(1-中国磨料磨具进出口公司 2-中国磨料磨具网 3-中国超硬材料网 )
关键词: CBN 金刚石 低熔陶瓷结合剂 磨具 计算机程序
超硬磨料低熔陶瓷结合剂磨具配方设计程序,可以给出CBN和金刚石两大类超硬磨料和不同硬度、不同填料的陶瓷结合剂磨具配方,同时提供一个常用的数据库,给出了数十个低熔陶瓷结合剂的参考配比和不同配比的结合剂耐火度预测以及制品的烧成参考曲线(低熔陶瓷结合剂的参考配比和烧成参考曲线主要来源于早期《金刚石与磨料磨具工程》的文献中)。
一、常用原材料简介
CBN和金刚石用的陶瓷结合剂耐火度都比较低,CBN用的陶瓷结合剂的耐火度约800-900℃,人造金刚石用的陶瓷结合剂耐火度约在600-700℃,相对于刚玉、碳化硅磨料的陶瓷结合剂耐火度大多在1000℃以上而称低熔陶瓷结合剂。制造陶瓷结合剂CBN和金刚石磨具所使用的600-900℃的低熔、低热膨胀系数玻璃质结合剂可以用矿物原料,也可以用化工原料,或者矿物原料和化工原料混合使用而配制,现将常用的原材料大致分述如下:
1、粘土:主要成分为高岭土,高岭土向结合剂中引入SiO2 和Al2O3的成分,SiO2在结合剂中形成“基体”,Al2O3可提高结合剂的热稳定性、化学稳定性和强度,但过多引入Al2O3将提高结合剂的耐火度。
2、长石:结合剂中使用的长石主要是钾长石和鈉长石,用以引入K2O、Na2O、Al2O3、SiO2等成分,钾长石的分子式K2O·Al2O3·6SiO2 ,分子量556.5,但钾长石中一般都掺有一定量的钠长石;钾长石的化学成分要求:SiO2 62-66% ; Al2O318-22.5% ; K2O>10% ; Na2O<4%
3、石英:白色或乳白色块状,化学成分为SiO2,分子量60.10,比重2.23-2.65之间。SiO2含量要求SiO2>98%。由石英引入SiO2调整结合剂成分,以满足结合剂化学成分与性能的要求。
4、滑石:滑石的基本成分是含水硅酸镁,比重2.7~2.8,矿物实验式为:3MgO·4SiO2·H2O,理论组成:MgO 31.7%;SiO2 63.5%;H2O 4.8%。
结合剂中加入滑石引入MgO和SiO2,滑石在结合剂中的使用要求:SiO2 55-63%,MgO 26-33%。滑石可以提高结合剂的机械强度,增加结合剂脆性。
5、萤石:萤石化学式 CaF2 ,分子量78.1,比重3.01-3.25,理论组成:Ca 51.3%,F 48.7%。
结合剂中加入萤石,引入氟化钙,对结合剂有催熔作用,可以提高结合剂机械强度,使用的萤石要求:Ca 46-51%,F 44.5-48.5%。
6、冰晶石:冰晶石是一种天然结晶矿物,化学名称氟铝酸钠,分子式Na3AIF6,分子量210,比重2.99。
冰晶石的引入会显著降低结合剂的耐火度,但也会使结合剂的热稳定性和弹性有所降低。工业用冰晶石要求主成分含量Na3AIF6>96%。
以上是结合剂常用的矿物成分,在低熔结合剂中经常还要补充一些化工原料,常用的有十余种。
7、硼砂:结晶硼砂是一种白色颗粒,分子式Na2B4O7·10H2O,分子量381.24,比重1.69-1.72;400℃左右脱水,878℃熔融。硼砂在结合剂中引入B2O3和Na2O;B2O3能提高结合剂的弹性和化学稳定性,与SiO2、 Al2O3 等混熔形成低共熔物,降低结合剂耐火度。在结合剂中B2O3的加入量以20%左右为宜。
硼砂与长石以50:50左右混合,在900℃以上熔融,冷却、粉碎、过筛成粉状,称硼砂玻璃,简称硼玻璃,这也是一种常用的含硼材料。也有混入其他材料制成硼铅玻璃和硼硅玻璃使用的。
8、硼酸:在结合剂中引入B2O3但不希望过多地引入Na2O时,可以使用硼酸引入B2O3,硼酸分子式H3BO3,分子量61.8,含有B2O3 56%,比重1.435。工业硼酸要求H3BO3>98.5%。
9、氧化锌:白色粉末,分子式ZnO,分子量81.4,比重5.6,工业品要求ZnO>98%。ZnO在结合剂中是较好的助熔剂,能提高制品的热稳定性。
10、硝酸钾:分子式KNO3,分子量101,K2O含量46.6%,比重2.1,850℃分解出K2O,K2O能显著降低结合剂耐火度,降低结合剂表面张力。使用KNO3引入K2O时因KNO3分解时放出氧,所以还有氧化剂的作用。工业用硝酸钾要求含量KNO3>98%。
11、碳酸钠:白色粉末,分子式Na2CO3,分子量106,熔点852℃,Na2O含量58.5%;碳酸钠放置空气中易吸潮结块。Na2O能减少制品的烧成范围,在结合剂中的作用与K2O接近。
12、碳酸钡:分子式BaCO3,分子量197.3,比重4.43,高温时能分解出BaO,BaO含量77.7%,BaO在结合剂中能部分代替PbO和B2O3的作用,其热稳定性优于PbO,且能降低结合剂耐火度,提高结合剂强度。BaO在结合剂中的用量在6-15%之间。
13、碳酸锂:白色粉末,分子式Li2CO3,分子量73.88,比重2.11,熔点618℃,含Li2O 40.44%。Li2O能提高结合剂抗冲击强度。工业用碳酸锂要求Li2CO3>98%。
14、钛白粉:分子式TiO2,分子量79.9,比重在4左右,TiO2能提高结合剂的物理化学性能,因其耐火度较高,用量不可过大,约3% 左右为宜。工业钛白粉要求TiO2>98.5%。
15、氧化铜:黑色粉末,分子式CuO,分子量79.5,比重6.4,CuO能降低结合剂耐火度并有着色作用。工业品要求CuO>98%。
16、氧化铁:赤红色粉末,分子式Fe2O3,分子量159.7,比重5.0-5.25。Fe2O3能降低结合剂耐火度,提高结合剂韧性,工业品称铁红,要求Fe2O3>98%。
除以上介绍的十几种原材料外,有的结合剂中还引入P2O5、Co2O3、Cr2O3、ZrO2、SnO2以及放射性元素的氧化物CeO2等,可以根据具体需要加入各种成分研制结合剂。目前我国各超硬材料企业使用的低熔陶瓷结合剂主要是以化工原料配制而成,但我国传统的玻璃和陶瓷企业使用的低熔玻璃则主要是以矿物原料配制而成,如果用矿物原料配制超硬磨具的低熔陶瓷结合剂会有什么结果也不妨一试。
二、CBN和金刚石浓度的换算
CBN和金刚石的浓度是一个状态标识,在实验中需以质量形式具体操作,程序提供了CBN和金刚石的浓度与质量的换算值。
三、低熔陶瓷结合剂常用物质的分子量
通常在一些文献中看到的结合剂配比有些是克分子比,但在生产和实验操作中需要以质量形式加入,所以具体操作时克分子比需按分子量换算成质量比,表1给出了一些常用氧化物的分子量,以便于应用。
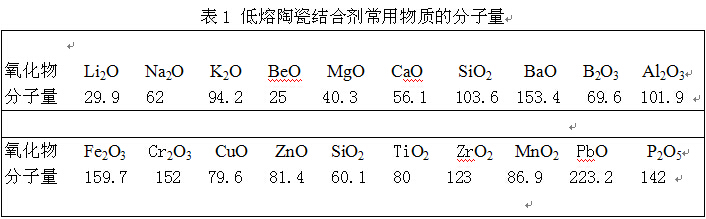
在这一段程序中自550℃~890℃之间有20多组不同的结合剂组成,选出一指定温度则可由程序给出一组参考组成;但因原资料出自不同作者之手,对温度的取值不同,所以误差较大,使用者应予注意。(资料主要来源于《金刚石与磨料磨具工程》)
适用于这一部分结合剂的主要成分:
Li2O ,Na2O ,K2O ,MgO ,CaO ,ZnO ,SrO2 ,B2O3 ,Al2O3 ,SiO2
五、《Na、K、Mg、Ca、B、Al、Si》系统低熔陶瓷结合剂基础玻璃的耐火度的预测
本程序可以预测 Na ,K ,Mg ,Ca ,B ,Al ,Si ,系统的基础玻璃600~900℃左右的耐火度。实验中也可在此基础玻璃中加入其他成分或调整含量以寻求自己所需要的结合剂组成。
(一)预测方程:
Y = 43.1799×X1 -153.446×X 2 +58.9785×X3
(二)必要条件:
Y = 耐火度
1 ≤ X1 = Al2O3 ≤18
6.5 ≤ X 2 = R 2 O ≤16.5
9 ≤ X 3 = R O ≤13
11 ≤ X 4 = R 2 O3 ≤ 37
33 ≤ X5 = R O2 ≤56
99.95 ≤ X1 +X 2 + X3 + X 4 + X5 ≤100.05
六、CBN和金刚石陶瓷结合剂磨具的配方设计
前苏联 瓦西里耶夫 提出了一个关于磨具中各参数之间的关系式(式2),
R = π d2 /1.73 ×(n×Vс×/Vз)0.5 ×б (2)
R-把持每个磨粒的力
d-磨料颗粒直径
n-每个磨料颗粒上的结合剂桥的个数
Vс-结合剂含量
Vз-磨料含量
б-结合剂强度
日本人 佐田登志夫提出用大樾氏硬度计测量磨具硬度时有如下关系式
OB = 17 ×G-0.66 ×(0.89)Z (3)
OB-测量坑深
G-粒度
Z-硬度序数
以上两个公式是我们分析磨具配方数据的主要参考,结合我们的实际研究编制了本配方设计程序。前苏联和日本的超硬磨具硬度分级基本是一至的,分为软、中软、中、中硬、硬、共五级,我国现还没有制定超硬磨具的硬度标准,参照苏、日的分级目前我国超硬磨具的硬度在此也可分为五级,作为“抛砖引玉”,供制定硬度标准时参考。
(1)硬度代号,见表2
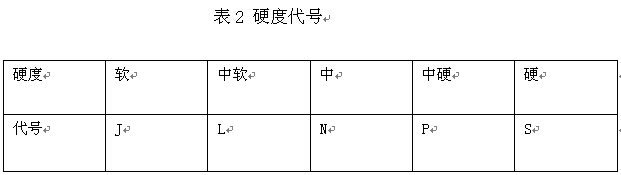
(2)浓度:浓度我们取可能的常用范围由50%~175%;表3

(3)粒度:
本程序设计的粒度取值范围是60/70~325/400;取填料粒度比超硬磨料细1~2级,以突出超硬磨料的作用,但也不能过细,过细起不到填料应有的作用,选定磨料粒度后填料的默认值见 表4。
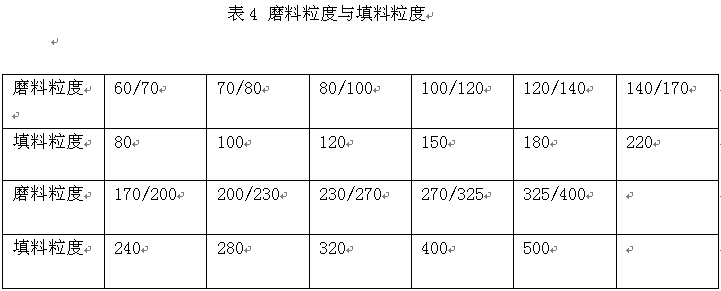
(4)CBN和金刚石陶瓷结合剂磨具配方表格式,见表5
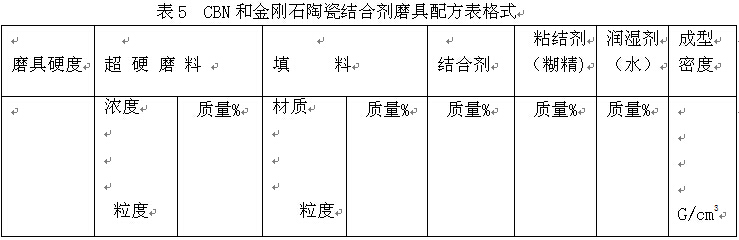
在操作中按表5的要求给出需要的材质、粒度、浓度、硬度即可由程序给出配方,其中填料CBN默认为白刚玉,金刚石默认为碳化硅,粘结剂和润湿剂默认为糊精和水;如不用默认值可自行确定填入亦可。
(5)CBN和金刚石陶瓷结合剂磨具配方计算举例,(见表6)
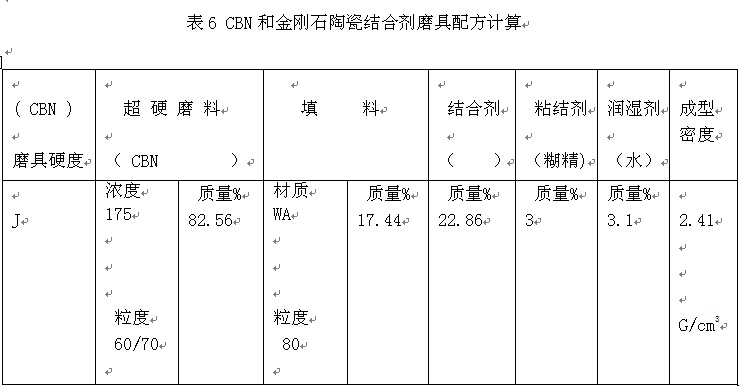
七、CBN和金刚石陶瓷结合剂磨具的配料计算
(1)按指定的金刚石陶瓷结合剂磨具配方表,程序可进行配料计算
(2)如选定表6的数据计算,设:模具体积=10; 片数=20; 当给出模具体积和片数后程序给出以下配料数据,
(3)成型单重 = 2.41×10=24.1
(4)混料量 = 成型单重×片数×(1+混料余量)
(混料余量数值可选)
(5)超硬磨料量 = 324.00
(6)填料量 = 68.44
(7)结合剂量 = 89.71
(8)粘结剂量 = 11.77
(9)润湿剂量 = 12.17
后记:
本文主要参考文献为《金刚石与磨料磨具工程》,但现已无法列出详细的参考文献目录,特向原作者和读者致以深切的歉意!