依据对磨削工况参数对砂带磨削性能测试结果影响的研究结论,我们尝试对制定砂带磨削性能试验新规程提出一些具体建议,分述于下:
4.1 关于恒进给磨削试验模式的讨论
恒压力磨削是涂附磨具行业过去普遍使用试验模式,这种模式广泛地被应用在许多场合,例如:材料的摩擦磨损测试、地板表面耐磨性测试、橡胶产品耐磨性测试等。本试验机采用伺服电机驱动滚珠丝杠的传动方式,不仅可做恒压力磨削试验,也为恒进给磨削试验创造了条件,为此在试车过程专门对恒进给磨削进行了探索,先后共进行了12次试验,其中:圆棒试件的恒进给试验11次,圆管试件1次。
在恒压力磨削过程中,压力是主控参数,试验机是依据压力传感器的测值来随时调整进给速度的快慢,以保持压力的波动处于设定值规定的范围内。从图4-1可见磨削压力基本是稳定的,而砂带的切除重量随磨削次数的增加呈逐渐下降的趋势。
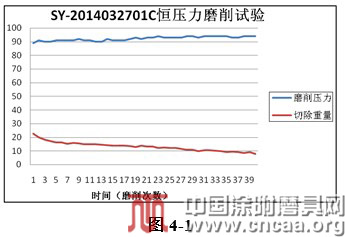
在恒进给磨削过程中,进给速度是主控参数,试验机始终保持进给速度的恒定,当试件的截面是一致时,也就实现了恒切除量磨削的效果。磨削压力在磨削过程只是测试值,不参与控制,但是可作为判断砂带失效的依据。图4-2是一次恒进给磨削的曲线图,从中可见其切除重量是保持恒定的,而磨削压力则随磨削次数的增加逐渐上升,到达某一点后磨削压力的上升迅速加快,说明砂带已磨钝,失去使用价值。
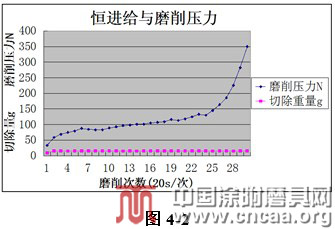
表4-1统计了B公司X产品在一个月内先后做的9次恒进给磨削试验的有关数据,表中“切除重量均值”一栏是该试验编号内所有单次切除重量的平均值;“切除量相对差”是该试验编号内所有单次切除重量标准差与平均值的相对偏差。
统计表明:
1,恒进给磨削过程单次切除量的波动非常小,切除量的相对差基本控制在0.3%以下,足见磨削进行的很稳定。
2,切除重量均值的波动也小,以6mm/min的进给速度为例,尽管两次试验间隔一个月,但是切除重量的均值仅差0.01g;再看8mm/min的进给速度,尽管7次试验间隔也是一个月,但是切除重量均值的极差也只是0.2g,7次试验的相对标准差仅为0.6%;说明恒进给磨削试验的再现性也好。
3, 速度设定值和切除重量的关联性好,8 mm/min比6 mm/min快了33%,切除重量同样增加了33%;10mm/min时的比值则为67%。
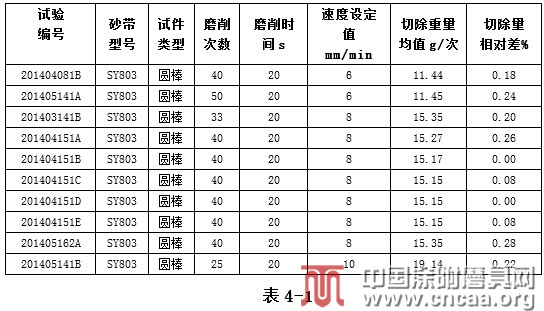
我们选择了三次不同进给速度下的恒进给磨削试验数据,试验条件列于表4-2,试验结果列于表4-3。
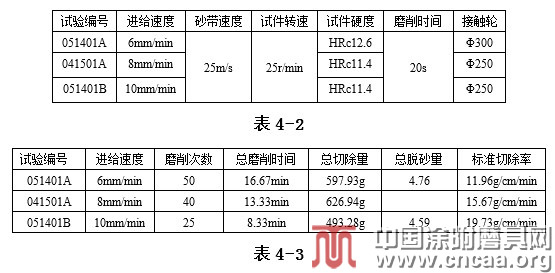
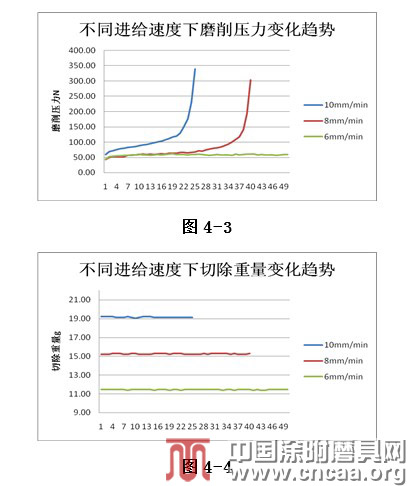
从图4-4中不难发现,在恒进给磨削试验过程中,随着进给速度的提高,单次磨削的金属切除量亦相应增加;从图4-3中可见,随着磨削次数(即磨削时间)的增长,压力随之增长,开始阶段增长相对缓慢,但达到一定时间后,会迅速增加,直至砂带磨削寿命终止,其中进给速度高的,磨削压力出现迅速上升拐点的时间也早。
对于B公司X产品,采用10mm/min的进给速度,磨了仅8.3min砂带的磨削能力就已消耗殆尽;而采用6mm/min的进给速度,磨了16.7min后,压力仍保持不变,表明还有很大的磨削潜力,真像是个跑“马拉松”的选手,具有很强的耐久力。
恒进给磨削试验模式虽然使用次数还不够多,不过我们已感觉其特点突出,试验数据非常稳定,判断砂带失效的标志明显,也非常适应对砂带磨削加工节拍有要求的砂带性能测试需要,应该是值得推荐应用的一种试验模式。
4.2 关于圆管试件的讨论
以圆形钢管作为砂带磨削试验的试件早在1987年从德国进口的砂带磨削试验机上就开始应用,但是在以后并未得到广泛应用,业内主要采用的是圆棒形试件。可能与下列两个原因有关:一是钢管的费用要比棒料高;二是钢管试件比钢棒试件重,使每次磨削后为称重装卸试件的劳动强度加大。
由于圆管试件具有独有的特点,因此本试验机在设计时考虑了两种试件的应用可能。为此我们也对圆管试件的磨削进行了一定尝试。试验中采用的圆筒试件材质为45#钢,规格为φ120/100×150mm。先后做了4次圆管的恒压力磨削试验和1次圆管的恒进给磨削试验。表4-4是采取恒压力磨削的试验条件;表4-5为圆管恒压力试验结果;图4-5为圆管恒压力磨削切除重量的变化趋势。
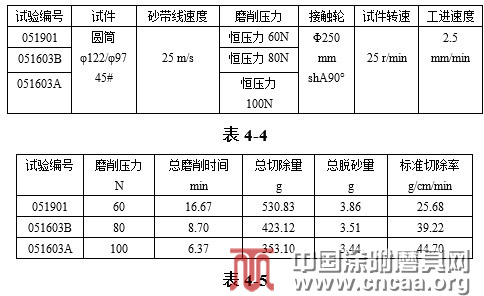
1、圆筒磨削与圆棒磨削相似,磨削过程砂带磨削性能的表现也呈现初始期、稳定期和下降期三个阶段;在初始期和稳定期磨削压力高,切除能力也高,从表4-5中的标准切除率对比可见一斑。
2、磨削压力高的下降期出现较早;特别是在100N和80N两次试验中均出现因瞬间压力超过保护设限而自动退出磨削,未能完成预定磨削次数的情况,100N发生在第21次,80N发生在第27次,唯有60N完成了全部磨削试验。所以60N的标准切除率虽然最低,但其总切除量却最多。这提示我们应注意圆管磨削时砂带与试件接触的宽度只有1cm左右,而圆棒为3cm,因此单位宽度上的磨削压力远比同样压力下的圆棒磨削为大;在本次试车中圆棒恒压力磨削所施加的最大压力为150N,也就相当于50N/cm的线压力。
3、圆管恒压力磨削过程压力波动情况要比圆棒为大,分析认为一是热轧钢管的壁厚均匀度较差,国家标准对普通钢管壁厚的公差范围规定是+15% / -12.5%,可见是产生沿圆周磨削过程引起压力波动的原因之一,为此今后圆管必须加工内外圆后才能进行磨削试验;二是要设计专门适用于圆管磨削的压力控制程序,如今使用圆棒磨削的压力控制程序来磨圆管是不合适的。
4、圆管磨削过程,试件温升很小,基本不需施加冷却,这与圆管磨削时试件表面自行冷却条件良好有关,也是相对于圆棒磨削的突出特点之一。
5、由于圆管试件单位长度上的质量要大出圆棒数倍,因此试验过程可减少更换和重装试件的次数,使操作简便了不少,也减少了因重装试件而产生的切除重量计算误差。
6、 对本试验所使用的B公司X产品而言,圆管磨削合适的磨削压力是60N。
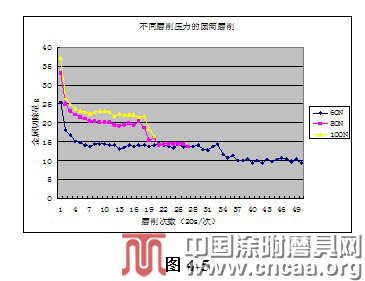
我们还进行过一次圆管的恒进给磨削试验,见图4-6。圆管与圆棒一样在恒进给磨削试验中非常平稳,单次切除重量始终保持在14.22g左右,25次磨削中单次切除重量波动的相对标准差为1.16%;总切除重量为380.67g;标准切除率高达36.84g/cm/min。在磨削过程中磨削压力上升比较平缓,未见明显拐点出现。由此又一次使我们看到恒进给磨削试验模式的优点。
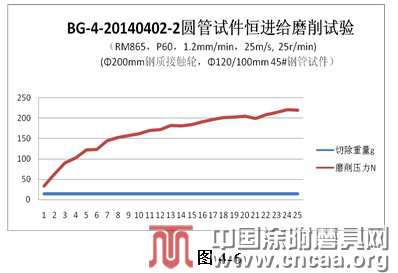
由于试验机试车时间不长,砂带试样的品种还仅仅限于普通磨料的。
对于砂带磨削性能检测新规程的试验工况参数,我们提出了圆棒试件恒压力与恒进给磨削的两种方案建议,见表4-6和表4-7。恒压力模式基本延续了行业内各企业目前较多采用的试验方式,其磨削状态比较切合砂带手工打磨时的情况,因为人工打磨时对磨削进给量的控制比较困难,但是通过手感来调节磨削压力大小,还是有一定可能的;而恒进给模式更切合机械式砂带磨削的情况,特别是最近正处于发展期的机器人砂带磨削需要,因为通过机械来控制磨削进给量是非常容易实现的,而对磨削压力的控制通常是根据磨削电流值的大小来间接反映;再说生产线的流水作业对加工节拍是有要求的,也就意味砂带的磨削性能应达到一定切除率的要求,所以我们更倾向于在砂带磨削性能测试中采用恒进给模式。
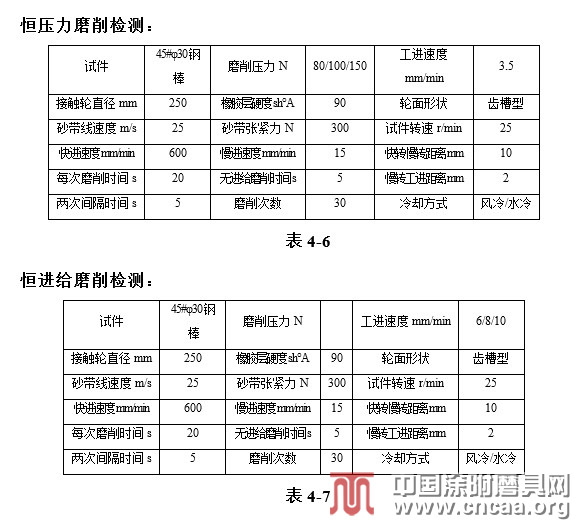
以上对试验工况参数的建议只是初步的想法,而且主要针对有切除能力要求的粗粒度砂带测试需要,实际上砂带的使用范围很广,制定新规程应考虑的问题很多,我们在此仅是为了抛砖引玉,期望行业内大家来提出建议,使新规程能起到全面的指导作用。
4.4 其他有关规程制定问题的讨论
4.4.1 关于在新规程中推荐使用圆管试件的想法
鉴于圆管试件在试车过程显现的许多特点是很诱人的,我们很想将其列为首选试件,但是上一阶段所做试验次数终究有限,说服力还不够充分,再说试验的成本因素也需考虑,所以还是需要斟酌。在表4-8和表4-9中只是对圆管试件的恒压力和恒进给试验提一个参考意见。
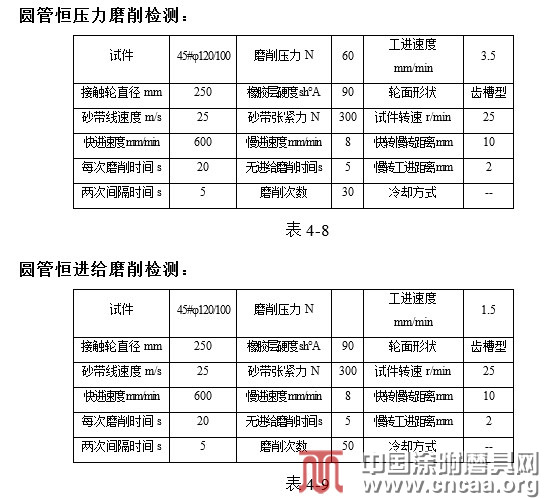
圆管恒压力磨削检测:
4.4.2 关于在新规程中对试件材质提出严格要求的想法
目前在砂带磨削性能测试中所使用的试件材质多数为45#优质碳素钢、S304(0Cr18Ni9)不锈钢和TC4(Ti-6Al-4V)钛合金钢。然而当前市场供应存在不规范的情况相当普遍,要想采购到合乎标准的材料十分困难,试车中就遇到很多问题。试件作为考核砂带性能的对照物,材质符合标准是必要条件,否则试验结果就缺乏公信力。所以在制定新规程时建议对试件材质作出严格要求,应确定试件的定点供应单位,以保证试件的一致性。
4.4.3 在新规程中应对试验机有关工况参数的示值误差作出限定
试验机是砂带磨削性能测试系统组成中的重要环节,每一项工况参数的测试误差都会影响到测试结果的准确度和离散性。这里的误差有两层含义,一是指工况参数示值相对检定用标准器件示值的偏差,即通常所说的“示值误差”;另一是指工况参数的示值相对该参数设定值的偏差,是反映控制是否精确的量值,可以称其为“控制误差”。对一些重要的工况参数都必须在规程中根据其重要程度,分别明确规定这两种误差的允差,例如:砂带线速度、磨削压力、进给速度、砂带延伸率、主电机电流、切除长度和接触轮橡胶层硬度等。
4.4.4 如何评价砂带磨削性能的优劣?
如今在评价砂带锋利性时,多用“标准切除率”这个参数,即总切除重量g / 磨削时砂带与试件接触区的宽度cm / 磨削时间累计值min。是否合理?值得讨论。在试车中就感觉砂带周长的长短会影响总切除重量的多少,而在“标准切除率”这个参数中是无法反映周长的影响。再说磨削时间累计值的取值方法也有讲究,会影响“标准切除率”这个参数的大小,如果取的磨削次数很多,在后阶段砂带已处于钝化阶段,这时的切除能力很低,计算下来,总切除量虽有增加,可是“标准切除率”却不高,会比磨削次数较少时的计算结果差很多,因为后者是在砂带锋利期采集的切除量数值。因此经常会出现“标准切除率”高,而总切除重量低,和“标准切除率”低,而总切除重量高的矛盾情况,到底应如何评价这两种砂带的优劣呢?是否将按单位宽度砂带改为按单位面积更合理些,或者是否还有更合理的评价方法?盼望大家讨论。
4.5对试验机下步改进的建议
根据在试车中的感受,对试验机需作改进的地方提出如下建议。
4.5.1建议增加测温系统
砂带磨削过程必然会产生切削热,由此引起被磨工件的温度提高,严重时将造成工件表面的灼伤;因此非常有必要在磨削试验过程中对被磨试件温度的变化进行监控,使其不超过200°C。目前试车时是采用手持式红外测温仪在每次磨削后对试件进行测温,比较麻烦,所以建议在试验机上增设在线式红外测温头,随时监测试件温度,当超过一定限度后发出报警讯号。
4.5.2建议改进吸尘口的设计
目前的吸尘口非常容易产生切屑的堆积,主要是因为磨削产生的高温铁屑受到吸尘口的阻挡,逐渐堆积并产生熔融态的金属块状物,严重时会堆高到接近砂带表面,造成安全隐患。
所以建议改进设计,使铁屑无从堆积。另外目前吸尘风量过大,既引起很大噪声,又不利节约能源,也应是吸尘口改进设计中需考虑的问题。
4.5.3建议在砂带磨削记录表中增加更多的工况参数实测记录
从现在的记录表中可查阅的工况参数实测值不多,只有磨削压力、切除体积、切除重量、磨削能力和砂带延伸率等几项,当然通过趋势图可看到更多的磨削试验情况,但是一是只能上机查看,脱机状态就无法了解实际的磨削工况值;二是趋势图一般只保存一个月,这主要是受计算机存储空间的限制。所以适当在纸质文件上记录更多的工况值是很有必要的。希望能增加的参数值有:砂带线速度、砂带电机电流、砂带张紧力、砂带打滑率、试件转速和进给速度等6项。
结语
通过以上试验与研究表明:SDSY-50B数控砂带磨削性能试验机是一台高性能的数控砂带磨削试验机,自动化程度高,减少了人工干预的误差,提高了磨削性能检测的精准度,在行业内可针对各企业涂附磨具产品做定向性能的检测和使用性能的开发,对涂附磨具产品的开发和研制,将起到巨大的推动作用。同时它为涂附磨具产品的数字化提供了条件,为涂附磨具产业转型升级,向先进制造业迈进提供了着力点。因此,有必要继续研究和开发试验机的性能与应用,使它更好地为产业服务。