申请人:南昌大学
发明人:段端志 章少剑 赖志慧 许文虎 张海涛 吴斌
摘要: 本发明公开了一种基于自蔓延反应快速制备致密超硬磨具与钻具的方法,所述超硬磨具与钻具的外径为4–100mm,所述超硬磨具与钻具的结构分为工作层和基体两个部分,所述工作层组分包括金属结合剂和超硬磨料,所述金属结合剂包括Al、Ti、Cu、Fe、Sn、Ni、Co。所述基于自蔓延反应的致密超硬磨具与钻具的快速制备方法包括混料、压制成型、通过感应加热基体和石墨模的方式引发自蔓延反应并在反应刚完成时施以高压等步骤。本发明致密超硬磨具与钻具的胎体结合剂与金刚石界面结合强度高,金刚石力学性能损失小,胎体致密度高,具有加工效率高、耐磨性能好、使用寿命长等优点。
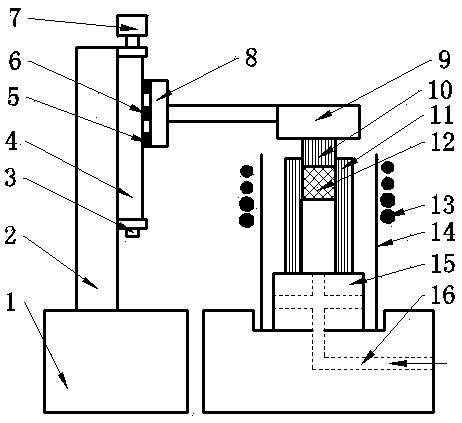
2.根据权利要求1中所述基于自蔓延反应的致密超硬磨具与钻具,其特征在于,所述金属结合剂中Al和Ti的质量比例为0.5:1–2:1,且Al和Ti的总重量份数为15–45份,Ni/Co/(Ni+Co)粉重量份数为0–10份,Sn粉重量份数为2–6份,Cu粉重量份数为20–70份,Fe粉重量份数为0–30份,且Cu粉和Fe粉的总质量份数为50–70份,所述超硬磨料为金刚石或立方氮化硼,浓度为30–140%,粒度为25/30–230/270目。
3.根据权利要求1中所述基于自蔓延反应的致密超硬磨具与钻具,其特征在于,所述金属结合剂中Al和Ti的质量比例为0.9:1–1.6:1,且Al和Ti的总重量份数为25–35份,Ni/Co/(Ni+Co)粉重量份数为2–8份,Sn粉重量份数为3–5份,Cu粉重量份数为30–50份,Fe粉重量份数为20–10份,且Cu粉和Fe粉的总质量份数为55–65份,所述超硬磨料为金刚石或立方氮化硼,浓度为60–110%,粒度为50/60–120/140目。
4.根据权利要求1中所述基于自蔓延反应的致密超硬磨具与钻具,其特征在于,所述金属结合剂中Al和Ti的质量比例为1.3:1,且Al和Ti的总重量份数为30份,Ni/Co/(Ni+Co)粉重量份数为5份,Sn粉重量份数为5份,Cu粉重量份数为40份,Fe粉重量份数为20份,所述超硬磨料为金刚石或立方氮化硼,浓度为85%,粒度为80/100目。
5.根据权利要求1–4所述基于自蔓延反应的致密超硬磨具与钻具,其特征在于,所述Ti粉、Ni粉、Fe粉、Co粉、Sn粉的纯度均高于99.7%,粒度均小于75μm,Al粉、Cu 粉纯度高于99.8%,粒度小于45μm。
6.一种基于自蔓延反应的致密超硬磨具与钻具的快速制备方法,其特征在于,包括以下步骤:步骤1、将Al、Ti、Cu、Fe、Sn、Ni、Co粉末按照一定比例称量后放入球磨机中充分混合均匀,然后添加超硬磨料再进行混料,混料过程均在氩气保护下进行,最后获得工作层粉料;步骤2、将步骤1所获得的工作层粉料与基体一起放入压制模具中压制成型,获得超硬磨具与钻具压坯;步骤3、将步骤2所获得的超硬磨具与钻具压坯(12)与石墨压头(10)、石墨外模(11)组装后放置于工作台(15)上,所述石墨外模(11)带有观察口,超硬磨具与钻具压坯(12)外面套上双开口石英管(14),感应线圈(13)顶端位置稍低于超硬磨具与钻具压坯(12)顶端,通过压杆升降系统安装于支撑板(2)上的压杆(9)轻压于石墨压头(10)顶端,所述压杆升降系统由丝杠(3)螺母(6)副、导轨(4)滑块(5)副、驱动电机和减速机(7)、支撑板(8)组成,支撑板(2)固定于承重台(1)上,通过感应线圈(13)加热压坯(12)钢基体和石墨外模(11)使热量迅速传递给压坯(12)工作层从而引发自蔓延反应,在自蔓延反应刚结束反应产物还处于红热时通过该压杆升降系统使压杆(9)施压于石墨压头(10)顶端从而获得致密超硬磨具与钻具。
7.根据权利要求6中所述基于自蔓延反应的致密超硬磨具与钻具的快速制备方法,其特征在于,步骤1中所述球磨机转速为100~200r/min,球磨时间4~7h,球料比为1:5–1:8,钢球和粉料总体积不超过球磨罐体积的50%。
8.根据权利要求6中所述基于自蔓延反应的致密超硬磨具与钻具的快速制备方法,其特征在于,步骤2中所述超硬磨具与钻具压坯的压实密度为理论密度的50–90%,所述压制模具材料为Cr12MoV,压力大小为20~350MPa。
9.根据权利要求6中所述基于自蔓延反应的致密超硬磨具与钻具的快速制备方法,其特征在于,步骤3中所述感应线圈(13)通过的电流频率范围为1KHz~200KHz。
10.根据权利要求6中所述基于自蔓延反应的致密超硬磨具与钻具的快速制备方法,其特征在于,步骤3中所述压杆升降系统可以由气缸或液压缸、方向阀、压力阀、流量阀、导轨(4)滑块(5)副、支撑板(8)组成。