摘要 “纳米技术概念”在第九届中国国际机床展览会上[1],温特苏尔公司推出的具有“纳米技术概念”的NandWin磨具发人深思,其结合剂是带有纳米涂层的重结晶玻璃结合剂602W,在陶瓷结合...
“纳米技术概念”在第九届中国国际机床展览会上[1],温特苏尔公司推出的具有“纳米技术概念”的NandWin磨具发人深思,其结合剂是带有纳米涂层的重结晶玻璃结合剂602W,在陶瓷结合剂磨具制造过程中,在结合剂内生成类似的玻璃晶链,不仅可提高磨具的强度,适应高速磨削,而且更重要的是可以减少磨具中的结合剂,提高磨具孔隙率,同时还可避免磨屑的粘附,使磨具性能得到很大提高。
一、纳米胶体动压空化射流抛光加工实验研究
射流抛光是在20世纪90年代发展起来的一种新技术,它以流体为抛光工具,被认为是当前加工复杂表面硬脆材料制品最有潜力的方法之一[2]。初期射流抛光技术利用磨料射流,在1998年荷兰Fahnle O W等人将磨料射流抛光应用于光学表面加工,待得到了粗糙度值Ra5nm的工作表面[3]。之后,Messelink Wilhelnms A C M等进行了液体射流抛光加工球面实验,新得出在抛光过程中材料去除速度取决于磨料的锋利程度及其动能大小的结论[4]。
国内王建生认为磨料射流加工磨料粒径为喷嘴直径的1/3—1/4比较合适。苏州大学方慧研究了影响磨料射流抛光效果的主要工艺因素和加工机理[5]。朱洪涛研究了磨料射流抛光机理,认为材料的去除主要依靠磨料粒子的冲蚀作用,水射流仅起辅助作用[6]。
近期,哈工大宋孝宗等人提出纳米颗粒胶体射流抛光,以及纳米颗粒胶体溶液代替普通磨料,得到了粗糙度低于Ra0.6nm的超光滑表面[7,8]。
纳米颗粒胶体射流抛光是利用纳米颗粒与工件表面之间的界面化学反应实现工件材料的去除,材料的去除是在原子尺度范围内,所以避免了机械作用材料去除方法无法避免的缺点,如亚表面损伤,成表层原子晶格破坏等[9]。
但是,纳米颗粒胶体射流抛光的加工效果过于低下,为了提高纳米颗粒胶体射流抛光的加工效果,王星等人考虑将空化现象引入纳米颗粒胶体射流抛光,以达到对工件的高效加工并取得优质的超光滑表面,因此提出了纳米胶体动压空化射流抛光。
图5.1是实验所用的加工系统示意图。
整个系统分为两个部分:液压系统为加工提供所需压力,纳米胶体系统依靠液压系统提供的压力实现对工件加工。
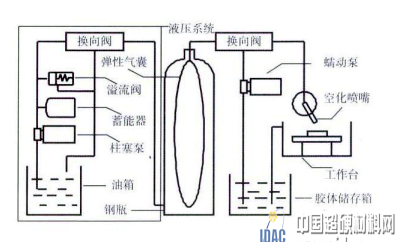
图5.1 实验系统简图
图5.2是普通射流和空化射流场空化现象的模拟结果。结果显示,旋转射流喷嘴产生的空化区范围广,而且第二相(空化)体积分数的高达86.9%,各空化区第二相体积分数都在20%以上;而普通锥形喷嘴喉部边缘形成一定量的空泡,其流场空化现象并不明显。
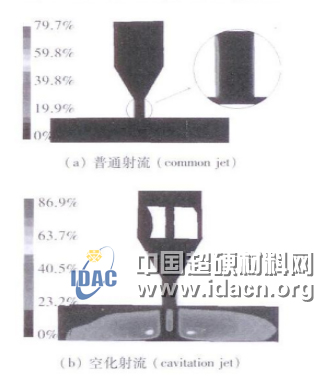
图5.2 喷嘴流场模拟图
观察两种抛光方法的轮廓发现,无论是普通锥形喷嘴抛光还是旋转喷嘴抛光,抛光压区域中心处的材料去除均较少,去除最深处位于距抛光中心位置距离相等的圆环地带。测量加工区橫截面轮廓的最低点与未加工表面之间的垂直距离,得到2h内加工材料去除深度。其结果如图5.3所示。空化射流抛光2h所达到的去除深度为0.26μm;普通射流抛光的去除深度略小,为0.23μm。
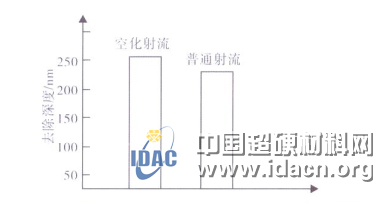
图5.3 空化射流抛光和普通射流抛光加工2h的去除深度
用原子力显微镜对加工表面进行检测,发现有在同一加工区域中,粗糙度较高的位置在工件材料去除较少的中心区域,而去除最多的圆环处的表面粗糙度值最低。分析认为,造成这种结果的可原因可能来自于抛光液流动状态的影响[10]。二、低熔高强纳米陶瓷结合剂粗粒度超硬工具
在烧结超硬工具的冷却过程中,超硬颗粒的收缩小于结合剂的收缩,故在结合剂中产生拉应力,如图5.4所示。
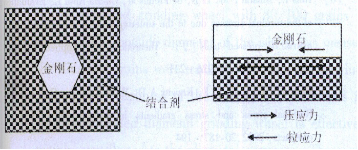
图5.4 超硬工具颗粒—结合剂界面应力分布示意图
传统的超硬材料工具以金属和树脂结合剂为主,由于金属和树脂具有良好的塑性和韧性,产生的拉应力远小于其抗拉强度极限,并且通过一定的塑性变形可以缓解和松弛应力;但是对于脆性的传统陶瓷结合剂来说,由于其抗拉强度比较小,没有塑性,内部分布的拉应力会对陶瓷结合剂的强度造成严重损害,使结合剂与超硬磨粒界面处易产生微裂纹,甚至烧结块碎裂造成工具废品。因此,研究结合剂—磨料界面应力的分布规律,缓解或消除界面应力,对陶瓷结合剂超硬磨具的大范围应用具有举足轻重的意义。为改善传统陶瓷结合剂的抗拉性能,减轻颗粒-结合剂界面应力及避免高温对超硬磨料的伤害。张向红,王艳辉等[11]将纳米技术引入到陶瓷结合剂中,在陶瓷结合剂基体中引入纳米级的颗粒、片晶、晶须和纤维等第二相,开发研制出一种新的纳米陶瓷结合剂,降低超硬磨具的烧结温度,缓解磨料—传统陶瓷结合剂界面应力问题。
试验所用陶瓷结合剂有两种类型:传统结合剂和纳米结合剂,用来对比研究结合剂—超硬磨料性能,其化学成分如表5.1所示。
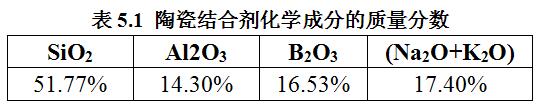
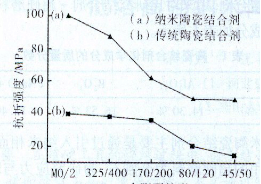
图5.5 金刚石粒度对陶瓷结合剂金刚石复合材料强度的影响
结论:(1)随着超硬磨粒颗粒变粗,结合剂金刚石界面积累的拉应力增大,试样抗折强度下降。
(2)纳米陶瓷结合剂与传统陶瓷结合剂相比,在相同实验条件下具有较小的界面结合应力,进而提高了试样抗折强度。
(3)工业化应用的实践证明,采用纳米陶瓷结合剂可以大幅度提高制品强度、韧性和耐磨性,实验结果的稳定性和重现性良好,并成功获得了工业化应用。
三、纳米SiO2改性金刚石柔性磨轮磨削性能的研究
抗拉强度参照GB/T2568-1995,试样形状尺寸如图5.6所示。
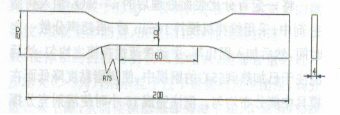
图5.6 抗拉强度试样形状尺寸图
拉伸剪切强度参照GB7124-86,试样形状尺寸如图5.7所示。
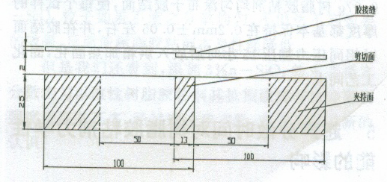
图5.7拉伸剪切强度试样形状尺寸图
1 超声分散时间对树脂胶粘剂力学性能的影响
纳米粒子在树脂基体中的分散均匀性是其作用效果的决定因素,而分散均匀性主要是由超分散时间来决定的。
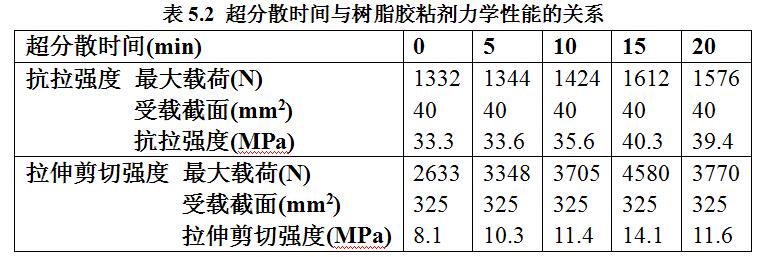
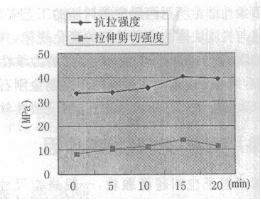
图5.8 超声分散时间与树脂胶粘剂力学性能的关系
由图表可知,当n-SiO2加入量为树脂总量3%时,树脂胶粘剂抗拉强度随超声分散时间呈先升后降的趋势,当超声分散时间为5min时,其抗拉强度与未经超声分散试样的抗拉强度相差不大,这是因为超声分散时间过短,起不到提高分散均匀性的效果;当超声分散时间为15min时,其抗拉强度达到最大值为40.3MPa,提高21%。这是由于在超声波震荡时产生了空化现象,液体介质中微泡的形成及伴随能量释放的瞬间内有强烈的振动波,液体中空气泡的快速形成和突然崩溃产生了短暂的高能微环境,由此产生的局部高温、高压或强冲击波和微射流等,可较大幅度地弱化纳米粒子间的纳米作用能,有效地防止纳米粒子团聚而使之充分分散,从而使n-SiO2在树脂基体中充分发挥其尺寸和表面效应,使其抗拉强度大大提高;但并非超声分散时间越长其作用效果越好。实验结果显示,当超声分散时间为20min时,其抗拉强度较15min时有所下降,这是因为连续超声时间过长,超声空化时产生过热超声搅拌,使体系的温度升高,随着热能和机械能的增加,颗粒的碰撞几率也增加,反而导致进一步的团聚,使抗拉强度降低。
而对于拉伸剪切强度,随着超声分散时间的增加,其强度也随之呈先上升后下降的趋势,在分散时间为15min时也达到最大值为14.1MPa,最大拉伸剪切载荷为4580N,比未超声分散时增加将近75%,这也是因为n-SiO2的小颗粒增强抗张强度,而聚合收缩力减小,使树脂与钢片表面粘结强度提高,然而随着超声分散时间的延长,反而使纳米粒子团聚增加,纳米粒子对树脂作用减弱,从而导致拉伸剪切强度反而降低。
2 纳米材料添加量对力学性能的影响
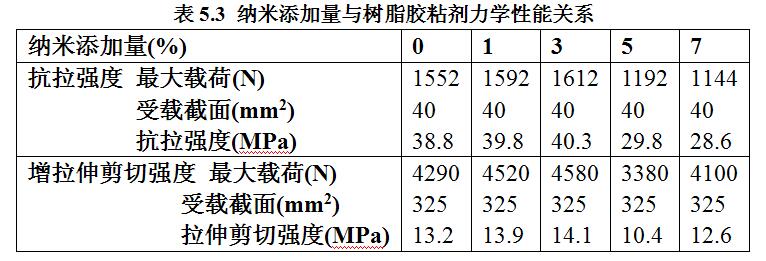
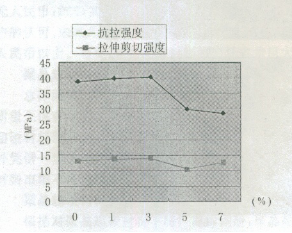
图5.9 纳米添加量与树脂胶粘剂力学性能关系折线图
由图5.9可知,随着n-SiO2添加量的增加,其抗拉强度和拉伸剪切强度都基本呈先升后降的趋势,在n-SiO2添加量为3%时其抗拉强度与拉伸剪切强度均达到最大值,分别为40.3MP和14.1MPa,较未添加n-SiO2时分别增加4%和7%,这同样是由于n-SiO2粒子表面具有众多的活性基团,易与高分子中的不饱和键发生化学键合,增强了两者之间的界面结合,在低含量时,n-SiO2在体系中充当物理交联点,增加了复合体系的交联密度,从而使体系的剪切强度增大。同时还发现,添加n-SiO2的量为3%时,如果不进行超声分散或分散时间太短,其抗拉强度和拉伸剪切强度反而较未添加n-SiO2时更低,这说明,添加n-SO2粒于如果不使之分散均匀,不但达不到想要的效果,反而使树脂胶粘剂本身性能降低。
3 纳米改性对含金刚石试样的力学性能的影响
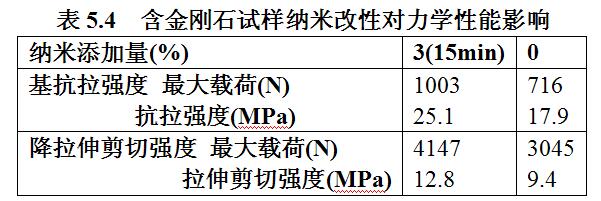
4改性前后金刚石柔性磨轮磨削性能对比
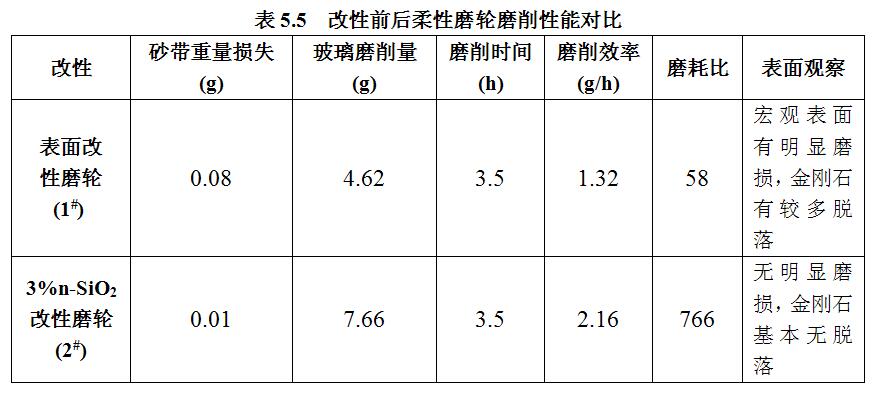
结论:
1 采用TL-2铝锆偶联剂改性纳米SiO2,当纳米SiO2含量为3%时,经过10min机械搅拌后,超声分散时间为15min时树脂胶粘剂具有最佳抗拉伸强度和拉伸剪切强度,较未超声分散时分别提高近21%和75%。
2 当分散工艺为机械搅拌10min,超声分散15min,纳米SiO2添加量为3%时,具有最佳抗拉强度和拉伸剪切强度,分别较未添加时提高4%和7%。
3 以胶料比为2:1加入w40金刚石后,经3%纳米SiO2改性胶粘剂抗拉伸强度提高40%,拉伸剪切强度提高36%,因而对含金刚石试样的力学性能具有明显的改性效果。
4 采用3%纳米SiO2改性后的丙烯酸树脂胶粘剂配制的金刚石柔性磨轮较未改性金刚石柔性磨轮前3.5h磨削性能有大大提高,同时证明了胶粘剂力学性能与金刚石柔性磨轮磨削性能的相对应性[12]。 (本文节摘自王光祖教授《超硬磨具制备与应用》第五章)