摘要:砂轮轮毂的设计和制备材料决定了砂轮的动态、静态特性;这些砂轮特性反过来又影响着砂轮的磨削性能。在砂轮受超大离心力和磨削力影响的高效深磨削(EHDG)工艺中,这些特性尤为典型。另一方面,通过进程中即时检测和后处理测量的办法对砂轮的动态特性进行控制是优化磨削工艺较为适宜的一种策略。本文利用两种不同轮毂材料的CBN陶瓷结合剂砂轮进行实验并对结果进行对比,从而研究碳纤维增强复合材料(CFRP)轮毂基体对磨削工艺的影响。实验结果表明砂轮动态性能影响着材料去除机制并影响工件的表面粗糙度。此外,采用CFRP作为轮毂材料可以降低砂轮在加工过程中的径向膨胀和磨削力。使用钢材砂轮时的振幅和频率较高,而使用CFRP轮毂材料的砂轮则可以使振幅和频率衰减。
关键词:CFRP,HEDG,进程中检测,砂轮轮毂,动力特性
1、引言
HEDG工艺和缓进给磨削工艺只有在配置高性能磨床和配套砂轮以及适当润滑剂的条件下才能实现高效磨削。在HEDG工艺中砂轮上的负载力较大且离心力相当大,因此砂轮的动力特性在整个工艺中就尤为重要。此外,HEDG工艺中由于砂轮和工件的速度较高,砂轮会产生弹性形变;受接触刚度影响的弹性形变进而会影响材料去除机制并导致加工误差。砂轮的接触刚度定义为接触区上施以砂轮法向压缩力Fn和砂轮弹性形变δ之间的关系。接触刚度受磨削参数、砂轮规格等的影响。
砂轮的另一个显著特性是阻尼特性,该特性影响砂轮和工件在接触区的振动并影响工件表面粗糙度和波纹度。另一方面,系统的不稳定性会在切割深度上发生规则振动,从而使得磨削力在砂轮上引起不规则磨损。
HEDG工艺通常采用CBN或金刚石超硬磨料。超硬磨料砂轮有涂附了一层超硬磨料的轮毂基体构成。轮毂基体的设计和材料影响着砂轮的静态、动态特性。近年来,多种材料被用来制备超硬磨料砂轮的轮毂基体。轮毂基体材料的基本要求有:热传导系数高、机械强度高、振动阻尼性能好。常见材料主要有:铝、钢材、金属/非金属填料的人造树脂、陶瓷和聚合物等。
轮毂材料的选择取决于砂轮的加工区。高速高性能深磨削工艺则采用钢材和铝材等强度高的轮毂基体。采用无心轮毂基体并对其横截面施以恒定应力可以实现500m/s的圆周速度。本实验实际最大圆周速度为280m/s。由于钢材和铝材的弹性模量-密度比作为材料化学组份函数关系的差异很小,所以在给定旋转速度的条件下,张力基本都相同。
制备高性能砂轮的另一种材料是碳纤维增强复合材料(CFRP),CFRP材料的强度和刚度极高,强重比极大。实现钢材轮毂到CFRP轮毂的材料升级可以降低砂轮膨胀3倍。碳纤维(CF)含量较低的CFRP轮毂可用于砂轮低速加工,具有轻量的优势。由于密度低,材料重量可减轻90%左右,CFRP可以提供额外的阻尼。
轮毂材料特别是CFRP特性对磨削工艺的影响鲜有研究。Muckli利用有限元素法在305m/s的较高切削速度条件下研究铝材和钢材轮毂制备而成的砂轮性能。研究表明轮毂基体的几何形状和材料都会影响砂轮上陶瓷结合剂CBN层上的应力。研究还发现钢材轮毂基体容易出现轻微膨胀,但应力较高。
Warnecke等人对比了人造树脂-铝材复合物轮毂和硬性铝材轮毂的性能。结果表明软性人造树脂-铝材轮毂发生了显著形变,而硬性铝材轮毂则稳定。此外,磨削力和材料去除机制受砂轮轮毂弹性和切削速度的影响。
本研究采用CFRP和钢材作为CBN砂轮的轮毂材料,用于淬硬钢工件的高效深磨削加工,以此来研究CFRP轮毂材料是如何影响磨削工艺的。研究结果主要侧重于砂轮振动和形变,磨削力和磨削表面质量。
2、实验装置
2.1 测量系统
为研究分析轮毂材料对磨削工艺的影响,需要对加工过程中轮毂基体上的振动传播进行探测记录。
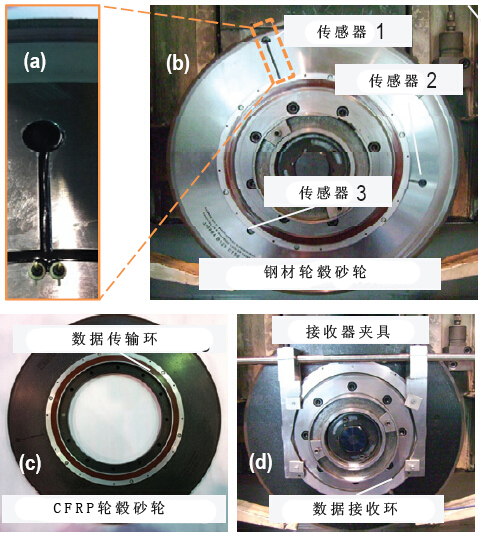
2.2 实验参数
表1为实验参数。表2为砂轮轮毂材料的机械性能。实验所用机床和相关设备如下:
机床工具:Elb 微切削AC8 CNC通用平面磨床;
表面粗糙度和轮廓仪:Hommel-Werke型T-8000;
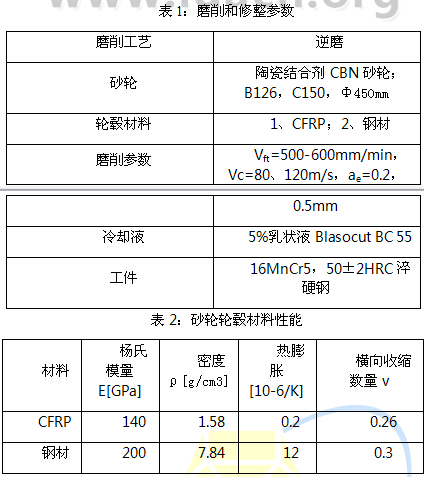
在HEDG工艺和缓进给磨削工艺中,切割深度会产生相当大的砂轮负载。这种现象主要发生在碎屑不能随冷却液完全清除掉时。在砂轮表面采用高压清理喷射可以防止砂轮发生负载,流速建议设置为0.3 lit/分钟,压力80 bar。这些措施主要取决于液体压力而非体积流量。它可以影响砂轮的动力特性。
鉴于此,在类似条件下对使用高压清理喷嘴的两种砂轮的动力特性进行该研究。实验结果表明高压清理喷嘴能够引起撒花轮振动,如图2所示。图中使用和未使用清理喷嘴得出的CFRP信号对比就证明了这一点。钢材轮毂砂轮的振幅明显比CFRP轮毂砂轮的振幅要大,利用CFRP轮毂材料就可以衰减砂轮的振动。
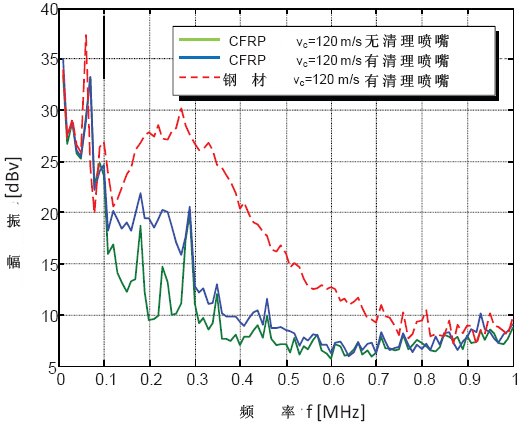
据图可知,CFRP较高的阻尼可以显著降低轮毂振幅;而宽频带钢材砂轮的振幅谱主要是由钢材较低的阻尼所致。
轮毂材料还影响砂轮的接触刚度以及离心力导致的砂轮径向膨胀。因此,砂轮接触区的集合形状会受到轮毂材料的影响;而通过以下试验则可以得到改善。首先,以恒定切割深度0.1mm、切割速度15m/s和进给速度50mm/min研磨出4个槽。选取槽1和槽4作为外槽基准,以此测量其他槽的深度。第二个槽以切割深度0.5mm、切割速度120m/s、进给速度500mm/min仅研磨一个周期。第三个槽按照第二个槽的参数来加工。然后在没有其他额外横向进给条件下对其研磨10个周期。第三个槽的深度可用来检测砂轮膨胀,第二个槽的深度用来计算砂轮的接触刚度。
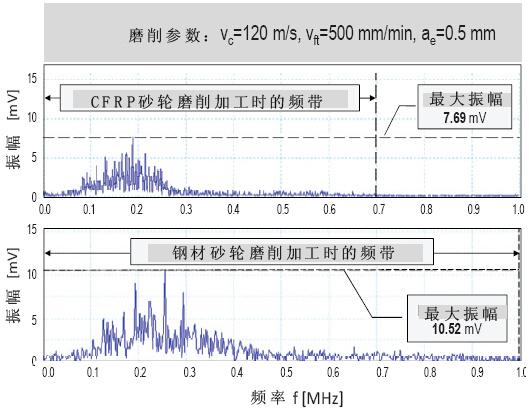