1、引言
近几年随着光伏太阳能市场的发展变化,太阳能电池不断地向高效率低成本发展。考虑到硅片方面产业规模的扩张以及成本增长的压力,业内不断寻求高效率低成本的硅片切割方式。现国际光伏行业晶体硅片的切割方式主要有两种。一种是砂浆切割,即利用涂有碳化硅和油浆的多根不锈钢细钢丝(SW)丝环绕在驱动轮和紧张轮上高速转动,以聚乙二醇和碳化硅微粉为主体的磨削浆料高速带入切割区域并对磨料施加载荷,磨料对硅料进行磨削切割。另一种是金刚石线(DW)切片,即采用电镀或树脂固定的方法将金刚石颗粒镶嵌在不锈钢丝上,这种不锈钢丝高速运转以一定的压力对硅料进行磨削切割。从电池制作工艺角度比较,砂浆切割对硅片表面摩擦断裂损伤剧烈,会使硅片表面出现较多小而不规则凹坑(如图1),容易导致后续清洗制绒工艺复杂且控制不稳定,金字塔绒面变化范围大,单片金字塔绒面均匀度差,成核率低。
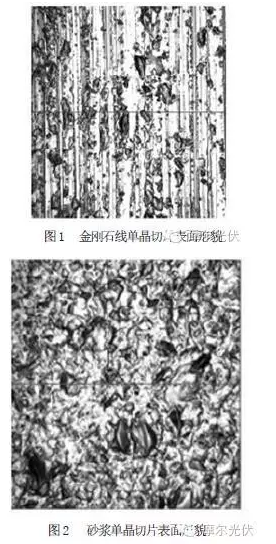
基于以上金刚石线切割硅片的种种优势,金刚石线切片制绒工艺的研究很有必要。本文通过在目前单晶硅片清洗制绒工艺的基础上从工艺流程和药液成分上尝试调整,研究适合单晶金刚石线切片的制绒工艺。
2、实验
2.1实验原料及仪器
实验的硅片为金刚石线切割的太阳能级P型单晶硅片156mm*156mm,电阻率为1-3Ω·cm。实验用化学品NaOH、异丙醇、表面活性剂、HF等化学试剂都为电子级,实验所用设备捷佳创单晶碱制绒机、RENA酸制绒机、反射率测试为HITACH公司的
D-4100球型积分测试仪。金字塔结构由扫描电镜进行观察,型号为S-4800、光学显微镜ScopeA1。
2.2实验过程
单晶金刚石线切片以采用金刚石颗粒镶嵌在不锈钢丝上不断循环磨削切割形成,切割工艺的不同导致硅片表面形貌如断裂损伤等有较大的区别,故硅片外观不同于常规砂浆切片(图1、2)。
如图砂浆切片表面呈现较多不规则损伤凹坑,金刚石线切片表面存在较多塑性磨削切割形成的光滑切割纹俗称线痕,单片硅片上这种光滑割纹占据约65%的面积,在腐蚀液中腐蚀速率较慢,所以一般砂浆单晶硅制绒工艺不适用于该金刚石线切片。
2.2.1方案一提高碱腐制绒液浓度
目前最广泛用于生产的单晶硅制绒工艺体系为碱液腐蚀晶硅<100>面,具体为质量浓度约1.3%NaOH溶液,有效降低溶液表面张力增加硅片浸润性并帮助反应产物氢气泡脱附的IPA,用于优化金字塔大小和成核密度的表面活性剂,水浴温度75℃~82℃,反应时间1000s~1500s简称单晶常规碱制绒体系。对于金刚石线单晶切片制绒尝试在此工艺基础上提高腐蚀液NaOH的浓度至1.7%~2.3%,同步降低添加剂用量约15%。
目的在不影响生产产量的情况下提高金刚石线切片的腐蚀速率以有效去掉硅片表面损伤层,并能形成大小良好、成核密度良好的金字塔(如图3)。其表面线痕仍较明显。
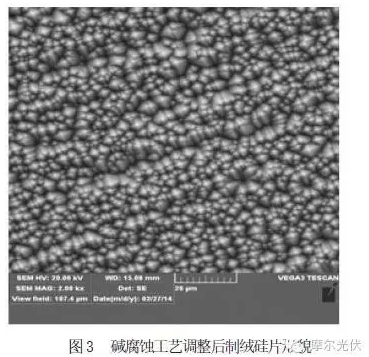
以上制绒工艺后仍不能有效去除金刚石线切片的线痕,然而这种线痕很容易引发丝网印刷不良。故尝试在腐蚀制绒前采用碱抛的方式优先去除线痕,然后采用以上提到的单晶常规碱制绒体系进一步进行金字塔生长。
第一种用质量浓度约8%NaOH,温度65℃碱腐蚀液粗抛3mins后用去离子水冲洗(如图4);第二种用质量浓度约12%NaOH,温度65℃碱腐蚀液粗抛8mins用去离子水冲洗后再进行常规碱制绒(如图2.2.3方案三酸液腐蚀后再碱液制绒对金刚石线切片表面形貌观察发现硅片上每条塑性光滑切割纹之间均会有少量摩擦断裂损伤处,这种损伤处与切割纹底部形成粗糙度差,所以腐蚀速率有较大差异。
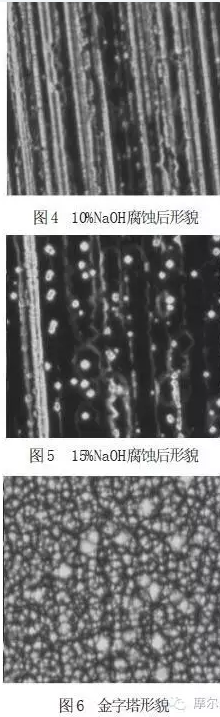
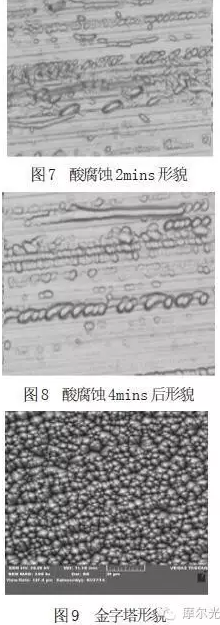
3、讨论
以上三种不同方案处理后,单晶硅金刚石线切片均可不同程度的制出金字塔。
方案一利用单晶硅常规各向异性碱腐蚀处理后该硅片可以形成大小均匀、成核密度较高的金字塔群,但切割痕不能有效去除硅片表面仍然存在依线痕而起的高低金字塔,平整度较差不利于丝网印刷。方案二工艺处理复杂,需经质量浓度8%NaOH与浓度12%NaOH两种高浓度碱腐蚀液做抛光腐蚀后前者线痕消除仍不明显后者减重较大线痕消除效果较好。但随着碱液腐蚀抛光的加剧硅片表面呈现阶梯状六面体,再在单晶常规碱制绒体系中腐蚀,金字塔粗糙度极大。方案三利用HF-HNO3酸制绒体系对切割造成的断裂损伤进行各向同性腐蚀(156mm*156mm硅片腐蚀量约0.18g~0.25g)缩小光滑切割纹底部与断裂损伤面的粗糙差异,用去离子水冲洗后再对其进行单晶常规碱制绒体系腐蚀制出大小均匀、粗糙度较好、成核密度高、光学显微镜观察硅片表面无明显线痕的单晶硅绒面。对各工艺制绒后硅片用HITACH公司的D-4100球型积分测试仪测试反射率(如图11),结果证明方案三反射率最低。
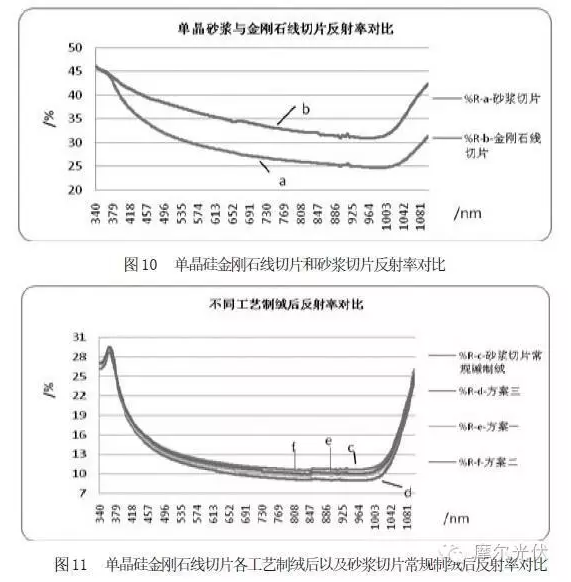
本文通过在常规碱制绒体系的基础上调整碱浓度、反应时间,甚至增加前处理工艺等不同角度尝试对单晶金刚石线切片进行制绒,发现当仅仅是在原工艺的基础上提高碱浓度、延长反应时间不能有效去除硅片表面切割线痕不利于印刷;当对该硅片碱抛光后制绒,减重较大且制绒后金字塔粗糙度极差不利于印刷;当对该硅片进行酸腐后再制绒,可以有效去除硅片表面线痕,制绒后金字塔成核密度高、粗糙度较好,硅片表面绒面平整度好利于印刷。