关键词:
工业陶瓷,磨料研磨,表面精整,磨除材料总量
引言
陶瓷是一种由元素周期表III-VI族中的非金属和金属化合物构成的多晶材料及制品;通过对源材料的烧制和成型加工制备而成。天然形成的化合物如硅酸盐、粘土和石英以及人造陶瓷(高纯氧化物、碳化物和氮化物等)都可以用作源材料。
工业陶瓷在机械工程领域广泛应用于结构性耐高温耐火零部件,如器材壳体、坩埚、齿轮和涡轮叶片的生产;还用于仪器仪表和化学工业中环境较为恶劣的条件下的使用。
陶瓷的机械加工是一种繁琐费力的加工工艺,旨在实现加工零部件的所需精度和工件表面质量要求;其加工方法有下述几种:
i.磨料研磨
ii.电火花、电化学加工
Iii.超声波加工
iv.水动力加工
v.激光切割
陶瓷机械加工常见工艺有磨削和精整(Breev B.T. 1982, Antyufeeva T.P. 1999)。
天然及人造刚玉、碳化硅和碳化硼等材料常用于陶瓷的磨削和精整;而金刚石抛光则常用于锗、硅、玻璃、石英和固态合金的加工处理。金刚石抛光工艺具有磨损小,工具耐用性高的优点。根据日本研究者的实验数据,陶瓷抛光的成本费用是结构钢精整加工的成本费用的10倍之高(A.P. Garshin 2003, J. Kang, 2005, Jeong-Du Kim, 1995)。
陶瓷材料的性能如硬度、脆性、强度、多孔性、表面态、热稳定性,以及磨料属性和所用刀具等都会影响陶瓷的机械加工;而陶瓷切削速度、夹持力和抛光材料的冷却等加工条件也会影响陶瓷的机械加工。一般情况下,陶瓷的机械研磨由三步骤工艺流程:粗加工、清洁处理和精加工。
第一步,利用大粒度工具磨除80%左右的材料并以渐增速度进行磨削加工处理;该处理工艺会在工件表面产生较深的裂缝和损伤。工件尺寸的粗公差可达0.3-0.5mm;根据零部件的尺寸,可分为单面和双面。第二步,利用小粒度研磨工具进行磨削加工并降低磨除材料量。第三步,利用金刚石微粉和研磨膏进行精整加工,达到标称尺寸。该步骤工艺完成后通常要进行抛光处理,以达到1-3级的精度要求和较低的表面粗糙度。
陶瓷表面的裂纹类型随着不同的磨削工艺步骤而不同。在金刚石粗加工阶段,脆性破坏导致的裂纹为主要类型。实验观察到两种脆性损伤,一种是研磨工具夹持力导致的裂缝,另一种是陶瓷和磨料的相对运动产生的切向力引起了粘结相,进而导致晶体(磨粒)发生分离(剥落)。
在上述作用力的影响下,金刚石磨粒上会发生局部磨损,磨粒面会出现钝化或裂缝。粗加工之后,这些缺陷会保留在其表面。这些缺陷的数量取决于金刚石磨粒的属性、尺寸和形状等。清洁抛光工艺中使用小粒度的研磨工具,进而减少了脆性开裂;该阶段研磨影响和塑性变形为主要因素。陶瓷表面呈压扁状。在精整工艺中,利用小粒度的金刚石微粉和研磨膏进行加工处理,研磨影响为主要因素。工件表面精度为1-4级(Baharev B.P. 2009, Vakser D.B.. 1986)。
因此,利用磨削工艺对陶瓷工件进行机械加工是一个复杂的工艺,它取决于陶瓷材料的属性、磨削参数、抛光参数和其他因素等。本文则研究了VSH-75(HRC90-93)陶瓷试样的抛光加工;并将其硬度、热稳定性和耐磨性与硬质合金进行对比。VSH-75陶瓷的缺陷是强度低,脆性高。装配着VSH-75陶瓷片的设备器械可以在高达1200°Ñ的加工条件下保持其硬度不变。VSH-75陶瓷可用于无应力、高速高温条件下铸铁、钢部件、有色金属及其合金加工处理的清洁、半清洁抛光工艺。
材料及实验方法
精加工实验所用研磨机型号为Raster220,专业精加工各种机械零部件高精平面。这种桌式机床有三大部分构成:传送、冲压和带有变频器的控制面板。
磨料为电熔白刚玉、绿碳化硅和人造金刚石粉末。金刚石粒度为40-5μm,每个工序中都有其样品说明。利用过滤法将磨料均匀沉积在研磨平面上。
不考虑磨料自身的属性,所有实验中磨料的体积均设置为50cm3。该体积参数可以在直径为220mm的研磨表面形成单层磨料沉积层。 根据其体积与比重,计算求得每种微粉的重量:
• 绿碳化硅-160mg;
• 人造金刚石-175mg;
煤油(70%)、烯酸(25%)和石油(25%)混合液做实验的液相环境。将0.75-1cm3p体积的混合液滴在研磨表面上。
实验结果
在装配有轨迹扫描工具(Khanov A. M. 2010,Antsiferov V.N.. 2011,Nekrasov V.P. 2006, KhanovA..2010)的研磨机上对VSH-75(HRC90-95)材料制备而成的工件进行研磨加工。研磨工具材料为珠光体铸铁SCH28。所需表面粗糙度低于0.9μm.
磨料微粉的属性对研磨精加工的结果有着很大的影响,特别是对陶瓷等硬质材料的精加工。利用铸铁研磨工具,采用电熔白刚玉EB M400、绿碳化硅KZ M40和人造金刚石ASM40微粉磨料进行精加工的对比实验就证明了这一点。通过每隔4分钟计算材料去除总量可知:人造金刚石微粉ASM40的效率是EB M40和KZ M40效率的15-30倍(如图一a所示)。这是由于加工材料的硬度略低于微粉EB M40和KZ M40,而人造金刚石ASM40的硬度则明显高于陶瓷的硬度。工件表面粗糙度基本不受磨料类型影响,其变化在误差范围内(图一b)。
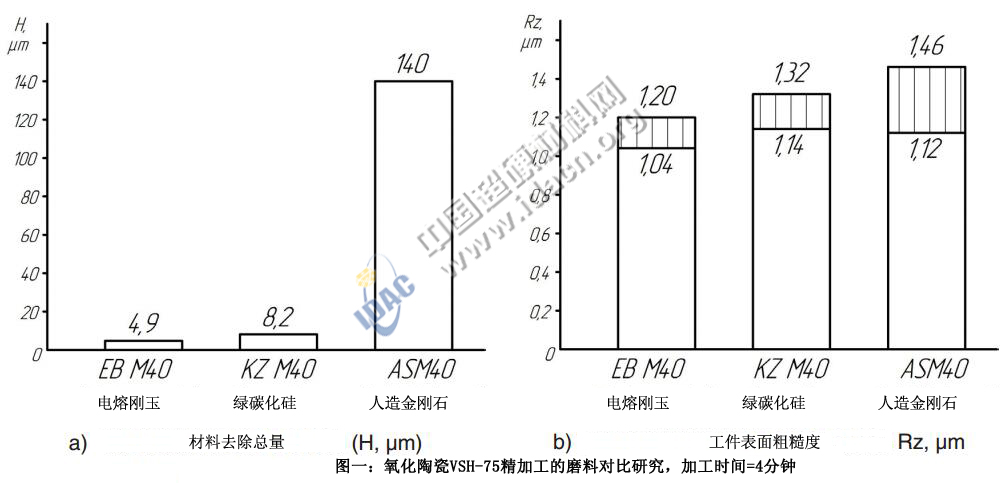
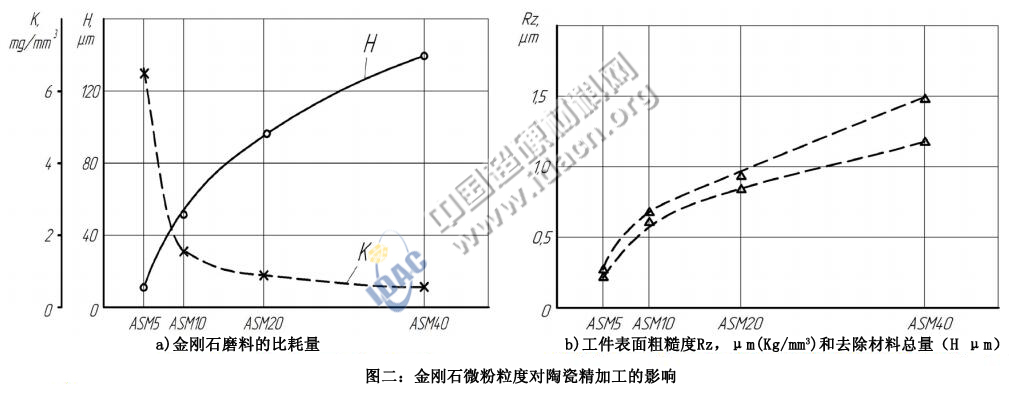
研磨表面的金刚石微粉量会影响精加工的性能、金刚石的单位消耗量K和加工效率H。在金属-陶瓷材料加工实验中,金刚石微粉ASM20的数量变化范围为50-175mg。
金刚石相对比耗量和材料去除总量随金刚石微粉量的增加而增加,如图三所示。
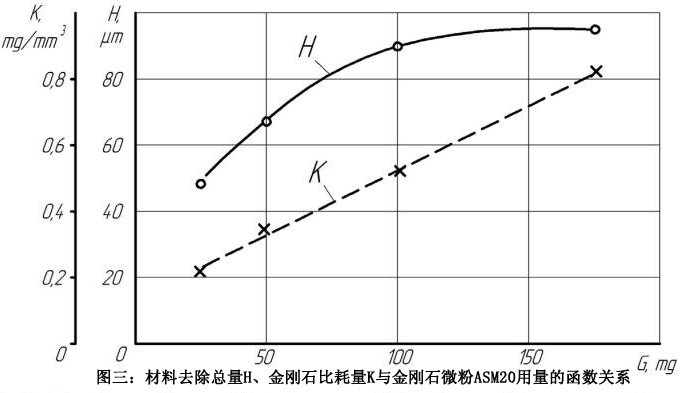
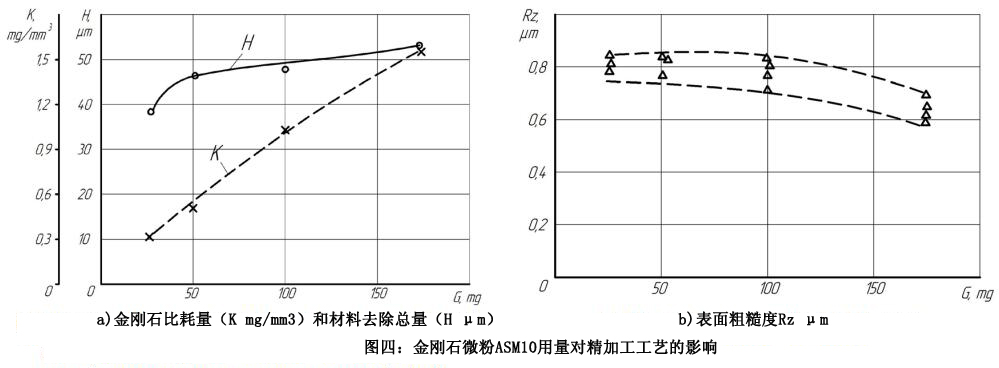
利用铸铁研磨工具CHS-28对金属-陶瓷工件进行精加工时,金刚石微粉ASM10和ASM20的最佳用量分别为20-45mg,40-80mg。
工件和研磨工具的接触压力通过金刚石磨粒得以传递。在25-150kPa压力范围内,利用ASM20磨料对陶瓷精加工过程中接触压力的影响研究表明:材料去除总量随着接触压力由25增大至50kPa而增大;当压力增至150kPa时,去除总量略有增加(图五a)。后者这种增加不甚明显的情况主要是由于高负荷下金刚石微粉磨粒的精炼所致。金刚石磨料的比耗量(k)随压力增大而降低,最为明显的降低发生在25-50kPa压力范围内(图五a)。
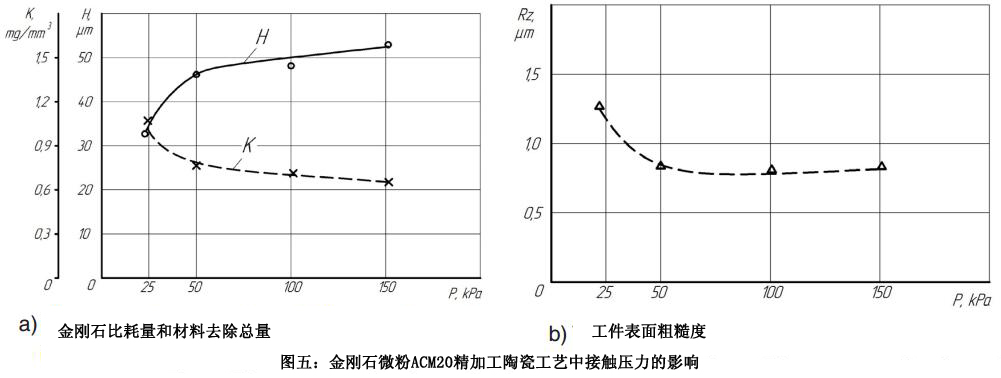
结论
人造金刚石微粉的粒度显著影响加工表面的粗糙度和精整效率。去除材料总量和表面粗糙度随粒度增大而增大。为满足Rz=0.9μm的要求和高效加工,推荐采用ASM20人造金刚石微粉。
研磨工具和工件的接触压力也会影响精加工。接触压力由25 kPa增至50 kPa时,材料去除总量显著增加,金刚石磨料的比耗量和工件表面粗糙度则降低。但随着接触压力进一步增大至150 kPa,接触压力的影响则不再明显。铸铁研磨工具CHS-28精加工陶瓷材料时的最佳接触压力为50-100kPa。(编译:中国超硬材料网)