HPM75无磁钢的加工分析
HPM75无磁钢这种特殊材料因为它的合金成分中含有大量合金碳化物,这样使得无磁钢基体强化。但是我们切削机加工中所用到的普通钻头和刀具耐热、耐磨性较差,硬度也相对来说较低。
刀具在对HPM75无磁钢进行切削速度较低时,材料的切削底面和刀具的前刀面在切削过程中形成化学活性很高的材料新表面。材料表面在高温、高压的作用下,就会产生积屑流。积屑流在材料表面有相对的稳定性,但是当切削过程中振动或负荷不均匀时,积屑流则会脱落产生刀具磨损。超出刀刃的积屑流,将替代刀刃进行切削,这样一来就会在已加工好了的材料表面留下痕迹,影响加工精度。
而HPM75无磁钢模具件在钻削过程中受至剧烈的加压和冲击压力时,无磁钢的奥氏体组织容易转变为细晶粒的马氏体,无磁钢材料的硬度也就由原来的200HB(约20HRC)提高到550HB(约55HC)左右。在摩擦与挤压形成的高温下材料表面易形成高硬氧化层(Mn2O3),同时也使得材料导热率很低(约为S45C模具钢的25%),散发热量少。这样一来钻头易退火,产生切削刃口的压溃,从而影响刀具寿命。
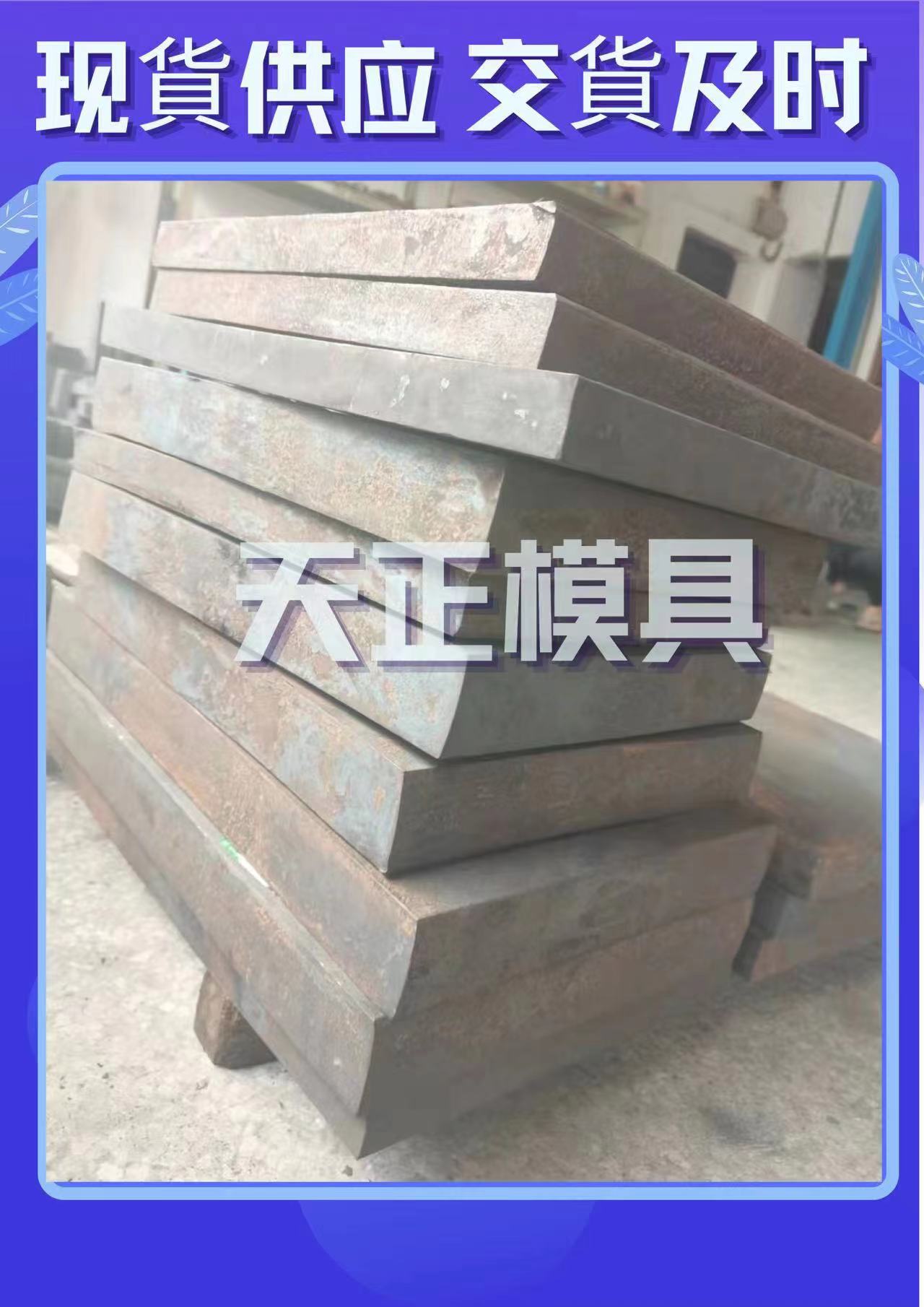
车削工艺
HPM75材料是高锰无磁钢属于高硬度、难切削的特殊钢材,加工过程中高速切削过程中易产生崩碎切屑,这样一来就会导致切屑力度就集中在刀刃旁边的很小面积上,而局部压力就很大,有一定的冲击性。
所以HPM75无磁钢的加工刀具应选抗弯强度和韧性较好的C-Co合金钢刀。由于无磁钢切削过程中很容易产生冷作硬化,所以选择刀具前角大、后角小、刃弧半径小的刀片,以此来降低切削力避免材料塑变严重。
钻削工艺
HPM75无磁钢钻削加工中,钻头直径的选择主要是根据加工伯孔径尺寸确定,根据产品实际需要通常为某一定值,而不参与优化。因此钻削工艺优化主要从影响刀具耐用因素考虑,即钻头材料、角度、进给量及冷却方式等。