磨削、钻削、车削和钎削是原材料加工成精整产品过程中比较重要的几种机械加工工艺,通过对原材料形状和状态的改变加工成新的工件。对于脆硬、难加工材料以及对尺寸精度和表面光洁度有较高要求的工艺处理,则通常采用磨削加工工艺;磨削是一种材料去除率较高的精磨工艺处理,产品质量要求高、误差错误的成本代价也比较高。因此,选择适当的加工参数对于保证工件表面质量和提高生产效率就至关重要。
近年来不少学者对磨削工艺进行了研究。Walton利用物理气相沉积(PVD)镀附法采用CBN砂轮对低碳钢(51CrV4)工件进行加工并测得精准温度,实验发现高压磨削液对于镀覆层没有影响。Kwak利用反应曲面法(RSM)分析了SCM440钢在外圆磨削时的磨削力和表面粗糙度,结果发现通过将普通材料去除率添加到这些数学模型等值线图上,可以求得一些有用的磨削条件。Monici解释了优化切削液设备方法以此来提高加工效率并指出将油性切削研磨油同CBN砂轮结合起来要比刚玉砂轮的效率更高。Xu利用CBN砂轮对氮化硅进行磨削,结果发现能够获得较好的表面质量。Badger利用刚玉砂轮对表面磨削的磨削比和功率消耗进行检测以此来研究影响高速钢(HSS)可磨削性的因素。结果发现碳化钒的尺寸是影响HSS可磨削性的主要因素。Deepak pal利用田口参数优化方法研究磨削参数的优化以求得最小表面粗糙度,实验结果显示随着材料硬度的增加,表面粗糙度降低;磨料粒度从G46变化至G60,以及速度变大时,表面粗糙度也会降低。Manimaran利用刚玉砂轮在干、湿、低温冷却的条件下对AISI316不锈钢磨削进行研究,实验表明低温冷却条件下切削深度加大时,表面粗糙度增加;此时磨削力和磨削区温度也都有所增加。H.Aouici对AISI H11热作钢的硬车削进行研究,发现进给速度和切削深度对表面质量的影响不大。
实验
将H11热作钢板坯加热至1025℃,高温保温0.5小时,500℃热盐槽淬火冷却。最高温度450℃煅炼两次,高温保温2小时,最终硬度为45HRC。实验采用热作钢AISI H11主要是因为它硬度高、耐磨性好、韧性好、耐热冲击性好,广泛应用于硬模、热作锻造、挤压成形工艺、直升机旋翼桨叶和翼轴制造。H11化学组份如表1所示:

H11热作钢尺寸为304 mm × 110 mm × 24 mm,采用横向切割。切割深度为110mm,每次切割后用Mitutoyo SJ-201p表面粗糙度检测仪测量五次,求其平均值作为最后的表面粗糙度值。图一为实验用的表面粗糙度检测仪,图二为实验装置示意图。
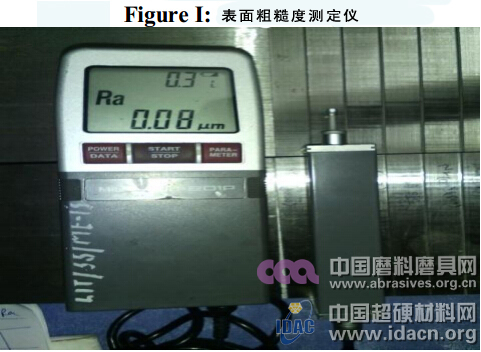
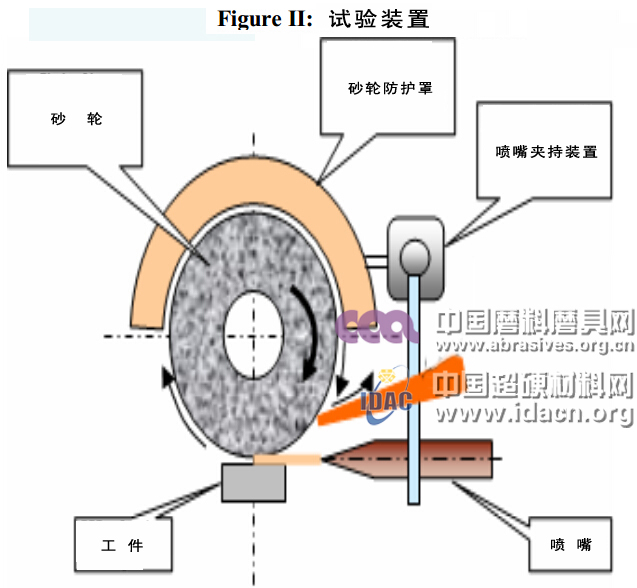
表二为平面磨床加工出的27组实验数据,由田口Taguchi L27 (34)正交阵列求得。
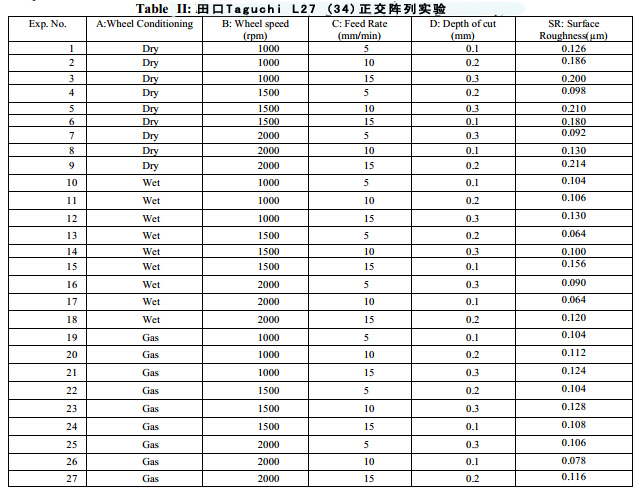
实验结果与讨论
表三和图三显示了对表面粗糙度的影响。信噪比越高,输入变量对输出参数的影响就越好。在湿加工条件下,进给速度5mm/min,切削深度为0.1mm,砂轮速度为2000rpm时表面粗糙度达到最优化。
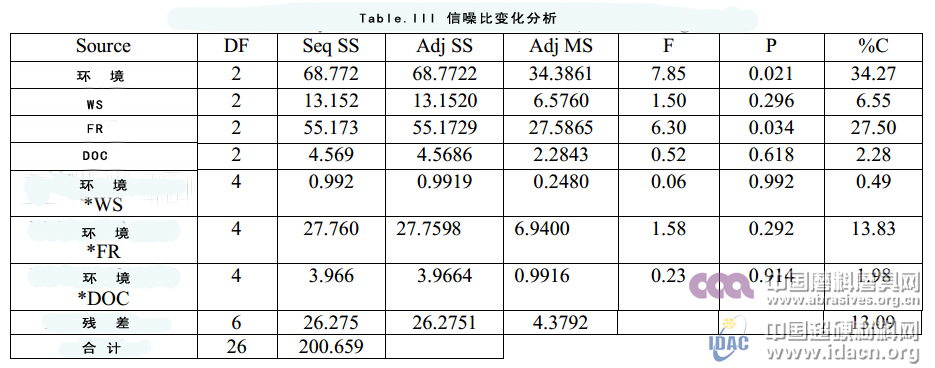
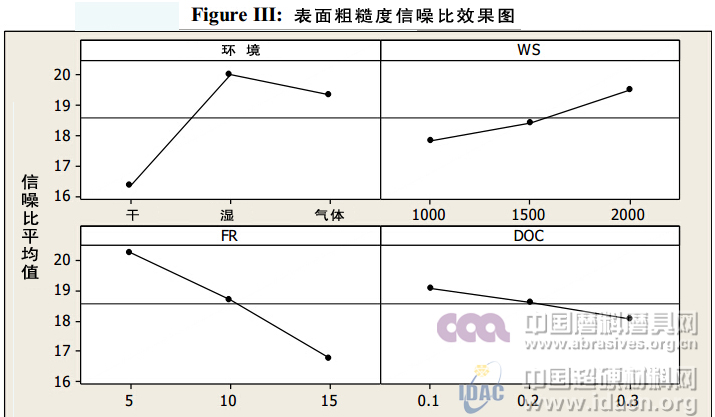
从表四可以看出,对AISI H11表面粗糙度影响最大的参数为砂轮加工环境,其次是进给速度(FR),接着是砂轮速度(WS)和切割深度(DOC)。图四为表面粗糙度的信噪比交互作用图,显示了加工环境(干、湿、气体)与砂轮速度、进给速度、切削深度的交互作用。
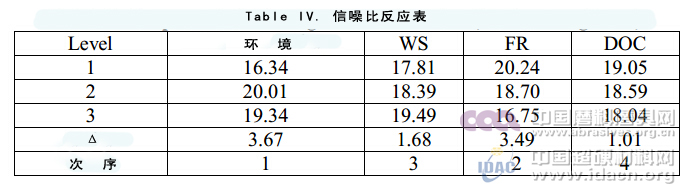
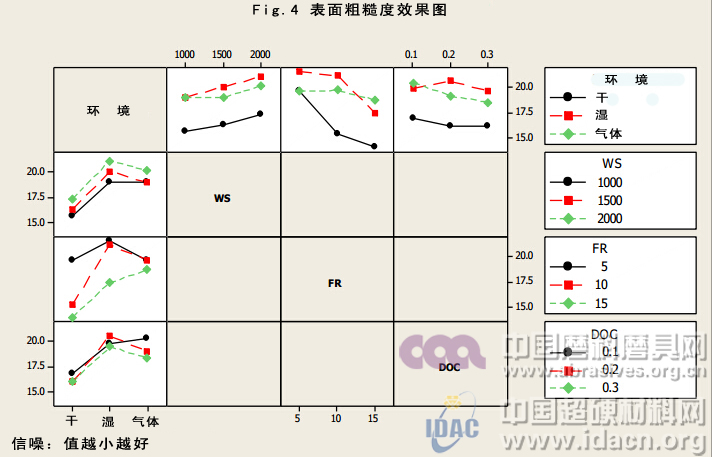
图五(a)显示,相比于干环境和压缩气体环境,湿冷却环境对较好的表面粗糙度有着更显著的影响;五(b)显示砂轮速度增加会改善工件的表面粗糙度;五(c)和五(d)显示随着进给速度和切削深度的增大,表面粗糙度也随着增大。同时还可以看出进给速度和切削深度的加大会导致磨削区温度升高,从而导致工件表面的灼烧并最终导致较大的表面粗糙度。
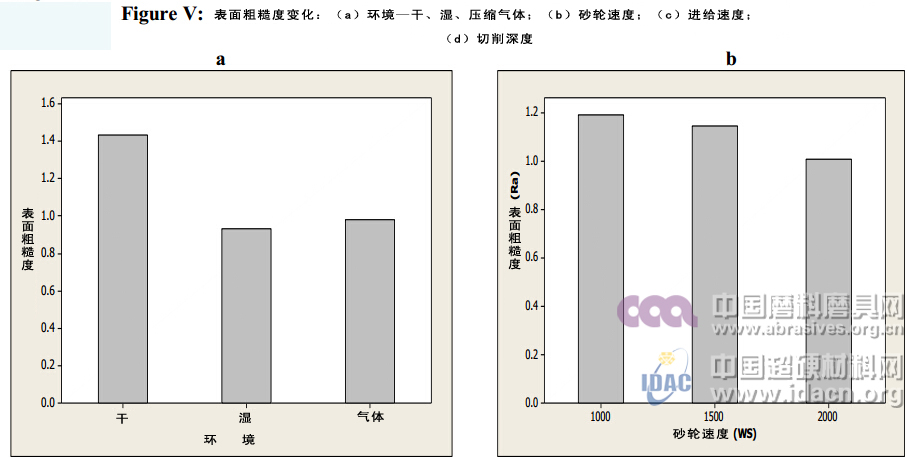
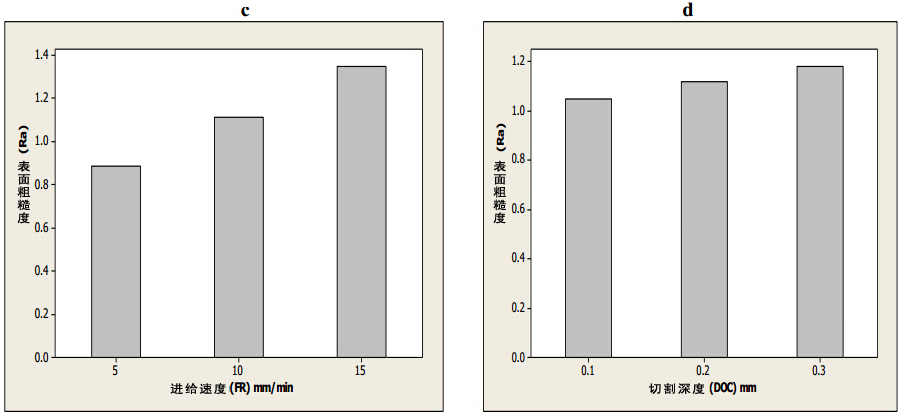
结论
1.湿加工条件要比干环境和压缩气体环境下更能够获得较好的表面粗糙度;
2.湿加工条件的有效性主要是由于冷却液提供了良好的润滑效果;
3.增大砂轮速度并减小进给速度和切削深度会获得较好的表面质量。