本研究利用高速钢钻头对聚合物复合材料(PMC)进行钻削加工并研究其表面光洁度。实验利用800、1000和1200目的碳化硅、氧化铝磨料,借助冷却液和泥浆系统对PMC进行钻削加工。磨料既可以起到冷却作用,又可以增加表面光洁度和MRR并减缓工具磨损。研究中用到的机床为CNC钻床;采用田口实验设计法;利用多性能特征对钻削参数(进给速率、主轴速度、磨料粒度、磨料类型、泥浆浓度)进行优化以便对表面光洁度进行研究。研究结果表明:进给速率、磨料类型和泥浆浓度是影响钻削工艺中表面光洁度的最显著因子。
关键词:
磨料,ANOVA,钻削,田口实验法,聚合物复合材料,表面粗糙度,MRR
1、引言
钻削是一种基础性加工工艺,用于材料去除的加工,并常用做铰孔、攻丝、和钻孔等加工工艺的预备加工,并朝着高效生产的高速设备方向发展。钻削通常利用钻头这类多刃切割刀具在实体材料上加工圆孔或者扩孔。研究表明高切割速度、高进给和大切割深度的高效加工和钻削常常伴随着较高的热量和切割温度,从而降低加工精度并缩短工具寿命。钻削是汽车制造和航空航天领域中结构性框架装置的重要加工工艺,而钻孔的质量则显著影响着接头的寿命。制造加工业特别是自由贸易和全球成本竞争带来的挑战迫切需要高生产效率、高产品质量和整体经济效益,同时也推动着切割工具朝着材料去除率高、稳定性强、工具寿命长的方向发展。
2、文献综述
J.Pradeep Kumar采用田口实验法利用HSS螺旋钻对OHNS材料进行钻削加工以研究钻削参数对表面粗糙度、工具磨损、材料去除率和孔径误差的影响;采用田口正交阵列、S/N比、ANOVA和回归分析法来研究钻削参数对钻孔质量的影响。本研究做了L18正交阵列实验系列;实验结果进行收集并利用MINITAB13软件进行分析。利用线性回归公式建立钻削参数和钻孔质量特征之间的关系。对实验实测值和预测值进行对比,具有较好的一致性。
Yogendra Tyagi采用田口实验法,利用CNC钻床对高速钢进行钻削加工。利用田口法对实验结果进行阐述以弄清每个最佳工艺参数的影响因子。利用L9田口阵列和ANOVA对参数配置的变化步骤进行阐述分析。研究表明表面光洁度和材料去除率是加工质量的一个特征并直接影响着加工效率。为使表面粗糙度最小化并提高材料去除率,实验对最佳加工参数(主轴速度、切割深度和进给速率等)的选择进行了分析。
Arshad Noor Siddiquee主要研究了以田口法为基础的深孔钻削参数优化,以便实现表面粗糙度最小化。实验利用整体硬质合金刀具在CNC车床上对奥氏体不锈钢AISI321进行加工;对切削液、速度、进给和孔深进行了研究。采用田口L18正交阵列实验设计方法。利用S/N比和ANOVA分析来研究加工参数对表面粗糙度的影响及其影响比例。
B.V.Kavad的研究表明钻削加工是玻璃纤维增强塑料(GFRP)制备和组装的重要工艺。实验尝试了传统钻削、振动钻削、超声波钻削等不同工艺,以此来保持材料的完整性和加工精度。该研究主要分析钻削加工参数对GFRP脱层损害的影响。在传统加工工艺中,进给速率、刀具材料和切割速度是影响分层的重要参数,因此,高速加工、硬质刀具材料和低进给速率可以实现GFRP较少的分层。振动钻削和超声波钻削的推力较小,因此比传统钻削工艺更能够实现较低的分层。
3、加工装置
图一为实验所用机床;切削液为碳化硅磨粉浆和800、1000、1200目的氧化铝磨料;粉浆浓度为20%、25%和30%。工件材料为聚合物复合材料;利用Mtiutoyo SJ-201P仪器对所有加工试样的表面粗糙度进行测量并求得平均表面粗糙度Ra。
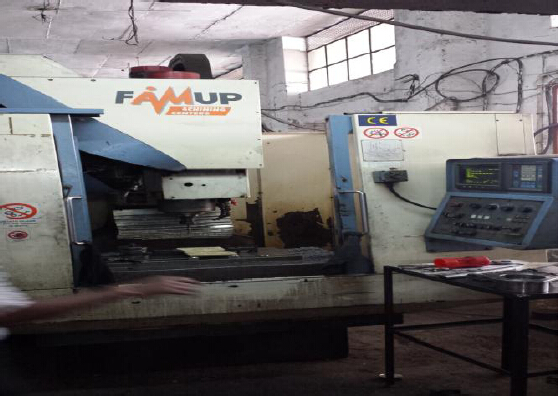
复合材料通常包括多种组份,其中聚合物为基体,各种纤维为补强材料。玻璃纤维是PMC材料中最常见的补强材料。只有将树脂组份和增强纤维结合才能发挥材料的卓越性能。当复合材料受负载时,树脂基体将载荷分散到纤维之间,从而保护纤维免受磨损和冲击。复合材料强度高、韧性好、复杂形状的制模成形比较简单,且抗环境影响性好;整体性能比一些金属更优越,广泛应用于诸多设备中。本实验所用工件材料的组份如表一所示。
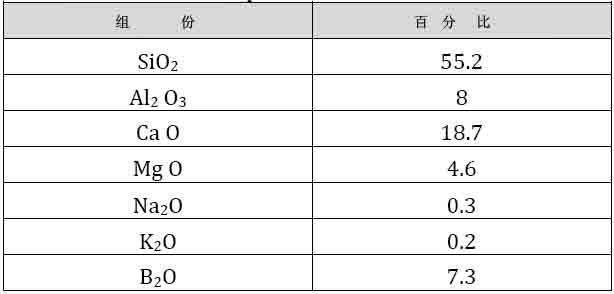
磨料可以定义为利用磨削或研磨原理采用硬度极高的材料对其他材料进行成型加工和其他工艺处理的材料。磨料可以用于自由磨粒、砂轮、纱布和砂纸等;也用在金属加工工艺的陶瓷切割刀具上。由于其耐火性和超高的硬度,磨料在高速加工、切割深度和精加工光滑度方面有着显著的优势。人造磨料主要有碳化硅、氧化铝和立方氮化硼等。
4、实验
本研究选取五组不同加工参数进行实验。工件材料因子有两组,其他参数如切割深度、工作台速度、粒度和粉浆浓度都各有三组。采用L18正交阵列实验设计。实验中的术语“signal”代表适宜可取的值,“noise”代表不需要的值。利用ANOVA预测不同工艺参数对性能特征的影响百分比。表3为五组工艺参数:磨料类型、进给速率、主轴速度、粒度和粉浆浓度。利用田口实验设计方法。利用Minitab16软件对工艺参数的影响进行建模。利用田口法求得S/N比。
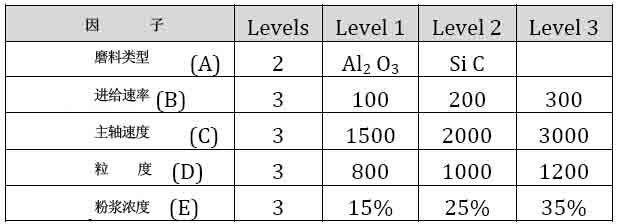
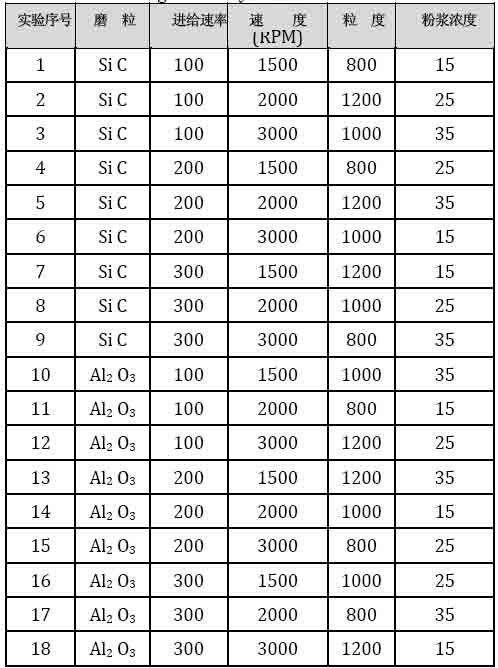
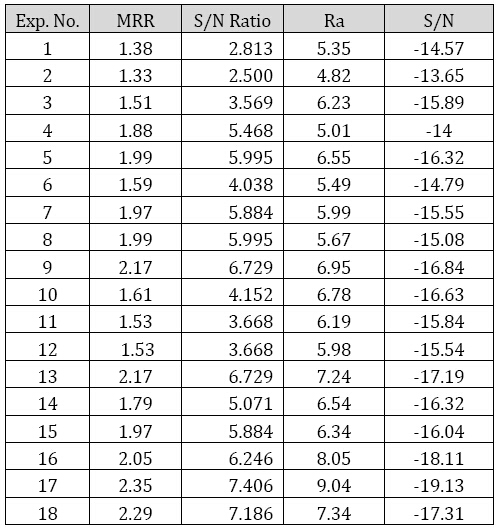
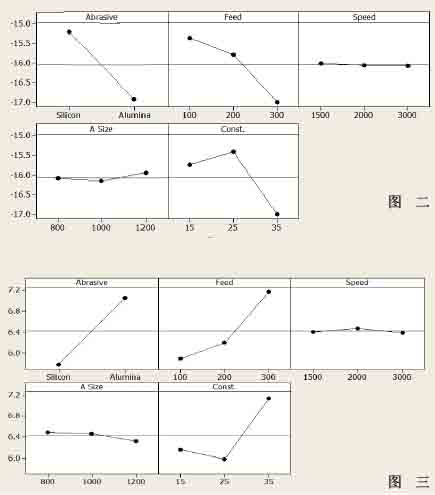
粗磨料的使用导致表面裂缝增大,进而使表面粗糙度变大,并降低了表面质量。而精细磨粒则降低了表面粗糙度。1200目的磨料加工出的表面粗糙度要比800目和1000目磨料的好。当粉浆浓度为20%和25%时,表面光洁度最佳。
实验发现碳化硅磨料钻削得到的表面粗糙度值要比冷却液辅助钻削得到的表面粗糙度值低。这主要是由于碳化硅钻削加工中的材料去除率低。由于MRR低,钻削过程中PMC表面没有出现孔穴。
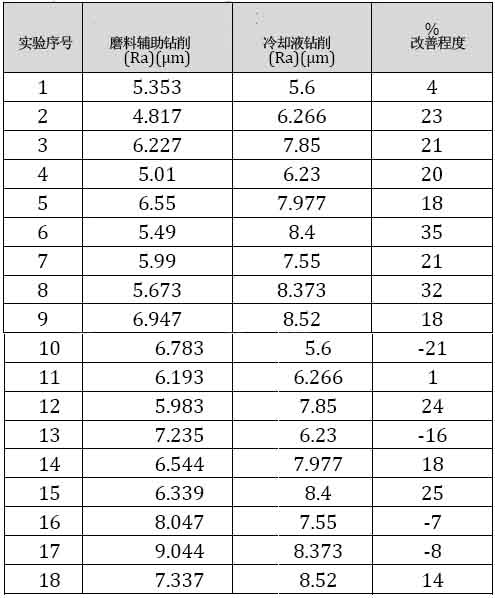

由此可以看出,碳化硅钻削过程中的表面光洁度有21.33%的改善;氧化铝磨料钻削过程中的表面光洁度有3.33%的改善。
6、ANOVA
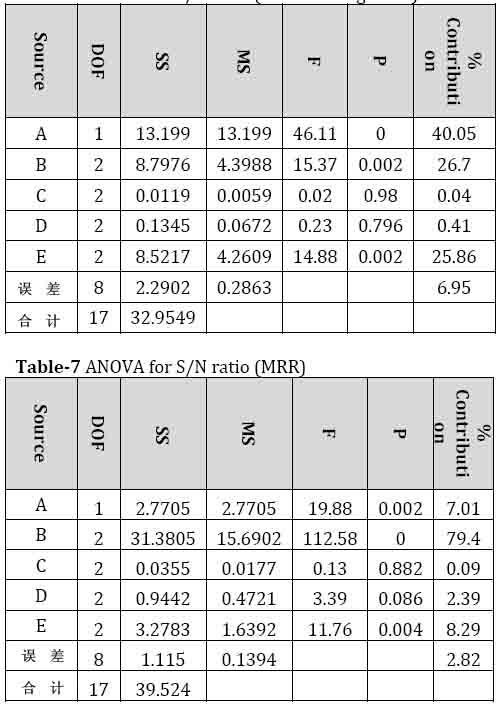
对于MRR,进给速率的影响百分比为79.40%;粉浆浓度占8.29%;磨料类型占7.01%。磨料粒度占2.39%;速度占0.09%。
7、结论
对于表面粗糙度,25%浓度的1200目碳化硅、100mm/min进给速率和2000rpm旋转速度为磨料辅助钻削的最佳工艺参数。
和冷却液钻削相比,碳化硅粉浆钻削得到的表面粗糙度的平均改善程度为21.33%;氧化铝粉浆钻削得到的表面粗糙度的平均改善程度为3.33%。
对于MRR,35%浓度的800目氧化铝磨料、300mm/min进给速率和2000rpm旋转速度为磨料辅助钻削的最佳工艺参数。
和冷却液钻削相比,磨料辅助钻削(碳化硅粉浆)工艺得到的MRR平均改善程度为2.02%;而氧化铝粉浆工艺得到的MRR平均改善程度为10.6%。
在所有所选参数中,磨料类型、粉浆浓度对磨料辅助钻削工艺中PMC材料的表面粗糙度的影响最大;Rpm和粒度影响较小。在高速、大粒度和适当浓度的条件下,表面粗糙度达到最小。进给速率和磨料类型对MRR影响大,而RPM和粒度对MRR的影响则较小。(编译:中国超硬材料网)