电镀所造成的线锯上下表面砂量不均匀的现象。使用羧甲基纤维素钠(CMC,粘度8000-12000)作为分散剂,其性质稳定,抗盐性较好,分散性能较为理想,但由于CMC具有成膜性,镀液应2-3个月更换一次,以免在基体表面成膜,影响施镀。
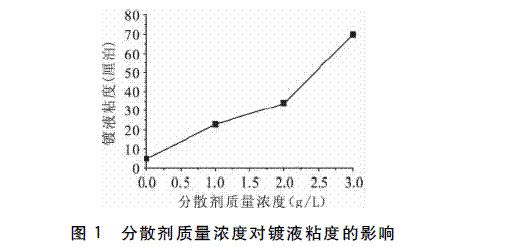
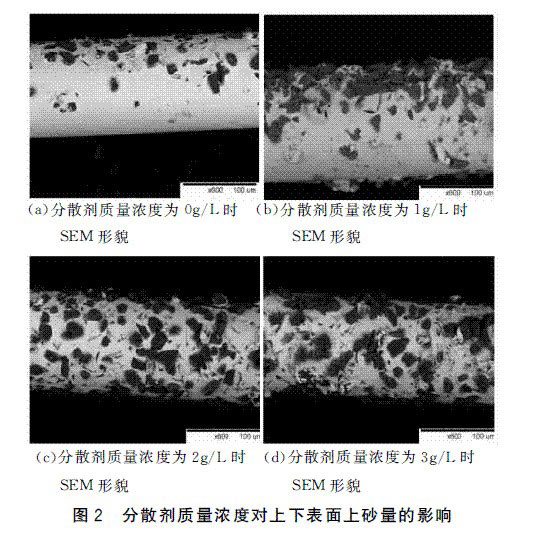
3.2金刚石微粒的质量浓度对锯丝砂量的影响
分别采用质量浓度为60g/L、70g/L、80g/L、90g/L金刚石颗粒进行研究(CMC质量浓度2g/L,其他条件保持一致)。从图3可以看出,镀液中磨料质量浓度增大使上砂量有明显的提高。如图3a和图3b所示,磨料质量浓度在60g/L-70g/L时,线锯表面砂量分布较为均匀,但密度较低,实际切割效率不高。质量浓度达到80g/L时,镀液中磨料的提高增大了紧靠基体一层磨粒的质量浓度,相同时间内金刚石磨粒沉积量增多,上砂量得到明显提高(见图3c)。磨粒质量浓度达到90g/L时(见图3d),表面金刚石磨料分布密度较大,有堆积现象产生,把持力降低,缩短了使用寿命,不利于实际应用。综合考虑金刚石磨粒消耗及锯丝质量,最佳金刚石质量浓度为80g/L。
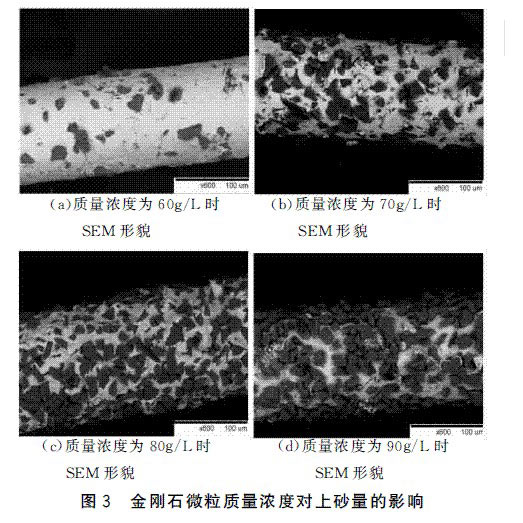
3.3平均电流密度对锯丝砂量的影响
取电流密度为1.5A/dm2、2A/dm2、2.5A/dm2进行研究(CMC质量浓度2g/L,其他条件保持一致)。如图4所示,平均电流密度对上砂量的影响较为显著,整体呈现增长的趋势。这是因为阴极过电位会随着电流密度增大而增强,进而提高了对金刚石微粒的吸附力,有利于金刚石磨粒在线锯上沉积。但是当电流密度增大到2.5A/dm2时,如图4c所示,金刚石磨料在镀层中重叠问题比较严重,直接影响切割质量。所以,最佳电流密度应为2A/dm2。
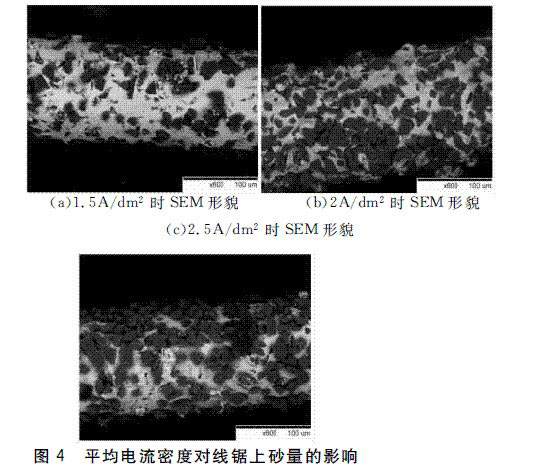
3.4电镀时间对锯丝砂量的影响
分别进行10min、15min、20min、25min的电镀实验(CMC质量浓度2g/L,其他条件保持一致),研究电镀时间对上砂量影响的情况,当电镀时间为10min时,由于金属沉积时间较短,镀层较薄,把持不住磨粒,导致线锯上砂量较小。从15min至20min,复合镀层逐渐形成,并且逐渐变厚,金属与磨粒共沉积效率提高,上砂量同时增加,如图5b和图5c所示。当电镀时间达到25min时,复合镀层中磨粒相互接触、堆积,导致其间的把持力降低,部分磨粒容易脱落,且锯丝较为粗壮,切割效率降低。所以,最佳电镀时间为20min。
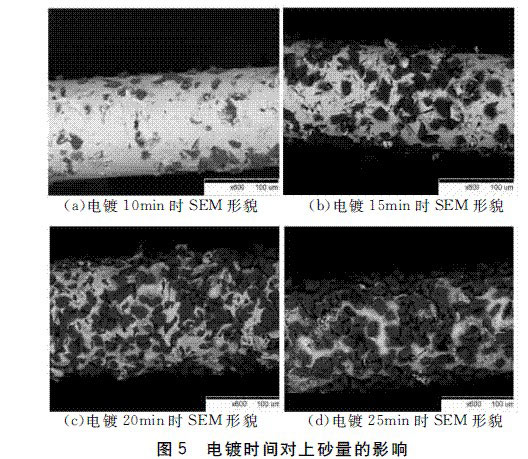
由上述确定的最佳工艺条件进行电镀金刚石线锯的实验,得到锯丝形貌如图6所示,从图中可看出,锯丝表面磨料分布较为均匀,上砂量适中,适宜实际切割。
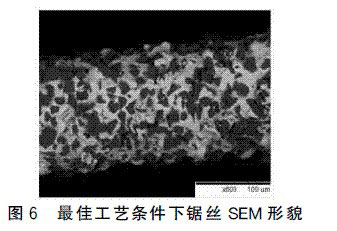
4·结语
本文以Kiswire120μm钢丝为基体,15μm金刚石颗粒为磨料,采用瓦特型镀液(硫酸镍250g/L,氯化镍30g/L,硼酸30g/L,十二烷基硫酸钠0.03g/L,1、4-丁炔二醇0.8g/L,PH=5.0,T=45℃),用悬浮法进行工艺研究,通过扫描电子显微镜图片分析锯丝表面上砂情况,得出了符合实际切割需要的电镀金刚石线锯的最佳操作工艺条件为:金刚石磨粒质量浓度80g/L,分散剂(CMC)质量浓度2g/L,电镀时间20min,平均电流密度2A/dm2。
参考文献(略)