摘要 选自《智能制造:未来工业模式和业态的颠覆与重构》,【德】奥拓·布劳克曼著一个没有相应流程的产品本身就相当于是垃圾。在过去被人们定义为生产结果的产品,如今是生产流程带来的产物。所以产...
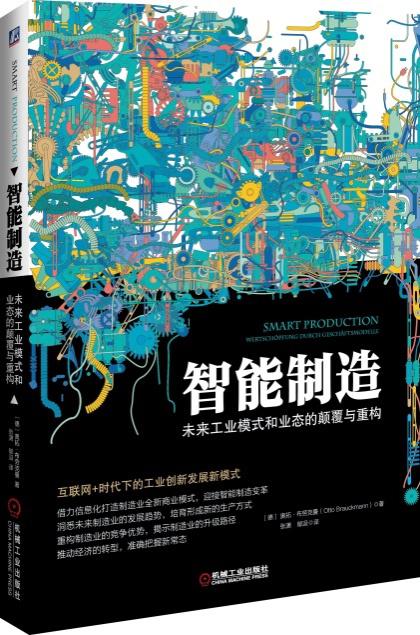
选自《智能制造:未来工业模式和业态的颠覆与重构》,【德】奥拓·布劳克曼著
一个没有相应流程的产品本身就相当于是垃圾。在过去被人们定义为生产结果的产品,如今是生产流程带来的产物。所以产品的市场力和经济性都是基于流程的。但是生产流程的逻辑是不一样的:相对于传统的生产参数来说,流程是可以计算的,而它所代表的经济性并不是基于流程时间,而是基于流程的连接点。一个没有任何误差的多个流程之间的完美交接是不存在的。每一个有可能发生的错误,在某一时刻都会发生。只要在整个合作中有一点错误发生,就会影响到整个流程。整个流程链的可靠程度是跟连接点的数量,以及每一个点的安全性(分散程度、重复精准度和可计划性)相关的。连接点的管理引发了新的思考,在ISO 9001 ff/TS 16949 标准中有定义:“在组织中一系列流程的运用,加上这些流程相互间作用的识别和管理,可以被视作是以流程为导向的方法。”(ISO 9001 ff)以流程为导向的方法所拥有的优势之一,就是可以持续调控各个单独流程之间的链接(ISO 9001:2000)。
单件及整体收益
流程的顺序逻辑与生产过程的顺序逻辑肯定是不一样的,生产过程只是将每个生产步骤所需要的时间进行简单的累积。我们用一个简单的掷骰子的游戏来说明这个区别。

图1掷骰子和流程成功率的对抗
我们一共前后掷5次骰子,并将2点到6点定义为无瑕疵产品,而只有1点定义为次品。这样我们每次掷骰子的时候平均会有5/6的可能性成功,也就是83%。而5次掷骰子的平均成功可能性也同样为83%。如果我们来看5次掷骰子的连续成功可能性的话,也就是连续5次掷骰子都成功,那么连续成功的可能性就只有39%了。也就是说发生错误的可能性要达到61%。每次掷骰子发生错误的可能性会叠加在一起。
把上面的案例放在生产中去看,就意味着即便我们有一台成功生产率在83%的机器(这个成功比例算不错了,现实中的金属加工行业比这个值要低不少),在连续5个生产步骤之后只有39%的可能性会得到一件成功的产品,有61%的可能性会得到次品而需要重新加工。这个极其简单的案例告诉我们,即便只有5个生产步骤,也就是只有4个步骤交接点,流程的成功率也会大幅度的下降,隐藏了巨大的改善潜力。
所以说生产的效率取决于流程链的复杂程度、交接点的数量以及单个流程的不同类型。不同的类型代表着流程结果会有分散性,会降低流程重复性的准确度,并有可能使流程更难以计划。效率低的流程所消耗的资源,如没有计划的等待和停泊时间,远远高于生产效率低所消耗的资源。因为对于后者来说,潜力已经几乎被开发完了,几乎所有的企业都拥有现代化的生产技术。而相比较而言,流程方面的提高潜力是非常巨大的。企业的经济性是取决于流程的交接点的。
所以ISO 9001标准根据流程之间的配合定义了生产效率。“企业如果想高效率地运作,就需要将大量相互之间有联系的活动识别、控制以及引导。”(ISO 9001 ff)虽然很多企业都签署了这项协议,但是根据标准的流程控制却很少有人在真正地做。
再重申一遍这条在ISO 9001 ff标准内的引用:“以流程为导向的方法所拥有的优势之一,就是可以持续调控各个单独流程之间的链接。”(ISO 9001:2000)
案例模型——装配机器
图2给出了一个装配机器流程的案例,这个案例同样也可以放到其他的流程中去。装配流程有8个前提条件,如机器准备程度、员工准备程度、材料齐备程度、工具齐备程度等。装配流程的成功取决于每一个单独步骤的成功。每一个单独的步骤和条件都带来了出错的风险:机器还没有准备好、工具还没有准备好、材料还没有备齐等。
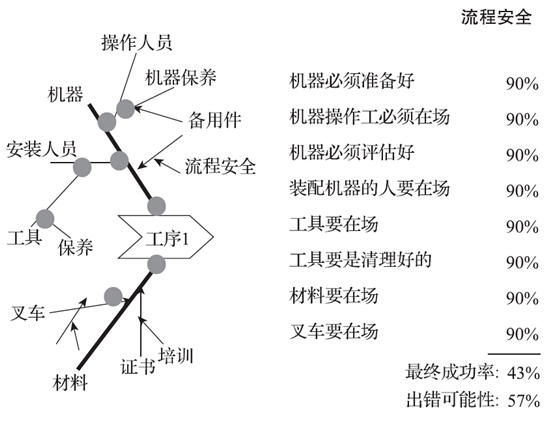
在图2中,我们假设流程的8个前提条件,每一个的平均成功率都在90%。即便只有8个前提条件,并且每一个条件的成功率都相当高,最后流程的整体成功率也只有43%,57%是会出现问题的。或者换一种表达方式:100次装配机器的流程中有57次需要被中断,只有43次可以按照计划完成。这个43%的比率叫作流程成功率,或者如果是流程链的话则被称为FPY(First Pass Yield,流程一次成功的比例)。
这个通过将每一步的成功率相乘得到的总成功率在现实中也是被广泛应用的。造成这个成功率的原因则是无处不在的延误:要么配置机器的人生病了、要么材料还没有配齐、要么工具还没有准备好等。失败步骤代表着效率下降,而企业的资源却仍然被占用着。失败步骤还伴随着大量的后续费用,如生产过剩(停泊时间)或者生产不足(等待时间)。
生产效率和方差
流程分散性(如可利用性)对于企业的经济性起着至关重要的作用,图84显示了基于现实的生产关系(Rehbehn和Yurdakul,2003)。图84中显示的是Siemens公司分析的流程分散程度(分散指数Sigma)和出错成本的关系。
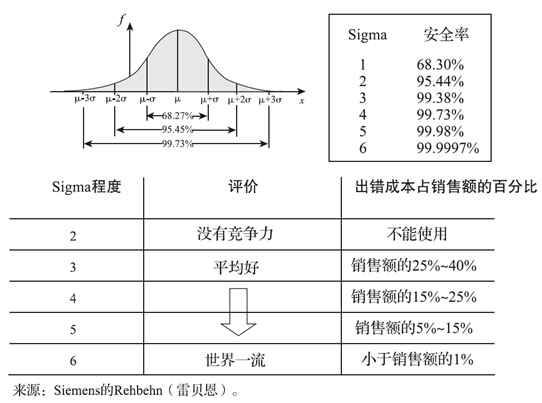
真正现实中的企业流程一般要面临上百种不同的前提条件。作者认为流程安全级别在2σ(流程每一步的成功率达到95.44%)是没有竞争力的。图3中的最后一栏显示了流程的安全级别σ与生产成本的关系。流程在交接点的分散性越小,错误造成的损失也就会越小。
Sigma(σ)是用来表示流程分散性的,σ级别可以看作是生产经济性的一个重要指标。图84中的数据是基于真实的生产条件统计出来的。数据表明,即便流程拥有非常高的99.38%的成功率,也仍然有25%~40%的销售额是要用来支付流程中发生的错误的。通过这些数据可以看出,σ级别的提升对于经济性的提升是具有非常明显的作用的。这里列举的失败成本与3.5%的机械和电子行业企业的平均税后收益率相比,是高得难以置信的。
结论:从流程角度来看生产率的话是基于方差以及流程连接点的。流程中的方差对经济性的影响比技术和生产对经济性的影响要高出以20为倍数的级别。“如果想要将企业的效率提高,也就是将生产效率提高以及成本降低,那么达到6σ级别将是最佳选择。”(Walch,2005)
隐藏的工厂
对于企业的员工,尤其是生产线上的工人来说,公司的价值流和成本计算不是可以被直接认识到的。一个跟流程密切相关并且实时更新的记录和计算并没有运用到实践中。在实践中运用得更广泛的只是操作之后的记录,并且也只记录那些可以计数或者测量的参数。而对于实际消耗了多少资源并没有一个明确的认知。单位成本是很难去统计的,而因为等待和停泊所浪费的时间资源也会一直有各种合理的借口。例如,当一名工人需要将装配机器的流程中断时,他的潜意识里并没有觉得这个会影响到生产效率,因为他觉得机器反正会“立刻”接到下一个任务继续运作,并不会影响到效率甚至是经济性。另外还要注意到,在生产循环中库存量的增多反而会使员工更为镇定。因为如果很多箱子都装满了货物,就会有一种企业运营良好的暗示,也使工作岗位更加的稳定。但是事实上所有没有计划的生产中断都会导致看不见的浪费,就如同接下来的案例所展示的一样。
对于企业中没有被认知到的程序,波士顿大学管理学院教授米勒和福尔曼取名叫作“隐藏的工厂”。因为这些间接的部分其实隐藏了很多生产力(Müller,1992)。
停泊比生产还要贵
图2显示了一个装配机器的流程,整个装配流程有8个前提条件。流程链的效率参数是FPY,即流程一次成功的比例(Rehbehn和Yurdakul,2003)。图4将图2的内容再次加深,当8个流程步骤的每一步都有90%的成功率时,最后总的成功率在43%。换句话说,每100个计划的装配流程中会有57次因为各种原因需要中断并无法继续进行。中断具体代表着等待材料、等待工具、等待工人等。这同时也代表着工具又要被拆掉并且放回仓库,其他的资源也一样,如材料以及其他配件(测量工具、检测报告等)。接下来需要安排新的任务,并检查可行性,因为FPY风险也是同样存在的。在某些情况下,中断还会带来其他的费用,如紧急的状态、特别的班次或者是加班,甚至到要坐上直飞Wolfsburg(沃尔夫斯堡)的直升机。所以说因为中断造成的等待或者停泊是比生产更加昂贵的。
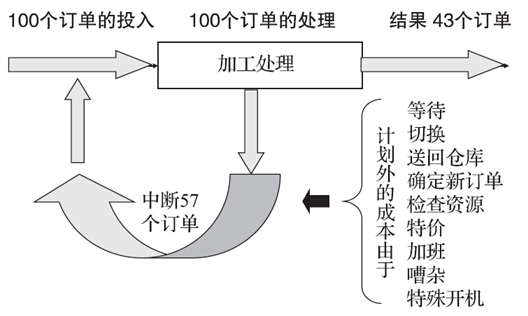
因此,上文提到的机器的使用率与材料的等待和停泊时间是没有关系的设想根本就是错误的。
损失计算
生产流程会按照顺序形成一套完整的事件。在每一个流程交接点都会有影响流程准确性(分散性)的风险,如太多、太少、太早、太晚、错误的地点、错误的质量等。针对面对的差异和应有值之间的联系以及由此造成的损失,Taguchi(田口)研究出了一种计算损失的方法。这种方法可以计算出差异(即便是误差范围之内允许的差异)所代表的损失。虽然Taguchi一开始是刻意参照比较可靠的设计来开发这个方法,并且主要用在技术加工领域的,但是他的方法同样可以很好地转接到其他的流程上来。Taguchi主要强调了单个目标变量的分散性:对于客户来说,产品的可使用性随着误差的增多而持续地下降。
一个过程在计划中的误差范围不能够看作是生产误差临界值,而要看作损失来计算。根据以下陈述:每一个流程目标的误差带来的损失,是根据误差的大小成平方倍数增长的。流程目标可能是时间(产品完成)、地点(运输目标)、数量(生产过度或者生产不足)或者质量(额外检测、重新加工、销毁)。
每一个实践中的工人都知道:“总有意外会发生的。”不是缺材料、机器没准备好,就是工人生病了,或者工具不齐。每日典型的影响包括计划外的生产中断、未能按计划生产并引起等待或者停泊时间、模具准备工作无法完成等。根据这些问题,流程操作的一个目的就是尽量采取能够减少这些错误根源的措施。
除了交接点安全性的提升,还有交接点的数量(也就是复杂性)对于损失的计算也是很关键的。如果在图1中那个掷骰子的案例里不是5个骰子而是10个骰子的话,或者按照生产流程来说不是5个生产步骤而是10个的话,那么最后得到的成功率就只剩下16%了,况且其实10个步骤对于现实中的企业运营来说根本不算多。步骤的数量同时也代表着可能发生错误的数量(Opportunity for Defects,发生错误的数据)。这个案例说明了,流程不能在整个过程结束之后再来评判,因为这时已经太晚了,而是需要在过程中(伴随生产过程)就开始调整(Rehbehn和Yurdakuhl,2003,第52页)。