摘要 在第十四届中国国际机床展览会(CIMT2015)上,国内外各机床及配套产品产商根据对用户及市场的了解推出了自己的产品,这不仅是先进制造技术在机床工具行业的应用成果展览,更是对参展企...
在第十四届中国国际机床展览会(CIMT2015)上,国内外各机床及配套产品产商根据对用户及市场的了解推出了自己的产品,这不仅是先进制造技术在机床工具行业的应用成果展览,更是对参展企业的风采的展示。高速切削技术在近年来变成了一个热门的话题,高速切削所带来的效率和工件表面质量的显著提高使得工件加工的总费用下降了至少40%。这个结论成为高速切削技术的理论基础和动力,随后的研究是围绕着如何提高刀具耐磨度,如何使机床的结构、主轴和驱动控制系统能满足高速切削技术的要求而进行的。
随着国内用户对高速加工的了解不断深入,高速加工机床的需求量会越来越大,从而会影响机床制造商在高速加工机床的研发、制造方面增加投入。目前境内外的高速加工机床在主轴和驱动控制系统上的差距不是很大,但是在结构和刀具上的差距仍然很大。前者影响了加工效率,后者是对机床稳定性的挑战。
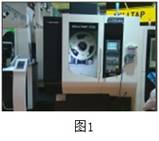
一、钻攻中心
1、德马吉森精机(DMG MORI)MILLTAP700高速钻铣中心(见图1),紧凑的机身设计同时确保了宽阔的加工区域,实现了刀对刀0.9s的换刀速度,主轴最高转速可达24000r/min,三轴快移60m/min,可选配探头套件和直接测量系统包,显著提高了加工速度和效率。
2、山崎马扎克VCP400L高速钻铣中心(见图2),机器宽度仅为1280mm,后排屑设计和无需机器左右保养区域的设计,可以将机器的占地空间降至最小,刀对刀0.9s快速换刀,主轴转速12000 r/min,三轴快移60m/min,搭载Mazak FZ[Fanuc 0i]系统,增加了MAZAK独有的便利菜单,实现良好的操作性。
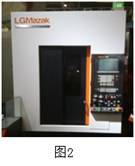
4、宝鸡ZH7120G钻削中心(见图4),最高转速20000 r/min,三轴快移48/48/60 m/min;Z轴快移速度达到60m/min,减少了高速钻攻时的空转时间,在减少成本的同时有效提高了加工效率。
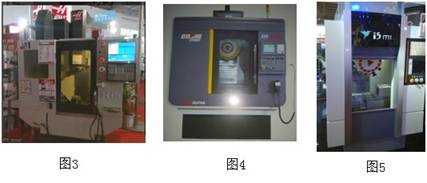
二、高速加工中心
1、现代威亚I-CUT400T(见图6),三轴加速度达到1G,快速移动为56m/min,显著减少非切削时间;可选配双臂式刀库,刀对刀换刀时间为1.6s,屑对屑换刀时间1.89s,同时选用的是伺服电机驱动换刀系统,大大增强了刀库的稳定性;主轴最高转速可达15000 r/min,逆旋转时可通过2倍的后进,从而减少加工时间。
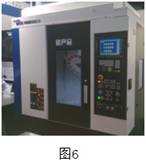
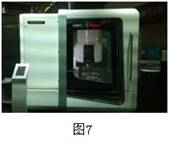
4、沈阳机床i5 M4智能立式加工中心(见图9),主要应用于汽车、摩托车零部件的加工,性价比高,稳定性好,95.5Nm的超大扭矩使加工强壮而有力。同时机床标配智能误差补偿功能,精加工精确无比,三轴快移48m/min,主轴转速10000 r/min。
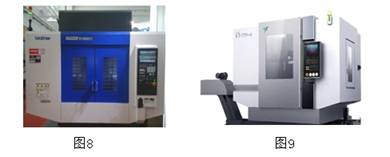
一台优秀的高速加工机床,应体现一个完善的加工方案。高进给速度要求高加速度,在高速加工时采用干式切削,充分考虑加工安全性,CNC采用以太网通讯,油雾吸收过滤、除尘、红外工件测头等装置的配备,对于零件高速加工是必不可少的。纵观国内外高速加工机床的发展,无不是围绕着这些技术要求进行的。
通过这次展会,我们看到国内的高速加工机床已经茁壮成长,有些方面与国际一流产品不相上下,甚至略有超越;但在系统开发以及机床稳定性、产品人性化设计等方面还有较大差距,只有不断创新才能有更大的发展空间。