摘要:硬质材料像高合金化高速钢在磨削加工过程中出现的复杂热机械载荷,会影响表面完整性进而影响工程零件的性能。残留应力则是评估磨削零件性能的一个显著参数。早期研究指出磨削工艺通常就是工件的拉伸表面残余应力的来源。本研究中,通过x射线衍射对磨削工件的测量发现表面产生较大的压缩残余应力。为理解该残余应力的来源,实验建立了外圆精磨有限元素模拟模型,且温度取决于材料属性;并采用SYSWELD 2010软件根据二维数值模拟建立了热机械模拟。利用工件表面移动的等量热通量来模拟CBN砂轮对工件的加工作用。根据实验测量和分析计算求得热源轮廓。将砂轮的机械作用模拟为分布在接触区磨粒上的正常压力。求得温度分布和残余应力。模拟结果和测量结果之间的差别是比较明显的。进一步对磨削表面层进行表征,发现在给定的工艺参数、砂轮和材料属性条件下,等量载荷的热机械模型不足以在塑性变形和结构变化中再生诱导残余应力。
1、引言
高合金化高速钢(HSS)由于其碳化物和马氏体基体的硬度非常高而被当作耐磨材料,并应用在钢材轧制等强力苛刻加工工艺的成形工序中。在加工前对这类机械零件的表面完整性进行一个预测可以保障加工过程的安全性和产品的质量。表面完整性的主要指标有表面微结构和残余应力等。本论文主要对CBN砂轮对高速钢进行外圆精磨加工时所产生的残余应力进行研究分析。
有研究者指出残余应力轮廓主要受最后的制造加工影响,而制造工序也是影响最终表面完整性的主要因素。磨削作为一种精确加工工艺,适宜高硬度终极精磨材料的加工。对于光滑表面和精准公差要求高的零部件加工,磨削是其工艺的最后关键一步。但大多数加工操作中由于碎屑形成机制的缘故,很大一部分能量被转化为热能并在磨料-工件之间产生高温;最终导致以表面软化为形式的热损伤、残余应力和再硬化。
在磨削工序中,砂轮类型、材料硬度和工艺参数等因素都会影响零件的应力状态。在砂轮类型方面,Kohli等人研究发现传统刚玉砂轮加工时传递到工件上的磨削能总量约有60-75%被转化为磨削区的热能;而CBN砂轮的这一数据约20%;所以使用CBN砂轮能够降低热损伤。
为研究工件磨削过程中残余应力的来源及其形式,实验建立了FEA物理模拟。数值模拟需要对耦合现象的不同类型进行建模:热力的、机械的和冶金的。一些研究者提出了不同的建模,其中考虑了部分或所有的以上现象。在最为普遍的FE模型中,工件上的移动热源代表砂轮。因此,需要知道传导入工件的热通量密度。大多数温度模型都根据Jaeger理论求得磨削工件上的温度分布。但现有模型大多都忽略了砂轮的机械作用,在热源的结构影响方面有所局限。
本论文利用CBN砂轮对高速钢进行外圆磨削加工,从而研究残余应力分布及其变化。通过等量热源的耦合热机械FE模型求得模拟实验结果,将模拟结果与实验实测结果进行对比。对比差异主要表现为较高的压缩残余应力来源,特别是在低温和高热稳固材料(HSS)的条件下。然后,通过次表面微结构的详细分析做进一步的完善。
2、实验
2.1 实验磨削装置
本研究采用HERMLE CNC 5轴加工中心进行外圆外围纵向精磨加工;所用CBN砂轮直径Ds=150mm,宽度b=12mm;工件为硬钢柱,直径Dw=116mm、200mm,硬度为63HRC;设计定制特殊的喷嘴用于磨削区的油润滑。整个实验装置如图1所示。
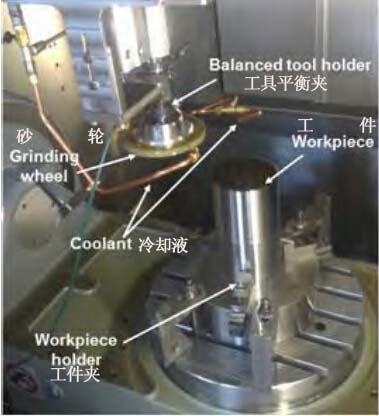
(详细内容请点击这里)